The challenge isn’t just about maintaining quality; it’s about doing so at scale. With skyrocketing volumes of data, a shrinking workforce, and rising costs, companies are looking for smarter solutions. That’s where AI and ML come in.
When Machines Teach Machines: AI and ML in Remote Condition Monitoring
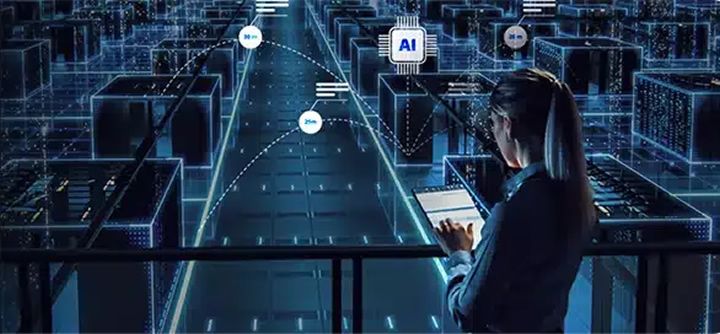
Article from | Fluke
Remote condition monitoring has never been more important — or more challenging. Today’s industrial operations are larger, faster, and more data-driven than ever before. Traditional methods of vibration analysis and manual diagnostics, once the gold standard, are struggling to keep up with modern demands.
The challenge isn’t just about maintaining quality; it’s about doing so at scale. With skyrocketing volumes of data, a shrinking workforce, and rising costs, companies are looking for smarter solutions. That’s where artificial intelligence (AI) and machine learning (ML) come in. These next-generation tools are already shaping how companies approach predictive maintenance.
Azima DLI, with decades of expertise in vibration analysis and condition monitoring, is at the forefront of this critical transformation. As an advanced AI- and ML-driven solution, Azima tackles the overwhelming complexity of modern condition monitoring — turning mountains of machine data into actionable insights and reshaping how failures are predicted and prevented.
How does Azima make it possible to handle more data with fewer resources and higher stakes — all without compromising on precision? It starts with thoroughly understanding the challenges and presenting novel solutions that give businesses an edge, despite limitations.
The Growing Challenges in Remote Condition Monitoring
What happens when you need to analyze twice as much data with half the workforce? Or when even a minor diagnostic error could cost millions in downtime? These aren’t hypothetical scenarios — they’re the reality of modern condition monitoring.
- A Shrinking Workforce and Rising Costs
The ongoing shortage of skilled labor continues to reshape the industry. Experienced vibration analysts are retiring faster than new professionals can be trained, leaving a critical expertise gap. Meanwhile, operational costs continue to rise, putting additional pressure on teams already stretched thin. The result is a growing need for tools that ensure analysts focus their time and expertise on the most urgent cases, rather than routine evaluations that don’t require human oversight. - The Data Deluge
Modern condition monitoring systems are generating an overwhelming amount of data. In 2024, Azima processed just under one million machine tests — and will likely process two to four times more information over the next few years thanks to advances in data acquisition and storage. While capturing data has become easier, managing and making sense of it is a much greater challenge. The sheer volume of information makes it impractical to rely on manual analysis alone. Analysts must quickly identify meaningful patterns and separate critical faults from background noise, all while making certain nothing important is missed. - Zero Tolerance for Failure
In today’s high-stakes environments, there’s no margin for error. Companies monitor machines that are critical to production lines, and even brief periods of downtime can lead to significant financial losses. We can’t sacrifice quality — not even slightly. Failures on high-value machinery or production lines are incredibly costly, and our goal is to prevent them before they happen.
Traditional condition monitoring methods were never designed for this level of complexity. Without a shift toward smarter, scalable solutions, the gaps in resources and precision will only continue to grow.
Azima’s Blueprint for Smarter, Faster Remote Condition Monitoring
Closing the gaps in modern condition monitoring requires more than just scaling up; It demands a smarter approach. Azima is leading the way in turning a data deluge into streamlined, actionable diagnostics with AI and ML.
Automating Expertise with EADS
One of the ways Azima addresses the complexity of modern condition monitoring is through the Expert Automated Diagnostic System (EADS). At its core, EADS is an expert system, a subclass of AI that processes and encapsulates human knowledge into logical, rule-based frameworks to enable automated decision-making.
EADS is built on 6,000+ diagnostic rules designed to replicate how skilled vibration analysts interpret machine data. These rules encode decades of expertise, covering everything from misalignment identification to rotor bar fault detection. By automating this knowledge, EADS transforms what was once a manual and time-intensive process into one that’s fast, consistent, and highly precise.
EADS is more than just a rules engine; It contextualizes machine data to deliver meaningful insights. Azima takes high-quality vibration data from sources like online systems, wireless sensors, or portable devices and pairs it with a comprehensive asset definition. This ensures that diagnostics account for the machine’s full operational context. Is the data from a centrifugal pump, a multi-stage gearbox, or a VFD motor? How is the machine train configured? What are the torque transmission paths, and which bearings are being monitored?
This understanding is further sharpened through use of historical baselines — datasets representing the healthy state of similar machines. When a new machine comes online, its condition is often unknown — whether it’s perfectly healthy or already showing signs of wear. To address the uncertainty, Azima’s system searches its data warehouse for similar machine pairings, such as a motor coupled to a centrifugal pump, to provide an initial point of comparison. Drawing on over 50 years of vibration data analyzed by world-class experts, Azima has created one of the industry’s most extensive repositories. This legacy of data not only supports precise diagnostics but also gives Azima a significant edge in the condition monitoring space.
Even when a machine’s historical data isn’t available, EADS can borrow baselines from comparable equipment. This allows the system to compare incoming data against known healthy states, delivering diagnostics, repair recommendations, and additional metadata almost instantly. This automated process significantly reduces the time required to establish baselines for new programs, cutting commissioning time from months to just weeks. By enabling fast, accurate comparisons against healthy states, EADS ensures reliable diagnostics from day one.
Scaling Analyst Focus and Capacity
EADS also enables smarter and more efficient use of human expertise. Traditionally, vibration analysts could handle 20–25 machine tests per day. With automation, that number has surged to 175 tests per day per analyst — and there’s room to go higher.
Approximately 80% of machines operate without issues, yet traditional monitoring requires analysts to spend time on these healthy systems. With EADS, 93% of machine tests are screened for indications of faults without human intervention, freeing analysts to prioritize the review of critical data.
Additionally, analysts play a vital role in refining the system itself: validating flagged results, assessing fault severity, and intervening in edge cases to prevent false positives. This feedback loop ensures that diagnostics remain accurate and adaptable to real-world conditions while allowing analysts to focus on impactful, complex diagnostics instead of repetitive tasks.
By combining automation, contextual understanding, and human expertise, EADS scales analysts’ capacity to manage more machines while maintaining the precision and reliability that modern operations demand.
Advancing Diagnostics with Machine Learning
Azima uses ML to uncover patterns and relationships in vast datasets that are too complex — or too subtle — for traditional methods to detect.
At the heart of this process are two approaches: supervised learning and unsupervised learning. In supervised learning, algorithms are trained on labeled datasets, mapping inputs like vibration spectra to specific outputs like loose rotor bars. By leveraging millions of labeled datasets in Azima’s archives, these models can detect fault patterns that may otherwise go unnoticed. In cases where data lacks labels, unsupervised learning algorithms condense the information, using methods like clustering and dimensionality reduction to reveal meaningful groupings in data that are otherwise unapparent to the naked eye.
This capability solves real-world challenges like missing machine-specific details — the number of motor bars in equipment, for example. Many users don’t know this parameter, yet it’s essential for accurate fault detection. Azima developed an algorithm capable of identifying motor bar patterns directly from vibration spectra, allowing the system to infer this missing information automatically. Our engineers also automated the identification of pump related forcing frequencies as well, including pump vanes and pump threads.
These innovations proved invaluable in one case where a motor was initially flagged for severe bearing wear, which typically requires a costly overhaul. However, when Azima’s system applied its advanced algorithm, it uncovered the true issue: loose rotor bars. By pinpointing the root cause, the system recommended a targeted motor circuit analysis instead of an unnecessary overhaul, saving both time and significant costs.
Of course, using ML effectively requires careful balance. Models that are too simple can miss critical patterns (underfitting), while overly complex ones may fail in real-world conditions (overfitting)—a challenge known as the bias-variance trade-off. Additionally, poor-quality data can compromise results, underscoring the importance of clean, well-labeled datasets. With over 50 years of organized vibration data, Azima ensures its models are trained on the reliable, high-quality data needed for consistent performance.
By integrating ML with EADS, Azima has created a diagnostic system that doesn’t just automate — it learns, adapts, and delivers actionable insights to tackle even the most complex challenges.
Building Trust in Data: From Collection to Anomalies
As we saw in the previous section, clean, reliable input data is critical for even the most advanced AI and ML models to deliver actionable insights. The old adage holds true: garbage in, garbage out. But machine data is rarely straightforward. Variations in how it’s collected, processed, or even distorted by anomalies can complicate the path from raw information to actionable insights.
Azima’s approach tackles these challenges head-on by integrating diverse data sources and detecting anomalies before they skew results. This transforms raw machine data into a dependable foundation for precise diagnostics.
- Simplifying the Way You Collect High-Quality Data
Data collection shouldn’t be a roadblock to better diagnostics. Whether you’re using the Azima TRIO portable vibration analyzer or Treon wireless sensor, Prüftechnik’s online VibGuard devices, or GE’s wireless Ranger Pro sensor, Azima brings all your data together on one platform for analysis. No matter how the data is collected or where it’s analyzed, Azima eliminates the hassle of fragmented systems, turning diverse data streams into a single, actionable source for precision monitoring. - Catching Anomalies Before They Become Problems
Machine data isn’t always perfect — sensors can overload, data spikes can occur, and one-off errors can easily distort diagnostics. That’s why Azima has built its systems to recognize and address anomalies before they lead to unnecessary repairs or wasted time.
For example, if a sensor becomes overloaded and produces distorted readings, Azima’s system flags it immediately. Instead of triggering false alarms or incorrect recommendations, the system recognizes the issue as a data artifact and prompts a retest.
The same applies to unexpected spikes in waveform data. Whether caused by something as simple as a bumped sensor or a random external event, these anomalies are caught and flagged for review.
With this approach, Azima saves analysts from chasing false positives, streamlining the diagnostic process, preventing unnecessary repairs, and keeping operations focused on what truly matters.
Smarter Systems, Smarter Decisions: What’s Next?
Remote condition monitoring is changing, and cutting-edge technology is making new analysis methods possible. Azima’s combination of automation, machine learning, and decades of expertise is simplifying complex data and turning it into something you can act on. By catching problems early, cutting down costs, and freeing up your team for more critical work, smarter systems are helping businesses stay ahead — even as resources tighten and the stakes grow higher.
Author bio: Austin Anderson, Product Owner for Azima DLI condition monitoring.
The content & opinions in this article are the author’s and do not necessarily represent the views of ManufacturingTomorrow
Comments (0)
This post does not have any comments. Be the first to leave a comment below.
Featured Product
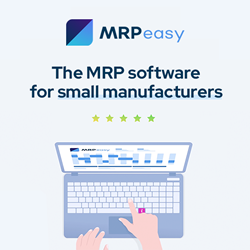