3 Ways Manufacturers Are Using Digital Twins to Improve Operations
Throughout the last few decades, advanced technologies have driven tremendous growth in the manufacturing industry. Technologies like IoT, sensors, and AI have propelled manufacturers forward, and we're finally seeing Industry 4.0 become a reality. Now, digital twins are poised to become the next breakout innovation in the sector -- even if some consider it an offshoot of IoT technology. In truth, digital twins is a robust technology that incorporates all of the multiple technologies listed above, and it's now driving financial growth for big and small manufacturers.
However, it would be unwise to chalk up digital twin technology to that following shiny toy every company needs. The reality is that ROI that can be delivered when utilizing digital twins to their full potential is game-changing for manufacturers looking to innovate in the wake of a global pandemic. Here are three ways digital twins are being used to improve operations and much more for manufacturers.
Replicating Real-World Data
Although a digital twin is exactly what it sounds like, it’s essential to explain why this technology is necessary for tomorrow's manufacturers. A digital twin is the computer simulation of a real-world system or device. A model is created to run as an ‘executable model’, driven by stimulus or various types of tests. The output of the simulation produces data that replicates the corresponding real-world device.
This replication of real-world data on a digital twin is where the importance of sensors comes into play. Although digital twins appear to be mere simulations, they’re, in fact, not. The data end-users receive comes from real-world sensors that display digital twins in real-world conditions, thus ensuring a more accurate picture. Sensors with digital twin object-orientation enable increased IoT-driven optimizations within the manufacturing industry. As a result, manufacturers gain actionable business insights versus a pile of messy data.
If businesses start with a well-thought-out data object, digital twin analytics can transform the maintenance and management team’s working ways. This robust tool allows for comparisons, analytics, what-if scenarios, and meaningful traceability. Compared to simply collecting unorganized raw sensor data, a digital twin framework enables physical assets to come to life meaningfully.
A recent survey from FMI and Autodesk found that although available project data has doubled over only three years, 25% of respondents' project data remains unusable. The survey also found that a third of all poor decisions are due to insufficient data. With that said, manufacturers can’t rely on messy data in 2022 if they hope to make Industry 4.0 a reality. Additionally, they can rest easy knowing that they’re making informed, data-driven decisions to keep their operations running smoothly.
Mitigating Equipment Risks
Although digital twins can help guide manufacturers in the right direction from a business point of view, digital twins can also paint a clear picture of individual assets. IoT-powered devices can detect changes in parameters on equipment such as pumps, valves, fans, cooling towers, motors, and more.
Many values can be analyzed to understand what, when, and why things change. As engineering and maintenance teams find solutions for preventative maintenance and increased optimization, utilizing IoT to observe changes in equipment parameters such as vibration, surface temperature, moisture, pressure, speed, level, and flow can save enterprises time and money.
For example, the digital representation of assets provides the elements and the dynamics of how a pump, valve, or piece of equipment lives through its life cycle. Additionally, the data from the digital twin allows traceability, history, and data analytics of the real-world device, thus making decision-making less obscure and more data-driven. Of course, with more organized data comes more opportunity to improve the surrounding process where the digital twin is implemented, enabling optimizations that were previously unknown.
And with the ability to monitor the behavior of physical assets versus the ideal operating parameters they were designed for, maintenance teams can compare all technical attributes and operational insights from similar pieces of equipment. Therefore, when starting with a well-thought-out data object, the digital twin analytics transforms the maintenance and management team’s ways of work, providing a handy tool for comparisons, analytics, what-if scenarios, and meaningful traceability.
Simplifying Data Visualizations
Compared to traditional industrial control systems, IoT is relatively young, and the digital twin concept is still maturing. However, enough successful examples are operating in the world that these principles cannot be ignored. IoT solutions have leveraged digital twins in various ways; from simple robotic arm images with superimposed sensor data to extremely complicated algorithms and visualizations that require a Ph.D. to comprehend.
And that is the ultimate perk of utilizing a digital twin: simplicity. Rather than individually monitoring individual pieces of critical equipment, the ability to compare all technical attributes and operational insights from similar pieces of equipment operating in different industries trended over time.
An excellent digital twin framework utilizes dashboards that can contain an unlimited number of unique digital viewpoints without the need to rebuild databases or create new frameworks constantly. Although a digital twin can have dynamic sensor data, static asset data, and performance analytical insights, it’s ultimately managed and represented as a single entity, thus ensuring simplicity for end-users.
This simplicity is also imperative for making visualizations easily digestible for end-users. Rather than drowning in data -- the end user can see the data in a way that is easy to understand. So, when flow sensors are installed on a pump for example, the digital twin becomes an excellent tool for monitoring temperature and vibration which is essential to not only avoiding downtime due to a maintenance issue but also ensures safety on the manufacturing floor.
With that said, data is always important for making informed business decisions. However, it takes time to sift through that data–time that many companies in the manufacturing sector can’t afford to waste. Time is money and with digital twins, manufacturers can be rest assured that they’ll be making the most out of their data.
Comments (0)
This post does not have any comments. Be the first to leave a comment below.
Featured Product
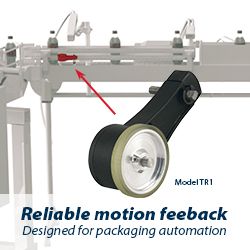