Additive Manufacture: In-house 3D Printing versus Outsourced 3D Printing Service
In this 3-part series of articles, we will embark on a comprehensive exploration of 3D printing / additive manufacturing (AM), where our main focus is empowering you to make informed decisions about how to engage with the technology across an ever-evolving landscape.
Winds Of Change For Vestas: 3D Printed Tooling Transforms Wind Turbines
There aren't a lot of technologies that can propel towering wind turbines to new heights of time and cost efficiencies, but large-format additive manufacturing rose to the challenge and delivered with its eclectic range of applications.
How to Create A Good Technical Drawing
Make sure your drawing undergoes all quality assurance and approval procedures. A drawing that is easy to follow and clearly defines your requirements is one of the first steps to a successfully manufactured part.
Manufacturing Impact: Rising Consumption of Entertainment Drives Demand For 3D Animated Content
The augmented demand for the technology from several industrial verticals due to the increasing use of simulation in the design of industrial tools by OEMs has facilitated the penetration of 3D animation solutions worldwide
Why Binder Jetting?
Besides being fast and capable of manufacturing complex shapes, binder jetting systems are also incredibly accurate.
Dynamic Micro-CT: Moving beyond 3D into 4D
In general, dynamic micro-CT is ideal for obtaining much more complete 3D information throughout a process and provides researchers with a lab-based capacity to collect data during testing without discrete interruptions―true in situ testing.
Model-based enterprise as a trigger to Digital Transformation
When it comes to industrial and manufacturing design and engineering, here we speak about low paced movement from 2D drawings to 3D models which are definitely more informative, easy-to-use and more adaptable to changes.
3D modelling technique for fast-track face shield production
Using stacked model data, the technique can dramatically increase 3D printing output, assisting in producing face shields for healthcare workers fighting COVID-19.
CRP Technology and Windform® Materials for 3D Printing are Driving AM Revolution
Some of the most advanced industry - as Automotive - are experiencing a renaissance not seen before, which is driving engineers to find new, innovative, cost-effective solutions using professional 3D Printing, mainly.
MODEX Q&A - Emulate3D
This year at MODEX we'll be highlighting CAD Is The Model technology, which enables system designers to mark up their solutions in SOLIDWORKS and Autodesk Inventor and create articulated and dynamic systems for emulation testing.
Booth #7869
Case Study: Phase Four Launches Scalable Electric Propulsion (EP) System with Xometry
This innovative California-based aerospace company is revolutionizing space exploration with Maxwell, its mass-producible EP system. Xometry is the manufacturing platform that's bringing its exoskeleton from its 12-page drawing to life.
GE Additive & Kaspar Schulz Q&A - Additive Manufacturing: there's always something brewing!
This year we wanted to go a layer deeper and explore the potential that additive technology could have on the brewing and beverage industry.
Rockwell Automation Acquires Emulate3D, a Leading Software Developer for Simulating and Emulating Industrial Automation Systems
Software portfolio integrates automation software with 3-D CAD model, enabling customers to test machine and system designs virtually
Onshape Teams Up with Magic Leap for New Spatial Computing CAD App
New product design app to offer live collaborative 3D CAD editing, not just viewing
Redefining Product Development Using Cutting-Edge 3D Metrology Solutions
How GE Appliances uses ATOS 3D scanners, TRITOP photogrammetry, and ScanBox automated technology to solve engineering challenges.
Records 1 to 15 of 38
Featured Product
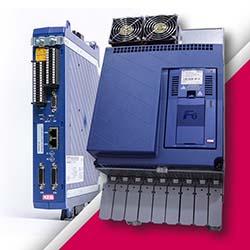
KEB VFDs for High Speed Motor Control
KEB's VFDs are the key to unlocking peak performance in your high-speed machinery. Engineered for precision control, even without feedback sensors, our F6 and S6 drives utilize advanced software and high-frequency output. This ensures smooth operation, reduced vibration, and optimal efficiency. Whether you're building turbo blowers, power generation systems, or other high-speed applications, KEB VFDs deliver the reliability and performance you need.