3D Printing and Sustainable Auto Manufacturing: A Glimpse into the Future
The auto manufacturing industry doesn’t have a reputation for being environmentally friendly. Still, many manufacturers have embraced sustainability initiatives to comply with increasing regulations or meet the demands of an eco-conscious market. As this trend continues, 3D printing could become a game-changing tool in the sector.
Also called “additive manufacturing,” 3D printing is most popular as a consumer hobby, but the technology has extensive applications in the industrial world. Capitalizing on these use cases could provide the catalyst some carmakers need to become more sustainable.
The Need for Sustainable Auto Manufacturing
The excitement around 3D printing in the automotive industry is easier to understand in light of growing sustainability needs. While vehicles themselves may be the most obvious target for emissions reductions in this sector, the production side needs improvement, too. Manufacturing a single vehicle produces 10 metric tons of CO2 equivalent, even for electric and hybrid cars.
That figure must go down if the industry hopes to meet the ever-rising number of government emissions regulations. While many current laws focus on direct vehicle emissions, more general targets may necessitate production-stage improvements.
As the world transitions to electric vehicles (EVs), these emissions will stand out more. Consequently, automakers that do not reduce their manufacturing carbon footprints could fall out of public favor. They may face regulatory penalties as environmental laws grow. Even if that does not happen, they risk losing business as consumers become more climate-aware.
How 3D Printing Supports Green Manufacturing Goals
Making auto manufacturing truly sustainable is a complex endeavor. 3D printing cannot solve all the sector’s environmental woes, but it can play a central role in the green production process. These improvements stem from several areas.
1. Energy Efficiency
The most direct impact of 3D printing on automaking sustainability is its efficiency. Additive manufacturing can produce components faster than conventional machining in many cases. These printers also use less energy as they work — largely because they encounter no friction or other resistance — resulting in lower process-related emissions.
NASA reduced rocket component lead times by two to 10 times by switching to additive manufacturing. Applying the same concept to vehicle production could yield tremendous time savings, resulting in less power spent per part.
Most electricity comes from fossil fuels today. Consequently, by reducing total tool time, manufacturers burn less fossil fuels per component. As more grids adopt renewables, these time savings will let automakers produce more parts with less power, reducing the strain on more intermittent sources.
2. Waste Reduction
The other main environmental advantage of 3D printing is it produces less waste. Conventional machining is subtractive — it must remove material to make any shape, so even the most efficient processes result in unused resources. By contrast, 3D printing is additive.
3D printers deposit material instead of cutting it away, resulting in higher resource efficiency. Even when these machines must produce supports that manufacturers later remove, these structures use less material than conventional machining would remove. This waste reduction reduces disposal-related emissions as well as those from upstream supply chains.
Leading car manufacturers produce 74 million tons of CO2 annually through their reliance on steel alone. Reducing waste through 3D printing would lower their virgin steel requirements, helping get that figure closer to zero.
3. Rapid Prototyping
Additive manufacturing can indirectly impact carmakers’ carbon footprints, too. Rapid prototyping, for example, can shorten vehicle development timelines and reduce related emissions.
Because 3D printers work faster than conventional methods, they let automakers create physical prototypes without investing as much time or electricity. Those benefits ripple throughout the design process, as testing, redesigning and re-testing will likewise use less time and produce fewer emissions. As a result, engineers can develop high-performing vehicles with a smaller carbon footprint, even with extensive testing.
This prototyping speed also justifies more testing and redesigns than a traditional process. That freedom leaves more room to optimize vehicle designs to produce a more efficient car. As rising environmental regulations spur EV and hybrid demand, this advantage will become increasingly valuable.
4. Greener Vehicles
Relatedly, 3D printing can make cars themselves more sustainable. Part of this eco-friendliness stems from the increased testing during the design phase. However, rapid prototyping and testing is not the end of additive manufacturing’s impact on vehicle efficiency.
3D printers can create complex geometries that are impossible or impractical to achieve with traditional manufacturing. Automakers can use this to develop stronger structures requiring less mass or lighter materials. The vehicles using these parts can be much lighter as a result, improving their fuel efficiency.
Additive manufacturing also opens the door to novel materials manufacturers may be unable to use otherwise. These filaments can reduce vehicle weight or limit reliance on resources like steel, which carry hefty carbon footprints. Renault embraced this strategy to make its car seats 30% lighter while improving material recyclability.
3D Printing in Auto Manufacturing Today
The advantages of 3D printing for sustainable auto manufacturing are more than just theoretical. Several carmakers are already experimenting with the concept.
Ford has invested in several 3D printing solutions, including large-scale metal printing and 3D-printed electronic circuitry. Bringing this process to more areas of car manufacturing will lower each vehicle’s production emissions while maximizing the efficiency benefits of 3D printing.
BMW has embraced 3D printing as a way to expand personalization. Customers can design their own panels and accessories, which it then prints and installs. While these adjustments are chiefly cosmetic, similar solutions could help custom vehicles become more sustainable to meet eco-conscious buyers’ needs.
Automakers’ investments in 3D printing are growing in scale, too. Volkswagen hopes to print 100,000 parts annually by 2025 after installing a new industrial-scale additive manufacturing process. These components are lighter and less energy-intensive than their steel predecessors, resulting in significant sustainability improvements.
The Future of Automotive 3D Printing
As more vehicle manufacturers embrace additive manufacturing, the increased funding will spur technological advancement. It will become possible to print larger components, not just small parts and circuitry. Some manufacturers may even be able to 3D-print entire vehicles in the future.
Novel filaments will also emerge as this technology advances. These new materials could provide increased strength-to-weight ratios, improve recyclability or reduce material sourcing-related emissions. Improvements like these would yield substantial carbon footprint reductions across the automotive supply chain.
Sustainable Auto Manufacturing Needs 3D Printing
3D printing’s full range of possibilities and the timeline in which these innovations will occur is still uncertain. This technology is still new, especially in an industrial context. However, it already shows impressive potential for sustainable vehicle manufacturing.
As pressures rise for the transportation industry to become more eco-friendly, 3D printing will become an increasingly popular solution. While it is not the only step toward sustainable vehicles, it is a crucial one. Automakers must jump on this opportunity today to ensure a greener tomorrow.
Comments (0)
This post does not have any comments. Be the first to leave a comment below.
Featured Product
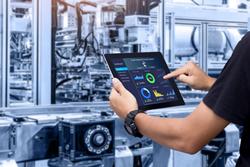