Penn Waste realized that it needed an advanced wireless solution combined with smart sensors that would deliver accurate, reliable and continuous real-time data for predictive maintenance.
Penn Waste Inc. Minimizes Machine Downtime and Improves Efficiency
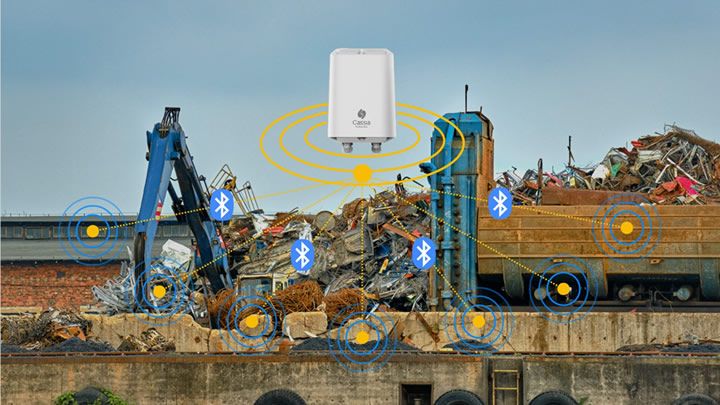
Case Study from | Cassia Networks
BACKGROUND
Founded in 2000, Penn Waste Inc., a locally operated and managed company focuses on providing South Central’s Pennsylvania with residential and commercial waste management services. The company’s recycling facility processes over 180,000 tons of material each year to promote a cleaner, more sustainable environment. Their strong commitment to environmental and social causes makes them the premier choice of residential and commercial waste management and recycling services in the state.
CHALLENGES
Penn Waste’s state-of-the-art recycling facility and modern equipment allowed the company to expand its sorting and recycling capabilities to process recyclables more efficiently and at a faster processing speed resulting in less contamination. One major challenge the company was facing was premature failure on their DRS glass breaker machine which is used to separate glass from mixed recyclables. These highly specialized machines are typically situated in very dirty areas of the facility where other items (i.e., coat hangers, stringed bags, etc.) can get caught in the bearings and wrap around the bearing shaft causing damage to the seal. Consequently, this leads to the premature wear of the bearings and shortens its life span.
A second challenge Penn Waste faced was the manual intervention and ongoing inspection of these machines to ensure their optimal uptime. This required several maintenance technicians spending multiple hours performing onsite inspections and cleaning the debris from the machines to reduce the risk of bearing failure.
When bearings would fail, additional labor was required to investigate the severity of the problem, disrupting many of their day-to-day business operations.
SOLUTION
Penn Waste realized that it needed an advanced wireless solution combined with smart sensors that would deliver accurate, reliable and continuous real-time data for predictive maintenance. The company discovered an opportunity with Cassia Networks and Dodge Industrial and decided that the combination of Cassia’s Bluetooth Gateways (X2000/X1000), IoT Access Controller (AC) and Dodge’s Smart Sensors was the ideal solution to help overcome their challenges. The company’s goal was to continuously monitor the bearings of their machines to accurately predict failure without resorting to frequent manual inspection.
Long-Range, Multiple Device Connectivity
Penn Waste installed multiple Dodge smart sensors on the DRS glass breaker machine to adequately cover all necessary bearings and gearboxes. In addition, multiple Cassia Bluetooth gateways (X2000/X1000) were deployed in the area to continuously receive data from the sensors and send this data to the cloud. Cassia’s outdoor/indoor X2000/X1000 gateways provide long-range connectivity up to 1000 feet (in open space) and the ability to pair and connect up to 40 Bluetooth Low Energy (BLE) devices simultaneously per gateway. The long- range connectivity and ability to pair and connect multiple sensors simultaneously was a critical requirement for this deployment.
Simple, Scalable and Flexible
The combination of Dodge’s Smart Sensors, Cassia’s X2000/X1000 Gateways and IoT AC provided Penn Waste with a flexible and easy-to-use wireless solution allowing them to deploy at scale. The process of installing and commissioning the smart sensors took less than three minutes. Once the sensors were paired to Cassia’s gateways and a reliable internet connection was made, the gateways were able to seamlessly push data to the cloud. The simplicity of this wireless solution provided Penn Waste with the advanced tools they needed to access data anytime to proactively identify any maintenance requirements and prioritize labor tasks accordingly.
RESULTS
By using Cassia’s X2000/X1000 gateways, IoT AC and Dodge’s Smart Sensors, Penn Waste gained the real-time visibility needed to accomplish their objectives - reduced machine downtime, reduced overall costs and improved efficiency.
Reduced Machine Downtime
Before installing Dodge’s smart sensors and deploying Cassia’s X2000/X1000 gateways, Penn Waste would average nine bearing failures in a ten-month time frame. After installing the sensor gateway platform, the company has had zero machine failures and achieved a 95% uptime in machine performance. The ability to continuously monitor the temperature and vibration levels of the DRS assets provides the granular data and insights the maintenance managers need to accurately predict when and where problems were occurring. By taking a proactive approach to machine maintenance, Penn Waste was able to significantly reduce machine downtime and improve efficiency.
Significant Cost Savings
Since deploying Cassia’s X2000/X1000 gateways and Dodge’s Smart Sensors, maintenance managers can remotely monitor machine health without the need for frequent on-site inspection in these harsh environments. This allowed Penn Waste to ensure workplace safety and redirect labor to other mission-critical tasks in the facility. Furthermore, the predictive maintenance approach to machine monitoring allowed maintenance managers to address any equipment downtime issues to improve the overall efficiency of their assets and reduce any operational costs associated with repairing and/or replacing these specialized and costly machines.
Maximizing Uptime for Improved Business Operations
For Penn Waste, managing and maintaining complex and costly equipment and processes is crucial for not only running the business efficiently and safely but also for meeting and exceeding the business’ bottom line. By installing Dodge’s Smart Sensors and Cassia’s X2000/X1000 gateways, maintenance managers have around the clock real-time visibility into asset performance resulting in maximized uptime for their machines, improved business operations and a greater ROI. By integrating predictive maintenance into their wider digital maintenance strategy, Penn Waste has captured the value from both increased uptime and reduced maintenance and labor costs.
Cassia’s X2000 gateways were simple to use and install and stood to the test in these harsh environments as well as providing the long-range connectivity we needed. What one wants from any wireless technology is dependability, efficiency and durability. Cassia’s gateways and Dodge’s smart sensors have given us just that.
— Joe Wojciechowski, Maintenance Manager at Penn Waste Inc.
ABOUT CASSIA
Cassia Networks is the leading provider for enterprise Bluetooth IoT products and solutions. Our patented technology provides the most reliable and easy to manage long-range, multiple device connectivity, edge processing and locationing for Bluetooth IoT networks.
Our mission is to solve the IoT connectivity, locationing and management challenges faced by today’s enterprises and make IoT easy.
To learn more about Cassia’s products and solutions, please visit www.cassianetworks.com or contact us at sales@cassianetworks.com / support@cassianetworks.com.
For more information about Dodge Industrial, please visit www.dodgeindustrial.com.
The content & opinions in this article are the author’s and do not necessarily represent the views of ManufacturingTomorrow
Comments (0)
This post does not have any comments. Be the first to leave a comment below.
Featured Product
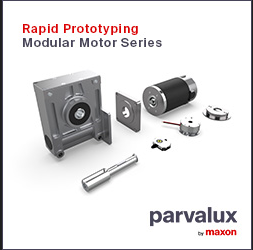