Properly managing your bills of materials can help you streamline production processes, improve material planning, and reduce costs.
BOM Management Expert Guide for Growing Manufacturers
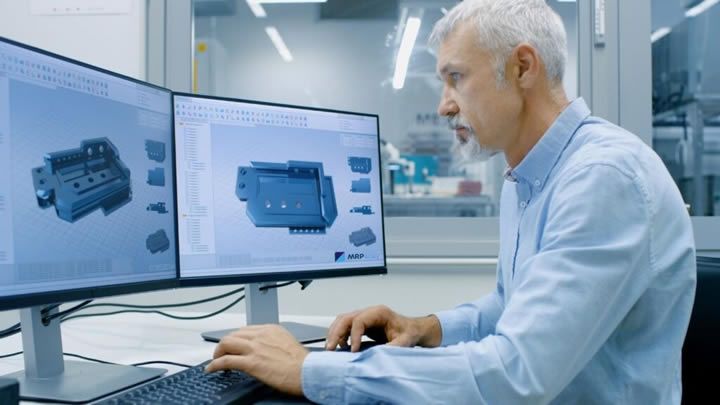
Article from | MRPeasy
What is a bill of materials (BOM)?
A bill of materials (BOM) outlines the specific components, parts, and materials required to assemble an product. It serves as a critical foundation for production planning, ensuring synchronization between inventory, procurement, and manufacturing processes.
BOMs are typically paired with production routings to create a complete "product recipe." This combines the detailed list of components with the precise assembly and quality control steps needed to produce the final product.
What is BOM management?
Creating a bill of materials (BOM) is just the beginning of its journey. BOM management extends throughout the product’s entire lifecycle and entails:
1. Creating the BOM
An efficient BOM starts with a detailed list of all components essential to assembling the product. Every component must have a unique part number, a clear description, and defined quantities.
In the case of complex products, an engineering BOM (EBOM) is first developed to reflect the product’s design. The EBOM serves as the blueprint for creating the manufacturing BOM (MBOM), which specifies how the product will be assembled and tested on the production floor. Seamlessly converting EBOMs to MBOMs ensures consistency and efficiency in transitioning from design to production.
2. Structuring the BOM
A well-structured BOM is critical, especially for multi-layered products with intricate assemblies. Depending on the complexity, BOMs can be:
- Single-level BOMs: Listing components directly related to the final product, such as a simple assembly.
- Multi-level BOMs: Detailing sub-assemblies and their respective components.
Clear structuring ensures that each part of the product is easy to track and manage during production and maintenance.
3. Adding the routing
The production routing specifies the sequence of operations necessary to transform components into a finished product. Each step outlines required machines, tools, and estimated times, enabling better capacity planning and precise scheduling for production lines.
4. Integrating the BOM with inventory
Linking BOMs with stock-keeping units (SKUs) within an inventory management system ensures accurate tracking of materials and components. For instance, if all parts are accounted for in the BOM and properly tracked, you can quickly calculate material requirements for incoming orders or upcoming periods, compare current inventory levels with your requirements, and make the necessary purchases in a timely fashion. This significantly reduces the risk of production delays due to component shortages.
5. Enabling customizations
Configurable BOMs or matrix BOMs are used to handle variations in the product design. Unlike static BOMs, these dynamic formats allow flexibility in combining components to create tailored solutions for specific customer needs or market demands. This approach eliminates the need for entirely new BOMs for every variant while maintaining BOM integrity and efficiency.
6. Recording BOM updates
BOM revisions are essential in environments with rapidly evolving product lines, where components can become obsolete or designs require optimization. Managing revisions ensures that updates are documented and seamlessly implemented without disrupting production. Detailed revision tracking allows manufacturers to identify the exact version of a BOM in use and revert to a previous iteration if necessary.
Benefits of effective BOM management
Implementing effective BOM management practices offers a range of benefits that optimize resource use and streamline production. Key advantages include:
1. Standardization and consistency
A well-defined bill of materials introduces standardization across the manufacturing process. It ensures that every stakeholder—from engineers to production teams—has a unified understanding of the components and assembly process. By clearly defining components and assembly processes, you guarantee consistent product quality and reliability across all production batches.
2. Less miscommunication between engineering and production
Effective BOM management bridges the gap between engineering and production by aligning EBOMs with MBOMs. This ensures that manufacturing teams receive clear and complete instructions for assembling products. Miscommunication is minimized, especially when outsourcing some stages of production to contract manufacturers. Everyone works from the same up-to-date version of the BOM, reducing errors and delays.
3. Effective supply chain and materials management
Precisely listing components—such as part numbers, specifications, and quantities—enables accurate sourcing of materials that meet specific requirements. Integrating BOMs with inventory management systems ensures real-time tracking of components, allowing you to:
- Forecast material needs for production runs or periods.
- Prevent stockouts of critical components.
- Avoid excess inventory that risks obsolescence.
4. Improved production planning and scheduling
With accurate BOM data, material requirements can be forecasted and aligned with production schedules. Manufacturers can plan purchases to ensure the timely delivery of components to the assembly line. Additionally, routing data can be used to account for material lead times, assembly times, and testing cycles, enabling more precise production scheduling and on-time delivery.
5. Better cost estimating and tracking
BOMs form the basis for estimating and tracking material and labor costs. When an order is placed, BOM data allows you to estimate costs for components, assembly, and testing based on order quantities. During production, material consumption and labor hours can be tracked to calculate actual costs and compare them with initial estimates. This ensures more accurate pricing and profitability analysis.
6. Better quality and reduced waste
Standardized BOMs and routings ensure consistency in how goods are manufactured, improving overall quality. For example, clearly defined testing processes can identify issues early, reducing defects. Standardized processes also minimize material waste and provide a foundation for continuous improvement in assembly and testing procedures.
7. Traceability
Effective BOM management ties finished products to specific component lots, enabling full traceability through lot tracking. For example, you can track which material lots were used in a specific products and which customers received them. This traceability is essential for identifying the root cause of defects, organizing recalls, and ensuring compliance with industry regulations.
Common BOM management issues
Even if your bills of materials (BOMs) are relatively straightforward, managing them and integrating them with inventory, procurement, and production can introduce complexities. These are the most frequent BOM management issues faced in manufacturing:
1. Inaccurate or incomplete data
Missing or incorrect information in a BOM, such as inaccurate part numbers, component specifications, or quantities, can disrupt production. This can result in delays, over-ordering, or critical shortages of components, jeopardizing deadlines and increasing costs.
2. Overly complex BOMs
For simpler products, unnecessarily detailed or multi-level BOMs can create confusion, slow down workflows, and overwhelm production teams. Streamlining BOMs to include only essential details for such products can help improve clarity and efficiency on the shop floor.
3. Poor integration with inventory systems
When BOMs are not properly linked to inventory systems, manufacturers lose visibility into stock levels and material consumption. This is especially problematic in supply chains with long lead times. The lack of integration can lead to procurement inefficiencies, supply chain bottlenecks, and production delays.
4. Lack of version control
Without robust version control, teams risk working with outdated BOMs. This could result in the use of obsolete components, procurement of incorrect parts, or mismatches between design, procurement, and production teams. Proper BOM version management is essential to maintain alignment across all departments.
5. Reliance on manual processes
Managing BOMs in spreadsheets becomes increasingly inefficient and error-prone as product complexity grows. In manufacturing, where precise data is critical, manual processes can result in miscommunication, errors in component specifications, and difficulty collaborating across teams.
The issues above can significantly reduce efficiency, increase costs, and delay time-to-market for your products. A single mistake in a BOM can lead to production stoppages, rework, or missed deadlines. The solution is to implement software for managing these critical aspects of your operation.
Managing BOMs with manufacturing ERP
All the challenges associated with BOM management can be addressed—and the benefits maximized—by implementing a robust system like manufacturing ERP (Enterprise Resource Planning) software. ERP solutions streamline the management of bills of materials (BOMs) while optimizing operations across the board.
Manufacturing ERP software integrates BOM management with critical functions like sales, inventory, procurement, production, and financial management. This automation handles countless processes, including:
- Real-time inventory updates for components.
- Revision control for updated designs or engineering changes.
- Order and cost tracking to maintain profitability and accurate forecasts.
With ERP, stakeholders gain real-time visibility into current BOM versions, order statuses, production costs, and material requirements. This transparency eliminates silos and ensures everyone is working with the most up-to-date information.
When dealing with complex products that consist of many subassemblies, or products with variations (e.g. in color or size), a robust manufacturing ERP system such as MRPeasy also provides you with the tools to manage multi-level and configurable BOMs.
With all this data centralized and easily accessible, communication between departments becomes lightning-fast and collaboration rises to a much higher standard. This streamlined exchange of information inevitably leads to more efficient shop floor and supply chain management.
For more information and a free trial, please visit https://www.mrpeasy.com/
The content & opinions in this article are the author’s and do not necessarily represent the views of ManufacturingTomorrow

MRPeasy
MRPeasy is a seriously powerful and easy to use ERP software for small manufacturers that gives you everything you need to manage your manufacturing and distribution processes. Integrating sales, procurement, inventory, production, finances, and your team, it provides you with an accurate real-time overview of your operations. MRPeasy is trusted by 1800+ small manufacturers worldwide, 700+ of which are based in the US and Canada. Our users report a 54% average improvement in the overall performance of their business and a 42% increase in on-time deliveries. Try for free, no credit card needed.
Other Articles
Scottish Chemical Manufacturer ‘Struck Gold’ with Manufacturing ERP Software
5 Most Common Small Manufacturing Challenges According to Consultants
Configurable BOMs – Simplifying the Production of Customizable Items
More about MRPeasy
Comments (0)
This post does not have any comments. Be the first to leave a comment below.
Featured Product
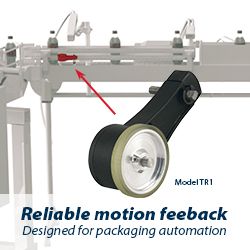