NANO DIMENSION’S TERA 250vx ENHANCES ACCUMOLD’S MICRO INJECTION MOLDING SERVICE
Today, Micro-Additive Manufacturing (Micro-AM) solution like the Tera 250vx from Nano Dimension can additively manufacture or 3D print micro parts and components only previously possible through the use of micro injection molding, and it can be done in a way that reimagines both the design possibilities and economic factors.
Accumold, located in Ankeny, Iowa, USA has been at the forefront of innovation in micro injection molding for nearly 40 years, and has recently invested in two Nano Dimension Tera 250vx Micro-AM 3D systems. The rationale behind investing in Micro-AM was largely driven by the objective of reducing product development time given traditional micro molding consists of a number of time-consuming stages including mold design, CAM programming, CNC set up and machining, and EDM (Electric Discharge Machining) etc…
The process for the traditional means of manufacturing can take 4-6 weeks to produce a mold, and assumes no additional iterations with each adding at least another two weeks. This is especially punitive for high mix, low volume applications whereby the cost and time taken for mold fabrication makes applications unjustifiably and prohibitively costly.
Nano Dimension’s Tera 250vx has provided a welcomed antidote to the existing challenges. The Micro-AM system has a build volume of 50 x 50 x 100 mm, builds parts in 1-10 micron layers, exhibits optical resolution of 4 microns, has a tolerance accuracy of +/-2 microns, and achieves 0.4 micron surface roughness (Ra). For Accumold, therefore, the path to the creation of innovative miniaturized parts at amazing speed and reduced cost was open for the benefit of its customers.
ACCUMOLD’S USE OF MICRO-AM
At Accumold, the Tera 250vx is used to print micro-sized prototype parts and injection molds, and therefore decreases time-to-market for its customers, while at the same time stimulating the creation of parts with geometric complexity impossible using traditional micro injection molding technologies. It is fair to say that success for Accumold through the use of the Tera 250vx is measured in microns and hours. Micron-level detail can be achieved without the need to fabricate molds, and this means that intricate and geometrically complex prototypes can be produced in a matter of hours.
Accumold found some of the greatest benefits in aiming for complex geometries. With conventional method, increased complexity comes increased cost, but not when using the Tera 250vx Micro-AM technology.
The use of the Tera 250vx also optimizes workflow, and promotes the reduction of iterative processes, assembly, and inventory. This means that significant operational cost benefits are now attainable at the micro manufacturing level.
Micro 3D printed molds can be used by Accumold to injection mold real parts. This unlocks new business possibilities for mold makers and manufacturers who up until this point have been restricted to the use of long lead time and expensive traditionally manufactured mold tools for the achievement of any volume of molding, from prototype runs all the way through to mass manufacture. The business case for a process chain that includes printed molds, with dramatically shorter lead times at reduced cost is compelling.
REAL TIME CASE STUDIES
The following case studies demonstrate the use of micro AM in real customer scenarios, but due to the proprietary nature of the work images of parts cannot be used.
Case Study 1 – Intraocular Implant. The first example is a medical OEM customer making an intraocular implant that measures 1.6 x 2.9 x 0.7 mm. The customer was up against a looming FDA submission deadline. The part design included a small gap on one side of the part. While the rest of the part design was pretty much frozen, the customer needed to determine what size gap would be optimal for the part considering that in its final assembly it would need to be accurately handled and safely implanted inside the eye.
Due to the micro size of this part, Accumold could print many samples using the Tera 250vx’s 50mm x 50mm x 100mm printing area. The company successfully printed multiple samples of six different designs for the customer to test. This took less than 24 hours to design, print, post process, package, and ship out to the customer, which was able to complete their testing in about two weeks. Their tests proved one of the designs to be superior to all others, and this was the design the company froze and submitted for FDA approval.
If Accumold had not been able to provide multiple part iterations for testing at one time, the customer would have had to delay their FDA submission or choose a design without adequate test data. Once the customer was satisfied with its test performance, Accumold could start to design and build the production tool so that it could qualify the tool and scale up to meet production volumes.
Case Study 2 – Implant Tip. Another of Accumold’s medical device customers needed to finalize an implant tip design measuring 1.5 x 3.0 x 2.5 mm before the design freeze date. The customer needed a frozen design so that they could kick off tooling and not push out their overall project timeline. Using the Tera 250vx Accumold was able to print 16 different tip designs for the customer to evaluate. A lot of parts could be built in the Tera 250vx print envelope, and the first print included 10 samples of each of the 16 design iterations. It took less than 24 hours to design, print, post process, package, and ship the parts to the customer, which completed its testing in a few weeks and came back with 6 different modified designs for another round of testing. Accumold’s second print was turned around in about one day so the customer could quickly resume testing.
Case Study 3 – Valve Assembly. A medical customer that was trying to finalize the design of a valve assembly measuring 9.0 x 9.0 x 10.7 mm came to Accumold. This valve was comprised of a softer material overmolded on top of a harder machined part. The valve needed to maintain a seal while being rotated within the final assembly.
Accumold’s first round of samples was molded with a TPE (thermoplastic elastomer) material. Testing found a few dimensions out, so the mold CAD models were updated, and new molding inserts printed a day later. The second round of mold inserts worked better but the TPE was too rigid when rotating it in the test assembly. The same printed inserts were used to mold parts in a TPV (thermoplastic vulcanizate) resin. The TPV parts performed better in the test assembly, but some leakage was observed. Sources of the leak were identified, the CAD models were modified, and another set of molds were printed. This final set produced valves that could be easily rotated in the assembly and did not leak.
From start to finish Accumold was able to test three different printed mold designs and two materials in about two weeks. The customer was extremely pleased with the results.
SUMMARY
All of the successful case studies discussed would not have happened without the Tera 250vx Micro-AM technology being used as a central enabler in the product development process. Fundamental to the success of the Tera 250vx is that it brings the benefits of AM to micro manufacturers for the first time, including hitherto impossible part complexity (enhancing design and functionality), minimized or no tooling costs, minimal set up costs, the ability to mass customise and personalise products, and the ability to produce mold inserts within a day. As a versatile technology appropriate for prototyping, small batches, and potentially even mass manufacturing, the technology is now stimulating innovation in the micro manufacturing sector, and is truly changing the economics of manufacturing.
Comments (0)
This post does not have any comments. Be the first to leave a comment below.
Featured Product
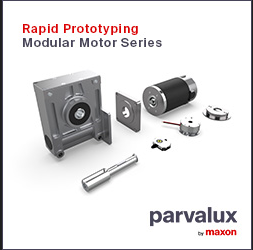