VTT: Five percent of spare parts could currently be stored in digital warehouses.
Emerson sweetens bid for Rockwell Automation to $29 billion
Can US Boost Manufacturing 25% By 2025?
Test Drive Watson IoT in Factory Simulation
3D Printer Farms And Robotics Start Pointing To Future Of Manufacturing
Britain must embrace 'Industry 4.0' as robots can create thousands of jobs, says report
3D Systems outlines additive manufacturing strategy, aims for turnaround
Rockwell Automation Invests in Artificial Intelligence (AI) for Industrial Automation
3D printing doubles the strength of stainless steel
The Rockwell Automation Bidding Starts at $27 Billion
Webalo Launches No-Code App Generation Platform for IIoT
Is Google Glass Staging A Comeback?
Adidas is using robots to produce small-batch, local-market shoes
Veo Robotics raises $12 million to help machines and humans collaborate more efficiently
Apple and GE just put iOS inside Industry 4.0
Records 781 to 795 of 1199
First | Previous | Next | Last
Featured Product
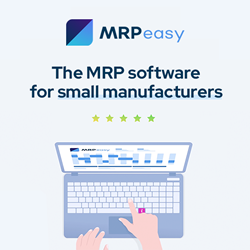