Driving Quality Control Excellence with MOM Integration
With MOM integration, compliance with regulatory standards becomes more manageable. Automated data collection and reporting streamline the process of preparing for audits and maintaining certification requirements.
Louis Columbus, Senior Industry Marketing Manager at DELMIA takes a closer look at quality control in manufacturing.
Best uses for manufacturing technology
In the ever-evolving manufacturing landscape, achieving and maintaining high standards of quality control is paramount for competitiveness and customer satisfaction. Integrating Manufacturing Operations Management (MOM) systems can significantly enhance quality control processes, providing a holistic approach to managing and optimizing manufacturing operations.
Let’s take a look at the benefits and best practices of integrating MOM with Quality Management Systems (QMS) to drive quality control excellence.
Understanding MOM and its role in Quality Control
Manufacturing Operations Management (MOM) encompasses a comprehensive suite of systems and tools designed to manage and optimize manufacturing operations. It includes capabilities for quality management, production monitoring, maintenance, logistics, and more. When integrated effectively, MOM can transform quality control from a reactive process to a proactive strategy.
Differentiating MOM from MES
Manufacturing Execution Systems (MES) are often confused with MOM, but it’s crucial to understand their differences. MES focuses primarily on the execution of manufacturing activities on the shop floor, providing real-time data on production processes. In contrast, MOM is broader, incorporating MES while also integrating quality management, logistics, and maintenance operations into a unified system.
The Importance of Quality Management Systems (QMS)
A Quality Management System (QMS) is a formalized framework that documents processes, procedures, and responsibilities to achieve quality objectives. According to the American Society for Quality, a QMS aims to meet customer and regulatory requirements while continuously improving efficiency and effectiveness.
Benefits of QMS
Implementing a QMS offers numerous benefits, including:
Consistent product quality: Ensures that products consistently meet quality standards. According to McKinsey, companies with robust QMS frameworks see a 20% reduction in product defects and a 15% increase in production efficiency.
Regulatory compliance: Helps maintain compliance with industry standards such as ISO 9001 and ISO 13485. Gartner reports that manufacturers with integrated QMS and compliance systems reduce audit preparation time by up to 40%.
Operational efficiency: Reduces waste and operational errors, lowering costs. IDC’s research indicates that companies using QMS systems can achieve up to a 25% reduction in operational costs.
Customer satisfaction: Improves customer trust and loyalty by consistently delivering high-quality products. According to a study by Gartner, companies with strong quality management practices have 10-15% higher customer satisfaction ratings compared to those without.
Enhanced decision-making: Real-time data from QMS allows for better decision-making processes, providing insights into quality issues and corrective actions.
Improved supplier quality: QMS enables better monitoring and evaluation of supplier performance, ensuring that raw materials meet quality standards, which reduces defects and rework costs.
Examples of integrating MOM with QMS
Integrating MOM with QMS creates a robust system that enhances quality control through real-time data collection, process monitoring, and comprehensive analytics.
Real-time data integration
MOM systems provide real-time visibility into production and quality data, enabling manufacturers to identify and address quality issues promptly. Real-time monitoring of production processes helps in detecting deviations from quality standards and implementing corrective actions immediately. According to McKinsey, companies that leverage real-time data integration see a 30% improvement in production efficiency.
Streamlined enforce quality processes
Integrating QMS with MOM ensures that quality management is embedded throughout every phase of production. This integration automates quality checks, reducing reliance on manual inspections and minimizing human error. It also streamlines the communication of quality-related issues between quality and production teams, enabling swift resolution. Additionally, the system provides full traceability, ensuring compliance with industry standards. Tracking compliance at the level of work instruction processes and step completion further strengthens adherence to quality protocols, ensuring consistent product standards and regulatory alignment.
Enhanced compliance and reporting
With MOM integration, compliance with regulatory standards becomes more manageable. Automated data collection and reporting streamline the process of preparing for audits and maintaining certification requirements. This integration ensures that all quality-related data is accurate, up-to-date, and easily accessible, which is critical for passing audits and maintaining compliance. Gartner highlights that automated compliance reporting can reduce the risk of non-compliance penalties by 50%.
Best practices for MOM and QMS integration
To maximize the benefits of integrating MOM with QMS, manufacturers should adopt the following best practices:
- Centralized data management: Ensure that all quality data is centralized and accessible to all relevant stakeholders. This approach facilitates better decision-making and quicker response times to quality issues.
- Continuous improvement: Use real-time data to continuously monitor and improve quality processes. Implement a cycle of regular reviews and updates to the QMS based on the insights gained from MOM systems.
- Cross-functional collaboration: Foster teamwork between quality, production, maintenance, and material handling teams. Integrated systems give everyone a shared platform to boost efficiency and quality. Material handling is key—they ensure materials are where they need to be, keeping production smooth and minimizing delays. By working closely with other teams, they help avoid bottlenecks, streamline inventory, and keep operations running efficiently.
- Training and development: Invest in training for employees to ensure they are proficient in using MOM and QMS tools. Well-trained employees are more likely to utilize these systems effectively, driving better quality outcomes.
- Scalability and flexibility: Choose MOM solutions that are scalable and flexible, allowing them to grow with your business and adapt to changing quality requirements. This ensures that the system remains relevant and effective over time.
- Standardized processes and procedures: Develop and implement standardized processes and procedures across all manufacturing sites. This ensures consistency in quality and helps in identifying best practices that can be replicated across the organization.
- Advanced analytics and Business Intelligence tools: Leverage advanced analytics and Business Intelligence (BI) tools to gain deeper insights into quality metrics and performance. According to IDC, manufacturers using BI tools report a 15% increase in operational efficiency and a 10% reduction in production costs.
- Integration with ERP systems: Integrating MOM and QMS with ERP systems gives a complete view of the manufacturing process, from procurement to delivery, for better resource management. It also tracks the total cost of quality—both good and bad. Good quality costs include investments in training, inspections, and process improvements that prevent defects. Bad quality costs come from rework, scrap, downtime, and warranty claims, all of which hurt profitability. Integrated systems help manage these costs, improve quality, and streamline operations.
- Real-Time monitoring and alerts: Implement real-time monitoring systems with alert capabilities to detect and respond to quality issues as they occur. This proactive approach helps minimize production disruptions and maintain high-quality standards.
- Supplier quality management: Extend the integration to include Supplier Quality Management (SQM) systems. This allows for better monitoring of supplier performance and ensures that raw materials meet the required quality standards before they enter the production process.
Final thoughts
Integrating MOM with QMS is a powerful strategy for driving quality control excellence in manufacturing. By leveraging real-time data, automating quality processes, and ensuring continuous improvement, manufacturers can achieve higher standards of product quality, compliance, and operational efficiency. Embracing this integrated approach not only enhances quality control but also provides a competitive edge in the market.
Manufacturers aiming to maintain and enhance their reputation for quality should consider the integration of MOM and QMS as a critical component of their operational strategy. By doing so, they can ensure that quality management becomes a proactive, integral part of their manufacturing processes, leading to sustained success and customer satisfaction.
Comments (0)
This post does not have any comments. Be the first to leave a comment below.
Featured Product
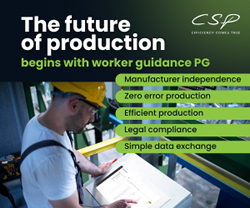