VTT delivers world's first industrial internet solution for a printed electronics plant
PostProcess Technologies Unveils Hybrid Series 3D Post-Printing System
Proto Labs Selected by HP Inc. to Test New, Industrial-Grade 3D Printing Technology
Puris Introduces "Puris 5+™"
RAPID - Type A Machines Introduces Absolute 3D Internal Structures, A New Paradigm for Defining Functional Internal Geometry of 3D Printed Objects
German manufacturers take aim at smart factories, mass customization
Schunk - SWS Quick-Change System: Modular, Robust, and Flexible
DuPont Announces 2016 Packaging Innovation Award Winners
Benda Manufacturing, Inc. Celebrates 30 Years
ToolHubs.com Launches a Network for 3D Printers and CNC Machines
East Coast's Largest Advanced Manufacturing Event Spotlights Innovation in Packaging Creation - from Health & Beauty to Food & Beverage
These Five Exponential Trends Are Accelerating Robotics
Dorner Announces Acquisition of Geppert-Band
Nordson EFD's PICO® Pµlse™ Jet Dispensing System Wins EM Asia Innovation Award and SMT China VISION Award
University of Warwick Uses Stratasys Fortus 3D Printer to Build "Most 3D Printed Vessel on the Grid" for Upcoming European International Submarine Race
Records 5056 to 5070 of 5415
First | Previous | Next | Last
Supply Chain - Featured Product
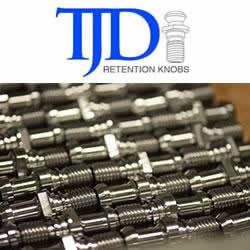