Integrating Heat Pumps in Industrial Processes: 5 Notable Changes
Sustainability requirements have led manufacturing companies to scrutinize their operations and find environmentally friendly alternatives to current machines. Some professionals have chosen to integrate heat pumps into their industrial processes due to their increasing efficiency.
How have heat pumps changed to help manufacturers? What innovations can industry professionals expect? Here’s a guide to the evolution of heat pumps and how they affect the modern manufacturing landscape.
How Have Heat Pumps Changed to Aid Industrial Processes?
Like most technologies, heat pumps have evolved to become more efficient and user-friendly. With today’s devices, manufacturers can use heat pumps to aid their industrial processes because of these five improvements.
1. Lower Leak Risk
For decades, manufacturers have used heat pumps while risking leaks inside their factories or warehouses. Heat pumps suffer from wear and tear and internal components can break down. For instance, operators may see cracks in the rubber seals or weakened copper coils essential to the device.
Modern heat pumps have improved their risk of leaks by requiring less refrigerant for leaks. Additionally, newer devices have electronic leak detection for continuous monitoring. This feature is essential for manufacturers wanting to implement automation into their operations.
Reducing the risk of leaks is crucial because of how toxic refrigerants can be to humans and the environment. Experts say modern refrigerants are over a thousand times more polluting than carbon dioxide (CO2).
2. Increased Sustainability
While heat pumps have long been an eco-friendly choice for manufacturing professionals, their sustainability has increased to comply with environmental regulations.
Most companies use R-410A as their preferred refrigerant because it’s a step up from R-22. R-410A’s global warming potential (GWP) concerns some industry professionals, but it’s better than R-22 because it affects the ozone layer less.
Additionally, it’s more effective in cold temperatures due to its enhanced heat absorption and lower boiling point. R-410A’s increased efficiency caused the U.S. and other nations to ban R22, considering the old refrigerant’s negative environmental impact.
3. Renewable Energy
Manufacturers have used electric heat pumps for over half a century to reduce fossil fuel consumption. While electric equipment reduces energy consumption, these devices have some CO2 liability due to the fossil fuels required to power the grid. One way modern manufacturers can lessen their environmental liability is to use renewable energy for their heat pumps.
Modern heat pumps utilize renewable energy advancements by implementing solar power and other environmentally conscious sources. These devices aren’t as widespread as electric heat pumps, but the research has been promising. A 2023 Solar Energy Advances study says solar thermal technology, including heat pumps, is essential for decarbonization and meeting industrial heat demand.
4. Higher Efficiency
While renewable energy options are entering the market, efficiency for industrial heat pumps is increasing across the board. Over time, these devices have increased their output while reducing their environmental impact.
For example, modern heat pumps have better compressors to let compressors reach adequate pressure without consuming as much power as previous devices. Technological advances have also created motor variability, allowing heat pumps to adjust their speed based on needs. Reducing power consumption and lowering emissions can help manufacturers achieve lower costs and fewer CO2 emissions.
Another advancement helping the efficiency of heat pumps is their heat exchangers. Contemporary heat pumps have started using larger exchangers, permitting more heat transfer from the air and refrigerant. Therefore, the heat pump will have an easier time directing heat.
5. Cold Weather Effectiveness
For decades, one of the drawbacks of heat pumps has been their performance in cold climates. Older devices may have seen decreased efficiency and less reliability in freezing temperatures. However, manufacturers have flipped the narrative and made heat pumps more efficient, even in frigid temperatures.
The improvements derive from the inverter-driven compressors. Increasing their variable capacity and efficiency has made them more effective, delivering efficiency even when temperatures dip below zero.
Heat pumps are just as critical in the winter when the demand for heat rises. Manufacturers must keep water in the facility warm for the sake of their machines, with most requiring temperatures of 140 degrees Fahrenheit or higher. Modern heat pumps can provide temperatures of 250 degrees Fahrenheit and higher, while heat pump systems can supply a 100-degree Fahrenheit lift.
What Technology Will Change the Future of Heat Pumps?
Heat pumps have seen numerous improvements in recent years, contributing to their effectiveness in industrial applications. The future looks promising as technology evolves and makes these devices more efficient.
For instance, researchers have developed a new refrigerant to make heat pumps more environmentally friendly. R-32 is a more sustainable hydrofluorocarbon because of its lower GWP and better recycling capabilities than R410A and R-22.
Another change manufacturers could see in the future is smaller heat pumps. With smaller devices, companies could target specific areas inside facilities and reduce wasted energy. Construction professionals have started using portable heat pumps to retrofit old buildings, considering the high cost of renovations.
What Benefits Do Heat Pumps Bring?
Heat pumps have become prominent for manufacturers due to their cost-effectiveness and environmental practicality. Here are a few benefits stemming from modern heat pumps.
1. Less Fossil Fuel Reliance
Sustainability goals have led manufacturers to adopt environmentally conscious policies. For instance, more companies have adopted electric vehicles because they have no tailpipe emissions and do not require less maintenance.
Heat pumps are a critical tool for sustainability because they run on electricity and don’t directly use fossil fuels. Advancing technology will make heat pumps more environmentally friendly as researchers harness solar power and other renewable sources.
2. Greater Efficiency
The efficiency of heat pumps is a significant reason manufacturers choose them over competitors. Older facilities may use natural gas boilers, depending on their location and the availability of this fuel source. Heat pumps provide cleaner energy and better efficiency than natural gas, making them more sustainable.
The International Energy Agency (IEA) says heat pumps are three to five times more energy-efficient than natural gas boilers if the operator utilizes low-emission electricity. Transitioning to efficient heat pumps is crucial for manufacturers as the world seeks to reduce its carbon footprint.
3. Saving Money
Heat pumps may challenge manufacturers due to their initial price. A smaller company might be unable to spend $20,000 on a reliable heat pump, so they look for alternatives instead. Manufacturers save money when looking at the cost-effectiveness of their heat pumps in practice.
For instance, heat pumps take advantage of all energy sources when operating. A device may use waste heat others would reject, thus saving money because it’s cheaper for companies. Heat pumps also save money by implementing smart thermostats, timers and similar gadgets to increase autonomy and lessen power consumption.
How Heat Pumps Are Changing Manufacturing
In the 21st century, heat pumps have become standard for manufacturers due to their effectiveness. These devices have improved to maintain efficiency and keep industrial processes moving. With sustainability at the forefront, manufacturing companies have leaned into heat pumps to decrease emissions and reduce environmental liability.
Comments (0)
This post does not have any comments. Be the first to leave a comment below.
Featured Product
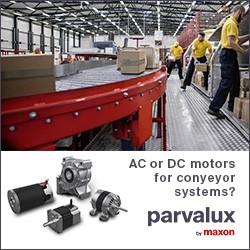