THE ROLE OF MICRO MOLDING IN THE PRODUCTION OF MICRO-OPTICS
Achieving the exacting tolerances required for these delicate micro-optic parts necessitates a deep and specialized processing knowledge that is distinctly different from that used for typical mechanical parts.
THE IMPACT OF 3D PRINTING ON MICRO MOLDING - A SYNERGISTIC APPROACH
The precision achieved in micro molding is not just about miniaturization, it's about reproducing complex shapes with exacting tolerances that are measured in microns repeatably.
NANO DIMENSION'S TERA 250vx ENHANCES ACCUMOLD'S MICRO INJECTION MOLDING SERVICE
Today, Micro-Additive Manufacturing (Micro-AM) solution like the Tera 250vx from Nano Dimension can additively manufacture or 3D print micro parts and components only previously possible through the use of micro injection molding.
The Critical Role of Risk Mitigation & Vertical Integration in Successful Micro Molding
Alex Anderson, Sales Engineer at Accumold systematically explores the crucial implications of vertical integration in micro molding projects.
The Challenges of Boomerang Projects in Micro Molding: a Customer Perspective
In the world of micro molding, where precision and efficiency are paramount, the concept of boomerang projects can present significant challenges for both customers and micro molders.
OPTIMIZING OUTCOMES THROUGH MICRO MOLDING - AN EXPERT PERSPECTIVE
In this Q&A interview, Craig Tappe, Sales Engineer at Accumold discusses various aspects of the micro molding process, and discusses why it is important to ensure that when short-listing your preferred suppliers, the correct questions are asked.
MICRO MOLDING - PLACE THE FOCUS ON OUTCOMES
You need to understand what micro molding can do in terms of stimulation of innovation, what it can deliver in terms of manufacturing efficiency, and what - above all - it can do to achieve increased functionality in parts that are often required to be smaller and smaller
How Micro AM is Impacting Time-to-market for Precision Plastic Parts
When using micro AM, by week 7 a design can have been refined numerous times as the process requires no traditional tooling, just DRST. This means that time and focus in this early stage of product development can be spent on design optimization.
Tolerance Attainment in Micro Molding
When manufacturing micro parts and components, it takes a coordinated team of experts in design, materials, tooling, molding, validation, and automated assembly to successfully manufacture customer parts at high volume.
Micro Molding - Material Selection and Design Concerns
You need to understand the basic design approach and really bottom out what you can and cannot do, as when micro molding, even the smallest design change can be catastrophic and completely derail a project.
The Critical Role of Validation in Micro Molding
Measurement should be a central consideration in every quote issued by a micro molder. If a micro molder can make the steel micro tool, and subsequently mold the part, sure as night follows day it will need to be measured.
MICRO MOLDING - THE TOOLROOM PERSPECTIVE & DfMM
DfMM has a massive impact on the tool build; this will therefore have a disproportionate effect on product development time, cost, and indeed the quality of final product.
Micro Molding & Microfluidics - Overcoming Complexity Issues
Microfluidics is an extremely dynamic niche today, and will continue for many years to cement the importance of micro molding as a technology used to drive innovation in the medical sector in such applications as drug delivery devices, implants, and diagnostics
MICRO MOLDING FOR MICRO-ELECTRONICS
Perhaps like no other, the field of microelectronics exemplifies the drive towards miniaturization, the obvious reduction in size of everyday household appliances and cell phones showing the extent to which products containing electronic components have been reduced in size.
Records 1 to 14 of 14
Featured Product
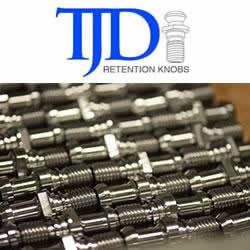
T.J. Davies' Retention Knobs
Our retention knobs are manufactured above international standards or to machine builder specifications. Retention knobs are manufactured utilizing AMS-6274/AISI-8620 alloy steel drawn in the United States. Threads are single-pointed on our lathes while manufacturing all other retention knob features to ensure high concentricity. Our process ensures that our threads are balanced (lead in/lead out at 180 degrees.) Each retention knob is carburized (hardened) to 58-62HRC, and case depth is .020-.030. Core hardness 40HRC. Each retention knob is coated utilizing a hot black oxide coating to military specifications. Our retention knobs are 100% covered in black oxide to prevent rust. All retention knob surfaces (not just mating surfaces) have a precision finish of 32 RMA micro or better: ISO grade 6N. Each retention knob is magnetic particle tested and tested at 2.5 times the pulling force of the drawbar. Certifications are maintained for each step in the manufacturing process for traceability.