The Evolution of Mass Custom Manufacturing: Why the Industry Needs a High-Velocity Shift
For decades, custom manufacturing has been defined by compromise. Traditional job shops, the backbone of the industry, have offered bespoke solutions but at the cost of unpredictable lead times and inconsistent quality. Online vendors have sought to improve accessibility, but many rely on vast networks of third-party manufacturers, leading to variability in both service and output. Meanwhile, off-the-shelf options force customers into a rigid framework, requiring manual labor to achieve customization—often at the expense of professional-grade results.
The industry’s limitations have long been accepted as the status quo, but as demands for speed, precision, and reliability increase, these inefficiencies have become glaring roadblocks to innovation. Enter High Velocity Mass Customization (HVMC), a novel approach that challenges the fundamental trade-offs that have defined the sector for centuries.
The Limitations of Traditional Approaches
Job shops, which have been around for generations, offer expertise and hands-on craftsmanship. They are invaluable when access is reliable, but they operate on a backlog-based system, meaning lead times fluctuate depending on demand. Customers seeking customized manufacturing solutions are often at the mercy of these bottlenecks. Moreover, job shops frequently lack digital infrastructure, making processes like design iteration and automated quoting cumbersome.
Online vendors, which leverage vast manufacturing networks, address some of these issues by providing fast lead times and convenience. However, the distributed nature of their supply chains introduces a different set of challenges, including inconsistent quality, limited customer support, and the potential for miscommunication between designers and manufacturers.
Off-the-shelf products offer the lowest cost but are inherently inflexible. When customization is needed, customers must either settle for a subpar result or engage in a piecemeal process, working with multiple vendors to achieve their desired outcome. This fragmented approach not only extends production timelines but also increases the likelihood of quality mismatches between different components.
The Emergence of High Velocity Mass Customization
HVMC represents a paradigm shift by blending the efficiency of mass production with the flexibility of custom manufacturing. At its core, HVMC relies on breaking down the entire manufacturing workflow—design, production, and assembly—into standardized, repeatable elements. This approach enables scalability while maintaining customization, a feat that traditional methods have struggled to achieve.
Unlike job shops, which face unpredictable bottlenecks, HVMC employs automation and in-house software to create a seamless manufacturing sequence. Each process step is modular, allowing for efficient assembly without the traditional lags associated with custom production. The result is a system where parts move through the facility with a velocity previously thought to be exclusive to mass production.
The ability to integrate automation with customization addresses a critical need for engineers, designers, and manufacturers: the freedom to innovate without being constrained by lead times or quality concerns. HVMC challenges the long-held belief that speed and quality are mutually exclusive in custom manufacturing.
A Turning Point for the Industry
As industries ranging from aerospace to medical devices continue to push the boundaries of design and production, manufacturing must evolve to keep pace. The old models—job shops, fragmented online networks, and off-the-shelf workarounds—are increasingly out of step with the speed of modern innovation.
The promise of HVMC is not just faster production but a fundamental reimagining of how custom manufacturing operates. By standardizing and automating processes without sacrificing the ability to tailor products to specific needs, HVMC has the potential to transform the landscape.
The question is no longer whether the industry needs a change, but how quickly manufacturers will adapt to this new frontier.
With over 35 years immersed in the realms of technology and innovation, Steve Lilley has steered the creation and expansion of numerous tech-driven enterprises. Presently, he serves as the President of Protocase Incorporated, a pioneering manufacturing venture he co-founded in 2001, and as the director of 45 Drives Limited, another technology-focused business established in 2012. In 2023, Protocase launched ProtoSpace Manufacturing, a division dedicated to serving engineering and innovation in aerospace and defense.
About Protocase
Protocase is a leading provider of custom electronic enclosures, panels, and brackets, serving a wide range of industries from aerospace to biotech. The company’s mission is to empower engineers and innovators at all levels to bring their ideas to life quickly and efficiently through its “high velocity mass custom” manufacturing process.
Comments (0)
This post does not have any comments. Be the first to leave a comment below.
Featured Product
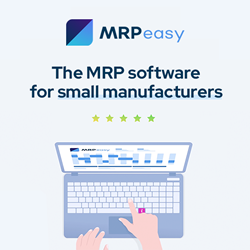