Successful use of professional 3D printing and high-performance composite material in the manufacturing of airbag housing container
As Joyson Safety Systems project and application, it is the first functional prototype to be produced with Laser Sintering process by using CRP Technology’s Carbon reinforced composite material Windform® SP
Joyson Safety Systems (headquartered in Auburn Hills, Michigan, USA) is a global leader in mobility safety providing safety-critical components, systems and technology to automotive and non-automotive markets.
Joyson Safety Systems is worldwide the first manufacturer supplying in series steering wheels with HOD ("Hands-on-Detection") function for autonomous driving to renowned OEM's in North America as well as in Europe.
CHALLENGE
Joyson Safety Systems' Core innovations team started a project to explore and deep dive into the Additive Manufacturing field, also pointing out to its possibilities and potentials to discover new processes and materials to use for the manufacturing of airbag housing container.
They thus carried out a market analysis in order to find out a composite material corresponding to the existing material (in this case, polyamide with 40% glass fiber reinforcement) used in production of the airbag housing container through conventional process (injection moulding).
The Driver Airbag (DAB) housing part is often produced with PA6-GF40 material. The complete system of the airbag is consisting of inflator, an airbag cushion, a cover and a housing with attachment points on the steering wheel. The airbag cushion that is connected to the housing part is located within the space of the housing and the cover.
The performance of the DAB housing part is extremely essential, due to the fact that it's a safety component in the vehicle. This means that the Airbag will inflate during a sudden accident within quite a short period of about 30-50 ms (millisecond) to prevent the passenger from any injuries. The DAB housing is holding the entire Airbag system in place so it is also a base essential component for the system.
Samer Ziadeh and Daniel Alt from Joyson Safety Systems' Core innovations team explain which is the function of the DAB housing, and say that "it is to withstand a high amount of dynamic loads in addition to holding the inflator and the airbag cushion fixed in location during and after the deployment of the airbag system. This load is develop due to the pressure required to inflate the airbag, as a result the large stresses will directly be applied on the airbag system and more particularly on the DAB housing.
The test procedures are normally conducted within a various range of temperatures between -35°C and +85°C."
Thus given, the material used for manufacturing the part is expected to have sufficient strength, impact resistance and heat stability to perform properly under different testing conditions.
SOLUTION
The Joyson Safety Systems' Core innovations team scheduled a very tight programme, aimed to reach specific purposes, that is: produce a real functional prototype part within days instead of months, out of composite materials which are almost similar in mechanical, thermal properties and performance to the original materials; test part performance under real testing environment conditions to examine how the material will perform under thermal changes and to withstand high strain mechanical stresses; eliminate the amount of time-consuming and avoid the highly tooling costs of conventional process.
Joyson Safety Systems' Core innovations team turn to CRP Technology for their Windform® TOP-LINE range of high performance materials and its in-house 3D printing service.
Ziadeh and Alt add, "after running some market analysis in order to find out the most suitable material and process that could deliver the required performance, we came across the Windform® TOP-LINE family of composite material and, specifically, the Windform® SP.
Windform® SP brought our attention to the fact that it's a material produced from polyamide PA grades and reinforced with Carbon fiber as a powder form material, and it has almost the required and even better performance for our application."
"The technical data of the Windform® SP" - Ziadeh and Alt comment - "displayed a very high potentials to be used for producing the DAB housing by SLS process."
Thanks to the collaboration with CRP Technology and to the use of Windform® SP Carbon composite material, it was possible to produce a functional prototype and to test it in a complete airbag module within a short period.
RESULT
The test has led to very good results as the material exhibits an excellent mechanical performance in terms of high strength and impact resistance as well a good thermal stability between a low and high range of temperatures (RT; 23°C, -35°C & 85°C).
"Therefore this opportunity has opened up a variety of capabilities and considerations for a further cooperation with CRP Technology", comments Samer Ziadeh.
Ziadeh and Alt state, "Also the prototype part demonstrated an outstanding performance during various testing conditions, which has proven the fact of part functionality for a complete consideration of a new product development. Basically the pros by using the SLS process is the possibility to use reinforced polymers with high mechanical performance and stability. The combination allow for the manufacturing of complex part structures with good tolerance. Concerning the Windform® SP, it indicates an excellent mechanical properties in terms of high tensile strength, impact resistance and thermal stability at high temperature. This actually fulfill the requirements of the DAB housing part."
The most innovative aspect about Joyson Safety Systems project and application is the fact that this is the first functional prototype of a DAB housing to be produced with SLS process using a composite material, Windform® SP, which exhibits an excellent mechanical performance in terms of high strength and impact resistance as well a good thermal stability -
Joyson Safety Systems' Core innovations team
Featured Product
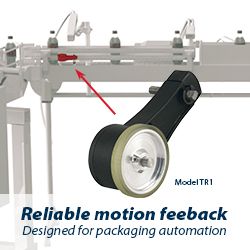
Model TR1 Tru-Trac
The Model TR1 Tru-Trac® linear measurement solution is a versatile option for tracking velocity, position, or distance over a wide variety of surfaces. An integrated encoder, measuring wheel, and spring-loaded torsion arm in one, compact unit, the Model TR1 is easy to install. The spring-loaded torsion arm offers adjustable torsion load, allowing the Model TR1 to be mounted in almost any orientation - even upside-down. The threaded shaft on the pivot axis is field reversible, providing mounting access from either side. With operating speeds up to 3000 feet per minute, a wide variety of configuration options - including multiple wheel material options - and a housing made from a durable, conductive composite material that minimizes static buildup, the Model TR1 Tru-Trac® is the ideal solution for countless applications.