Best Practices for Safer Factories in 2024: How to Improve Material Handling Applications
In material handling applications, the safety and productivity of carts are critical factors impacting factory operations. The industry is continually looking for safer and more efficient solutions, including both improved manual processes and motorized or autonomous options. This shift is not just about adapting to current challenges but is a strategic move to enhance safety and efficiency.
Engineered caster solutions play a pivotal role. When designed specifically for the carts they're installed on, the right casters can significantly reduce push force, addressing ergonomic challenges and preventing overexertion injuries while also boosting productivity and reducing maintenance costs.
This article outlines the top tips to apply in the year ahead and improve cart safety through proper caster selection, maintenance, replacement, and training.
1. Match the Right Caster to the Machine and Load
It isn’t just a wheel. Choosing the right caster is critical to cart safety and operational efficiency – and customized casters help ensure greater productivity and fewer incidents. A caster that is not correctly specified for its intended load, ergonomic effectiveness, and durability can lead to significant problems.
The key to successful caster selection begins with a thorough understanding of the load it will bear. This involves assessing not only the weight of the load but also considering the unique characteristics of the materials being handled as well as the environment in which the cart is used. Factors like floor conditions, presence of obstacles, and even ambient temperatures can impact caster performance. Hence, a one-size-fits-all approach falls short in addressing these diverse needs.
Other factors, such as the frequency and distance of cart movement, also play a pivotal role in caster selection. For applications involving heavier loads or higher movement frequency, proper wheel material specification and motorized and autonomous casters present innovative solutions.
Advanced caster manufacturers have a selection of wheel materials available. Matching the correct polyurethane material, of which there can be up to a dozen choices, with the exact use case ensures the best tradeoff between push force, productivity and wheel life. This not only caters to the specific demands of heavy-duty operations but also significantly enhance safety. By reducing manual strain and the potential for overexertion injuries, they align with the ergonomic needs of the workforce.
2. Conduct Regular Maintenance and Inspection
The importance of routine maintenance for casters cannot be overstated, as it is vital for their longevity and safe functioning. Regularly inspecting caster wheels for signs of wear and damage is crucial in preventing accidents and maintaining efficiency. This process helps in early detection of common issues like wheel obstructions, cart overloading, and structural damage to the casters.
Promptly addressing these concerns not only minimizes the need for frequent replacements and associated labor costs but also reduces operational downtime. Furthermore, diligent maintenance contributes significantly to a safer and quieter work environment, which in turn boosts employee morale. Prioritizing such maintenance practices is essential for the smooth operation of material handling equipment.
3. Ensure Timely Replacement of Faulty Casters
The lifespan and reliability of casters are crucial for safety in material handling. Promptly recognizing when a caster requires replacement is essential for ensuring cart safety. Indicators like wear, bent, or broken components necessitate immediate action. Being proactive in replacing casters before they completely fail is a critical safety measure that helps prevent accidents. This proactive approach not only enhances safety but also boosts productivity by enabling the secure and efficient transport of loads. Regular attention to the condition of your casters is key to maintaining a safe and productive material handling environment.
4. Invest in Training and Best Practices
Ensuring employees are well-trained in best practices for material handling is essential for operational safety and efficiency. Training should focus on the correct usage of carts, understanding caster limitations, and identifying signs of wear and tear. It's Such education is a fundamental aspect of maintaining high standards of safety and efficiency in material handling.
5. Engage a Professional Consultation and Engineering Review
For complex environments or where problems persist, a site visit from a trained material handling specialist can be invaluable in identifying eronomic and productivity improvements. An engineering lab review of failed casters can provide insights into the root causes of problems and suggest improvements. This review can be a crucial step in understanding root cause issues.
6. Consider an Autonomous Solution
The material handling industry is increasingly leaning towards autonomous solutions to improve both safety and operational efficiency. To navigate this shift, it's crucial to perform a comparative analysis between autonomous systems and traditional push carts. This evaluation should factor in the facility's size, the type of materials handled, and staff availability to ascertain the most efficient and safe material handling methods. Such an analysis will guide organizations in choosing between modern automated solutions and conventional methods, ensuring both cost-effectiveness and safety in their operations. This strategic approach is key in adapting to the evolving dynamics of the industry.
In conclusion, improving the safety of carts in material handling applications is a multifaceted approach that involves proper caster selection, regular maintenance, timely replacement, comprehensive training, professional consultations, and an analysis of autonomous versus manual options. By focusing on these areas, companies can address the ergonomic, productivity, and uptime challenges posed by material movement across facilities. As the industry continues to evolve, prioritizing these aspects will be key to ensuring worker safety and operational efficiency.
###
About the author:
Doug Backinger, Senior VP, Solutions Engineering & Innovation, Caster Concepts
Doug Backinger, Senior VP, Solutions Engineering & Innovation, brings a well-rounded background of outstanding leadership and engineering expertise to the Caster Concepts team. Under his direction, the company has grown and become a valuable material-handling resource to customers globally. With the ability to integrate a lean Six Sigma methodology combined with his intuitive knowledge of solving material handling challenges, Doug ensures Caster Concepts’ quality products meet the specific needs of a wide range of applications and industries.
Doug started at Caster Concepts as a college intern and continued on to become an indispensable and hard-working full-time member of the company's engineering team. He accomplished all this while completing both a bachelor's and a master's degree in engineering and manufacturing.
Doug was instrumental in leading advanced processes as head of the quality department at Caster Concepts. He also led the team to secure ISO 9001 and AS 9100 certifications for Aerol, the company's latest acquisition of precision casters and ground support equipment for the military and other industries. He also co-authored an award-winning article entitled: Predictive Product Failure Models for Polyurethane Trends. Doug’s leadership and insights have been instrumental in the growth of Caster Concepts and its future success.
Comments (0)
This post does not have any comments. Be the first to leave a comment below.
Featured Product
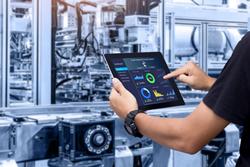