Challenges in Aerospace Innovation in 2019 and Solutions for 2020
Manufacturing for the aerospace industry faced roadblocks in 2019, which slowed the speed of innovation. This article looks at the three biggest challenges engineers in the aerospace industry faced in 2019 and anticipated solutions in 2020.
Streamlining and Integrating Manufacturing Execution Systems and Operations Management (MES/MOM)
The aerospace industry is undergoing a renaissance of innovation with manufacturers pushing for sleeker, more efficient, greener designs across the board.
Professional 3D Printing and Windform® composite materials used in the manufacturing of two innovative aero-elastic wind tunnel demonstrators
Professional 3D printing has revolutionized the entire process of construction and verification of the parts allowing the following: faster production speed and possibility of optimizing the internal shape of these aerodynamic sections.
Quest For Manufacturing Human Tissue In Space Via 3D Printer to Be Launched In July
Though the prospect of manufacturing hearts and other organs via a 3D bioprinter is likely a decade away, the July launch is a significant milestone in that quest.
Top Three Teams Share $100,000 Prize in Complete Virtual Construction Level of 3D-Printed Habitat Challenge
Team SEArch+/Apis Cor won first place in the Phase 3: Level 4 software modeling stage of NASA's 3D-Printed Habitat Challenge. The unique shape of their habitat allows for continuous reinforcement of the structure. Light enters through trough-shaped ports on the sides and to
NASA to Advance Unique 3D Printed Sensor Technology
The 3D printing system is like printers used to produce money or newspapers. However, instead of ink, the printer applies nanomaterials, layer-by-layer, onto a substrate to create tiny sensors.
Flexible Shafts in Aerospace Applications
An argument can be made for the flexible shaft being one of the backbones of the aerospace industry, and it isnt difficult to see why. From windshield wipers to TRAS systems to jet afterburners, flexible shafts are there ...
3D Printing the Friendly Skies: Additive Manufacturing & the Future of the Aerospace Supply Chain
The benefits of additive manufacturing are hard to ignore. So, why hasnt it achieved wider adoption? There are a few important hurdles that AM needs to clear for the aerospace industry at large to get on board.
GKN Aerospace Cuts Assembly Tool Production Time with Stratasys Additive Manufacturing
Time cut from several weeks to a few hours using Stratasys Production 3D Printer. GKN Aerospace is producing complex tools that were uneconomical or impossible to make without additive manufacturing
Top Five Teams Win a Share of $100,000 in Virtual Modeling Stage of NASA's 3D-Printed Habitat Competition
Winning teams successfully created digital representations of the physical and functional characteristics of a house on Mars using specialized software tools.
Renishaw Reduces Machining Time for Aerospace Impeller Manufacturer
If the workpiece datum of a finished part is off-centre, the impeller must be submitted for design analysis, in which a designer reviews the component and decides whether it can be used. Each analysis costs approximately $66,900 per part
Cling's Aerospace Eliminates the "Weakest Link" in Aerospace Machining
Manufacturers are increasing productivity 10-40% and reducing tooling costs by addressing an often overlooked flaw in toolholder-retention knob design.
GE Additive creating world's largest laser-powder additive machine
"The machine will 3D print aviation parts that are one meter in diameter, suitable for making jet engine structural components and parts for single-aisle aircraft"
NASA Awards $100,000 in 3D-Printing Habitat Competition
Ian O'Neill, Space.com: The first printing segment of NASA's 3D-Printed Habitat Challenge is now complete, and the U.S. space agency has awarded $100,000 to the two winning teams.
Norsk setting up industrial scale additive manufacturing plant in New York
Aerospace Manufacturing & Design: Norsk Titanium U.S. is building the world’s first industrial-scale metal additive manufacturing plant by 2017 in Plattsburgh, New York. Officials at the aerospace structural company say the state of New York and the State University of New York (SUNY) Polytechnic Institutehave place an order for 20 Norsk MERKE IV Rapid Plasma Deposition (RPD) machines.
“We are proud to be a part of the unwavering vision and leadership of Governor Cuomo and are moving forward in support of his efforts to revitalize upstate New York with jobs, technology and community pride,” says Norsk Titanium Chairman of the Board John Andersen Jr. “Our researchers have spent ten years pioneering the Rapid Plasma Deposition process that is now ready to cut millions of dollars in cost from the world’s premier commercial and military aircraft, and with the foresight displayed in other sectors, the State of New York is the ideal place to launch this manufacturing revolution.”
Norsk Titanium President and CEO Warren M. Boley Jr. adds, “Today marks the beginning of a new erain the way aircraft, marine vessels, automobiles, spacecraft, and many industrial products are designed and built. Not only are we creating jobs, huge economic impact and great visibility for the wider Plattsburgh community, we are also making history by kicking off a new phase of on-demand, near-net-shape manufacturing that sets a new benchmark of efficiency and customer responsiveness.” Cont'd...
Records 16 to 30 of 30
Featured Product
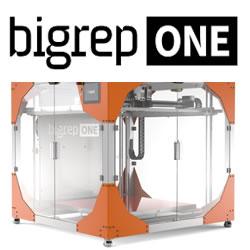
BigRep ONE: Large-Scale 3D Printing
The BigRep ONE is an award-winning, large-format 3D printer at an accessible price point. With over 350 systems installed worldwide, it's a trusted solution for prototyping and production by designers, innovators, and manufacturers alike. Featuring a massive one-cubic-meter build volume, the fast and reliable ONE brings your designs to life in full scale.