As the implementation of advanced manufacturing methods like AM increases, it is important to investigate and apply production methods that can produce intricate, yet reliable parts quickly and cost-effectively.
Increasing Demand for Medical 3D Printed Parts Requires Effective Finishing Methods
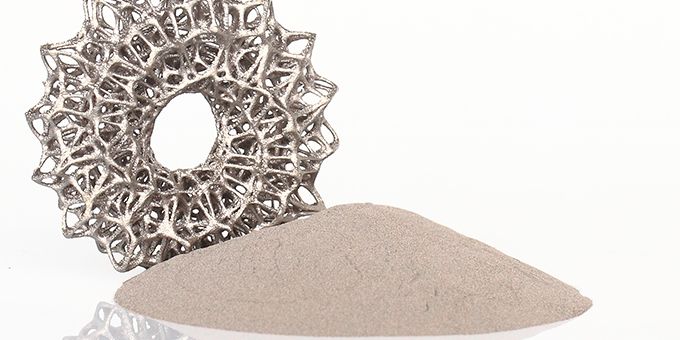
Elizabeth Norwood, Senior Chemist | MicroCare, LLC
Covid-19 has helped to push 3D printing, a form of additive manufacturing (AM), into the spotlight thanks to its capability to quickly and effectively produce medical components.
At the beginning of the pandemic, the world was plunged into a crisis that required manufacturers of medical devices to produce essential products quickly. However, logistical challenges due to transportation and manufacturing disruptions put pressure on the supply chains resulting in shortages of essential items like parts for ventilators, emergency respiration devices and PPE.
Manufacturers of 3D printed parts rose to the emergency and responded swiftly thanks to its agile production environment. Unlike traditional manufacturing methods, parts could be designed and produced at speed even for those that were complex in design.
AM has made such an impact since the start of the pandemic that the global 3D printer market is predicted to grow. In 2019 at the start of the pandemic, the global 3D printing market was estimated at $12.1B on average seeing a 25% year-over-year growth since 2014. For the following five years, analysts expect the market to grow on average at 24% CAGR, reaching $35.0B by 2024 and doubling in size approximately every three years.
As the implementation of advanced manufacturing methods like AM increases, it is important to investigate and apply production methods that can produce intricate, yet reliable parts quickly and cost-effectively. This includes choosing the best finishing methods and fluids for the printing material being used. This will enable the innovation in medical device design and manufacturing and for AM to continue to flourish.
AM- The Process
There are a number of AM methods used to make medical parts. Some, like selective laser melting (SLM) and electron beam melting (EBM), require specialized equipment, complex safety procedures and skilled workers to operate. Binder Jetting (BDJ) is less expensive, faster and easier to use than other methods and is the preferred option for many manufacturers thanks to its simplicity.
BDJ builds a part out of a feedstock made up of fine plastic or metal powders and a binding agent. The powdered metals can include medical-grade stainless steel, titanium and other alloys to produce high-performance precision parts that meet both FDA regulations and a customers’ specific standards.
The 3D printer deposits an ultrafine layer of powder on a build platform. A liquid wax, which can include paraffin wax, carnauba wax, or speciality polyethylene, is then used as a bonding agent to bind the particles together. The print head continues to deposit alternating layers of the powdered material and the binding material in thin horizontally progressive layers until the green parts form the desired shape.
The binding agents aid in maintaining the resulting printed green part before sintering. Once the green part is printed it is debound and then sintered at extreme temperatures. This extracts any remaining binders and bonds the metal powder into its solid coherent mass. Although critical to forming the metal powder into a specific shape, a percentage of the binder must be selectively removed from the internal structure of the part before the green part can be exposed to the high heat required for sintering.
Vapor Degreaser: Vapor degreaser debinding can reduce debinding times by as much as 75% over other debinding methods
Vapor Degreasing-the Finishing Touch
To achieve a quality finish and guarantee the reliability and quality, any parts produced using BDJ should be debound and cleaned thoroughly. The most effective way to do this is through vapor degreasing and the use of speciality debinding fluids. The binders are selectively removed to avoid deformation and cracking during sintering. This also allows the part to maintain its dimensional accuracy, compress uniformly and sinter evenly. The debinding process also typically allows for quicker sintering times resulting in a faster production run.
A vapor degreaser boils a nonflammable debinding fluid into a dense vapor. The boiling fluid and vapors combine to debind, clean and dry the green parts inside. Depending on the green part’s material and the binders used, the binders are removed by either immersing the parts in the low-boiling debinding fluid, by holding them inside the vapor blanket of the vapor degreaser, or a combination of both. The low-boiling debinding fluid effectively melts the wax binders but does not damage the non-soluble fragile parts.
Once the vapors reach the condensing coils within the machine, they are chilled and returned to a liquid state. The liquid is then collected within the system to be used again. This recycling process takes place for hundreds of cycles before the debinding fluid needs to be refreshed or replaced, making it an efficient and sustainable process. Furthermore, the vapor degreaser concentrates the binders and other contaminants, minimizing the amount and frequency of disposal. This reduces environmental waste and the high disposal costs associated with other debinding methods.
Sustainability and Safety Benefits
Using solvent de-binding is not just sustainably beneficial when it comes to recycling, but it also hits all the green targets when it comes to global environmental regulations.
Todays’ vapor degreasing finishing fluids do not have air and groundwater quality concerns that older legacy solvents had. Highly advanced de-binding fluids have been developed to replace more questionable chemicals like HCFC-225 or nPB and TCE and feature a minimal Ozone Deleting Potential (ODP) and a low Global Warming Potential (GWP). They also meet important air quality and worker safety standards like those demanded by the medical industry and international governing bodies including the U.S. Environmental Protection Agency (EPA) and Europe’s Registration, Evaluation, Authorisation and Restriction of Chemicals (REACH).
In addition, modern debinding fluids are hostile to bioburden and do not support the growth of bacteria or mold. This makes them easier to introduce and validate into medical manufacturing processes.
Producing Quality Parts
Debinding fluids work quickly and efficiently to optimize production timelines. For example, fast-evaporating debinding fluids dry fast, allowing the green parts to move to the sintering phase sooner. Choosing vapor degreaser debinding can reduce debinding times by as much as 75% over other debinding methods, to improve throughput and reduce overall manufacturing cost.
When it comes to manufacturing medical parts, Covid-19 proved that time can be of the essence. But it should not come at the detriment to quality. Parts must not only be produced quickly and to a high standard, but they must also adhere to all standards and regulations. With 3D printing on the rise within the healthcare sector, it is important that the right tools, including effective debinding fluids, are used.
They should not only be efficient and consistent, but they must also meet environmental and safety standards. Vapor degreasing, when used with environmentally-progressive debinding fluids, are playing an important role in meeting future AM manufacturing requirements of the medical industry.
About Elizabeth Norwood
Elizabeth Norwood is a Senior Chemist at MicroCare, LLC, which offers precision cleaning solutions. She has been in the industry more than 25 years and holds a BS in Chemistry from the University of St. Joseph. Norwood researches, develops and tests cleaning-related products. She currently has one patent issued and two pending for her work. For more information, visit www.microcare.com.
The content & opinions in this article are the author’s and do not necessarily represent the views of ManufacturingTomorrow
Comments (0)
This post does not have any comments. Be the first to leave a comment below.
Featured Product
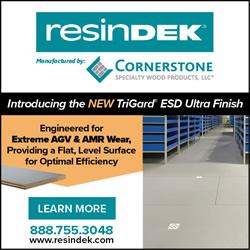