NORD Direct Drive Systems Outperform Belt Drives in Efficiency, Safety, and Cost-Effectiveness
Direct drive solutions offer an innovative alternative to traditional belt drives that deliver greater performance, reliability, and lower Total Cost of Ownership (TCO).
Two common types of drive solutions available on the market are direct drive solutions and belt drive solutions. With direct drives, the gear motor is directly connected to the load being driven and does not require additional connection components. Belt drives, in comparison, are offset from the driven load and require belts and pulleys to connect the two. They also often include a motor mount, sheaves, machine guard, and a torque arm, making them a more complicated set up than the gearbox, NEMA adapter, and motor combination of direct drives. The compact direct drives also provide higher efficiency, reliability, and safety features compared to traditional drive packages.
Gear motors from NORD DRIVESYSTEMS are offered as parallel shaft and right-angle mounted direct drives for versatile installation according to application and space constraints. The gear units are manufactured with robust, one-piece UNICASE™ housings with all bearings and seal seats contained within the housing for additional protection and reliability. Bearing life is extended in this design thanks to the lack of radial loads on the motor shaft and the gearbox input shaft. NORD electric motors combine easily with their modular gear units and provide high-efficiency, high output torques, and an ample output speed range across multiple frame sizes. Variable frequency drives extend these capabilities, providing precise speed control of the drive, reducing the number of system variants, and decreasing the quantities of spare parts backstock.
Direct drive systems offer improved safety over belt drives as interaction with equipment is minimized and the enclosed solution reduces the chance of injury. Belt drive systems require additional protection measures and resources for safeguarding users from their moving parts. Belts also require adjusting or replacing multiple times per year which can be dangerous if not handled properly by skilled personnel. Maintenance for NORD direct drives systems is significantly quicker, easier, and more cost effective than belt drives due to fewer wear parts and modularity. If the motor needs replacing, the old motor can simply be uninstalled, and the new one attached and connected to power. Motor replacement on belt drives, however, requires the whole system be unassembled before the new motor can be attached and the belt adjusted.
Direct drive systems prove themselves to be more efficient than belt drives due to reduced mechanical friction and no belt tension reduction. Since they do not have belts, they also do not require downtime to re-tension the belt, achieving greater system availability. In intralogistics systems that consume a lot of energy such as conveyor operations, energy efficient direct drives with premium efficient IE5+ synchronous motors significantly reduce energy costs and system variants thanks to their constant torque even at partial load and low speed ranges.
Featured Product
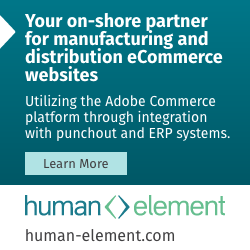