Quest For Manufacturing Human Tissue In Space Via 3D Printer to Be Launched In July
Two high-tech companies have teamed up to develop the first 3D printer capable of manufacturing human tissue (including, someday, organs) in the microgravity condition of space. Techshot Inc., a commercial developer and operator of spaceflight equipment; and nScrypt, a manufacturer of the world's most advanced industrial 3D bioprinters and electronics printers, developed the 3D BioFabrication Facility (BFF). The BFF will use adult human cells (such as stem or pluripotent cells) and adult tissue-derived proteins as its bioink to create viable tissue. A small bio-ink startup, Bioficial Organs, also was consulted on the project. It will launch to the International Space Station in July aboard the SpaceX CRS-18 cargo mission from Florida's Cape Canaveral Air Force Station.
Though the prospect of manufacturing hearts and other organs via a 3D bioprinter is likely a decade away, the July launch is a significant milestone in that quest. The initial phase for BFF, which could last about two years, will involve creating test prints of cardiac-like tissue of increasing thickness. The next phase, where heart patches are manufactured in space and evaluated on the ground (under a microscope and perhaps in small animals such as rats) could last through approximately 2024.
Ultimately, long-term success of BFF could lead to reducing the current shortage of donor organs and eliminate the requirement that someone must first die in order for another person to receive a new heart, other organ or tissue.
Why produce human tissue or organs in space?
Though researchers have had some success with 3D printing bones and cartilage on Earth, the manufacturing of soft human tissue (such as blood vessels and muscle) has been difficult. On Earth, when attempting to print with soft, easily flowing biomaterials, tissues collapse under their own weight – resulting in little more than a puddle. But if these same materials are produced in the microgravity environment of space, the 3D-printed structures will maintain their shapes.
Once printed in space, the structures will be placed in a cell-culturing system that strengthen them over time, to the point where they become viable, self-supporting tissues that will remain solid once back in Earth's gravity.
Techshot President and CEO John Vellinger said the July launch of BFF is the culmination of more than four years of research and planning. "The concept of developing tissue or an organ in space with a 3D bioprinter has been with us for years," he said. "From the technological and biological perspectives, making it real has been a painstaking process of experiments and testing. To see this coming together is an amazing thing for the team, as well as for all of medical science."
For nScrypt CEO Ken Church, Ph.D., BFF's long-term potential is very personal. Twenty-four years ago Church's daughter was born with one lung. She survived and today lives an active and full life despite her missing lung. But Church remembers thinking aloud: "I wish we could just make her another lung."
Today, the prospect of making a lung is not so farfetched. "Assembling a human lung or other organ is still years away, but it is no longer science fiction." Church said. "BFF is the roadmap for getting there. And this BFF team knows how to follow that map. I have no doubt someday BFF will provide someone like my daughter with a second lung."
BFF success can lead to numerous medical breakthroughs
Long-term success of BFF as a human organ manufacturing system presents several potential medical breakthroughs, including:
- Reducing the organ donor shortage (currently 113,000 people are on organ transplant waiting lists).
- Creating patient-specific replacement tissues or patches (by creating tissues/patches from the patients' very own stem and pluripotent cells).
- The possibility of transplant recipients receiving organs comprised of their own stem cells, thus reducing the likelihood of rejection and reducing long-term costs associated with a lifetime of anti-rejection drugs (and, perhaps, additional transplants).
- Eliminating the requirement that someone must first die in order for another person to receive a new heart or other organ.
About Techshot Inc.
Techshot Inc., has been developing new technologies for the aerospace, defense and medical industries since 1988. Its devices have flown aboard parabolic-flight aircraft, sub-orbital rockets, space shuttles, the Northrop Grumman Cygnus, the SpaceX Cargo Dragon and the International Space Station. Its Space Act Agreement with NASA permits the company to commercially operate its equipment aboard the station. Since 2015 the Techshot-designed and built Bone Densitometer has been conducting X-rays of mice in space for biopharma companies such as Novartis and Eli Lilly. Its Multi-use Variable-gravity Platform has been aboard the station since April 2018. Techshot is headquartered in Greenvilleand maintains an office at the Kennedy Space Center in Florida. www.Techshot.space
About nScrypt
nScrypt: Founded in 2002 and headquartered in Orlando, Florida, nScrypt designs and manufactures award-winning, next-generation, high-precision microdispensing and direct digital manufacturing equipment and solutions for industrial applications, with unmatched accuracy and flexibility. Serving the printed electronics, electronics packaging, solar cell metallization, communications, printed antenna, life science, chemical/pharmaceutical, defense, space, and 3D printing industries, its equipment and solutions are widely used by the military, academic and research institutes, government agencies and national labs, and private companies.
nScrypt's BAT, the world's first commercially available bioprinter (developed under a contract with the Defense Advanced Research Projects Agency) – won R&D Magazine's 2003 Top 100 award. www.nScrypt.com
Comments (0)
This post does not have any comments. Be the first to leave a comment below.
Featured Product
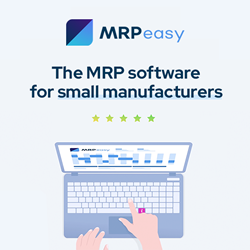