A Q&A Guide to Etching Metals
Chemical etching is a metal machining technology that has numerous advantages over traditional sheet metalworking processes, key among which is its applicability to a range of metals and alloys — even ones that are difficult or even impossible to machine using traditional metal fabrication technologies.
Q. What are the unique characteristics of chemical etching?
A. Chemical etching has the ability to manufacture burr and stress-free precision metal parts with complex geometries, while maintaining the flexibility to make last minute design changes, and mass-produce prototypes quickly. In addition to speed in production, chemical etching is often the most economical option for producing custom parts with complex designs and strict tolerances, as unlike other processes, cost does not increase with design complexity. Finally, the use of inexpensive and easily re-iterated photo-tools allows for low-cost trial and error of design configurations, again often not possible with other methods.
Q. Which metals are suitable for chemical etching?
A. Virtually any metal can be chemically etched, but as with most metal machining processes, some are easier to etch than others. Demand from industry often focuses on metals that have attractive attributes, and it is on these metals that Precision Micro’s efforts are focussed to ensure its processes are developed in line with our customer’s, and our customer’s markets demands.
Q. How do you etch titanium?
A. Titanium is lightweight, strong, has excellent fatigue performance, as well as offering high resistance in aggressive environments. These favourable properties, however, prove to be a problem when machining.
Titanium’s high strength, low thermal conductivity, and chemical reactivity with traditional tool materials (at elevated temperatures) significantly reduces tool life when machining. Its relatively low Young’s modulus leads to spring-back and chatter, causing poor surface quality on the finished product. In addition, during turning and drilling, long continuous chips are produced, which can lead to entanglement with the cutting tool, making automated machining challenging.
The use of chemical etching overcomes many of these issues, but even etching titanium is difficult, as the metal forms a protective oxidised coating when exposed to air, meaning it cannot be etched with standard etch chemistries. To overcome this, Precision Micro developed a propriety process, investing in specialist equipment and process chemistry to produce etched parts comparable to this produced in stainless steel.
Precision Micro is one of the few companies in the world that can photo-etch titanium on a production scale, today supplying a number of biocompatible medical devices to industry leading OEMS such as cranial and dental implants which benefit from complex openings with depth-etched countersink features.
Q. How do you etch aluminium?
A. Aluminium exhibits many of the attributes of titanium — notably its high strength to weight ratio and natural corrosion resistance — but whereas titanium is stronger and more corrosion resistant than aluminium, aluminium has a better fatigue limit, which makes it ideally suited to aerospace applications where fatigue limits must be high.
When conventionally machining aluminium, there are a number of problems, the biggest being what is termed “the built-up edge” — basically the welding of work-piece material to the tool edge, and the subsequent loss of effective geometry which causes increases in cutting forces and quality problems such as scratches in the surface and cloudy finish. For many suppliers, aluminium is also difficult to photo-etch effectively as the heat energy it releases during etching often results in a rough, granular edge.
As with titanium, Precision Micro has developed a proprietary method for etching aluminium and its alloys, producing edge profiles comparable with those etched in a much easier to process metal, namely stainless steel.
As an AS 9100 accredited supplier, Precision Micro etched components for a wide range of aerospace applications, including light-weight helicopter air intake grilles and heat transfer plates used in aircraft dehumidifiers and engines, the latter often requiring multiple designs which can be set-up cost-effectively.
Q. How do you etch steel and stainless steel?
A. While the likes of stainless steel, copper, and nickel are less troublesome to photo-etch, they still require the application of experience and significant investment in processing technologies to optimise customer outcomes.
Due to its versatility, stainless steel is used in a wide variety of applications in numerous industry sectors, and is a preferred metal in many instances due to its corrosion resistance properties and for the different versatile grades that are available.
Precision Micro photo etches a wide range of austenitic (300) and martensitic (400) series steel grades from stock, as well as specialist grades including Sandvik Chromflex strip steels and nickel chrome, all of which amounts to the supply of 2,000,000 steel components each month.
Precision Micro specialises in a number of applications of photo etching on stainless steel, including meshes, filters and sieves (cost does not increase with design complexity) flexure springs for ABS braking systems, medical biosensors, and fuel injection systems (burr and stress-free meaning springs function for longer) and bipolar plates for liquid-to-liquid or liquid-to-gas heat exchanger (complex channels etched into plates which remain perfectly flat).
Q. How do you etch copper and copper alloys?
A. As a relatively soft metal that exhibits high thermal and electrical conductivity, copper etches quickly in standard etch chemistries, unlike contact machining processes which can stretch copper out of shape and alter its properties.
Copper and its alloys are highly durable, ductile, and malleable, meaning it is well suited to forming and plating post-etching, Precision Micro produces thousands of 3-D electrical contacts, pins, terminals, EMI gaskets, shielding, lead frames and connectors each month for automotive, electronics, aerospace, and medical applications.
Q. How do you etch nickel and nickel alloys?
A. Nickels high resistance to heat and corrosion make it a popular choice when developing a variety of parts and components, it being commonly used as a protective outer coating for softer metals. Very few things are made out of pure nickel as it is used primarily as a stabiliser. However, while Precision Micro can apply its photo etching to an array of nickel-coated metals, it is also unusually able to process pure nickel and nickel alloys. One such application saw the company recently apply its experience to the processing of Inconel, a high temperature nickel-based superalloy which as well as superior heat resistance also exhibits excellent resistance to corrosion, pressure, and oxidation.
Q. Why should I choose Precision Micro as my chemical etching supplier?
A. Success in photo-etching any metal is down to the experience and skill of your chosen photo etching partner to ensure success in manufacture. Precision Micro has well over 50 years of experience, and is Europe’s market-leading chemical etching expert. Its continual investment in research and development of chemical etchants and process parameters means that today, even the most challenging metals can be processed in volume and to exacting standards in terms of tolerance and accuracy. All of this is underpinned with robust quality management systems with the company accredited to ISO 9100, ISO 13485, IATF 16949, ISO 14001 and AS 9100.
About Precision Micro.
For over 50 years, Precision Micro has pioneered photochemical etching. The company has won a reputation as the industry innovator, trusted to deliver by major global manufacturing concerns across multiple markets.
Comments (0)
This post does not have any comments. Be the first to leave a comment below.
Featured Product
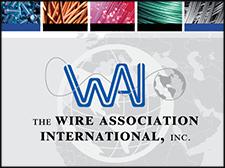