Foundations for Success In Industrial Automation: A Guide for Small to Medium Manufacturers, Part III
In previous articles, we’ve discussed the essential steps small and mid-sized manufacturers must take to create a successful automation project. In the first article, we emphasized the importance of laying the groundwork for an automation project by setting clear objectives, identifying key stakeholders, building specialized teams, and securing top-down support. In the second article, we explored strategies for selecting the right areas of operation to automate first by identifying low-risk/quick wins, choosing a productized application, and performing a factory walkthrough.
For example, I was meeting with a small business manufacturer that was looking to remove repetitive tasks from their factory floor. They needed to improve production by introducing more efficient processes, enabling employees to reallocate their time toward more fulfilling projects. Automation was the solution. By understanding the operation and visiting the factory floor, the team identified machine tending as an automated task that would generate a strong return on investment (ROI), improve efficiency and allow employees to work on more rewarding tasks.
Once you’ve pinpointed what you will automate, it’s time to develop a project roadmap. Here is how to best transform your preparatory efforts into an actionable plan:
Define your objective
Reflect on your automation objectives – Are they clear and concise and answer all the following questions?
- Why do you want to introduce automation?
- What problem are you trying to solve?
- What outcomes are you looking to achieve?
If so, you’re on the right track.
Introducing automation to the factory floor ensures your business can face ongoing industry challenges like labor shortages, client churn, and sudden changes. Automation no longer means high-risk or disruptive implementation; today, it’s accessible to even the smallest manufacturing company, providing returns on cost, quality, and production capacity as well as customer satisfaction.
The roadmap must begin with your objective, as each decision made during the automation project from start to finish must align with it. By clearly presenting the goal for your automation project, you ensure organizational alignment and focus in pursuit of that objective.
Build a business case
Now that you have presented the objective, it’s time to develop a business case. A business case justifies developing this project and can be separated into two main components – capital expenditures (CapEx) and ROI.
Break down each step of the process into estimated costs. With Manufacturing Automation Platforms, when you design your machine, you have access to the real-time pricing of the various components required.
After understanding estimated costs, a detailed ROI analysis must be developed. You can determine your ROI and forecast it for the first five years, including time to break even on equipment costs:
- Manual process assumptions:
- X shifts per day, X days per week
- Labor rate per hour
- Manual cycle-time
- Overall human effectiveness (OHE)
- Automated process assumptions:
- Total monetary investment
- Automated cycle-time
- Overall equipment effectiveness (OEE)
- Other factors:
- Increase production predictability due to labor shortage elimination
- Reduction in labor re-hiring and training cost
- Decrease in pallet formation error (i.e., label placement)
- Elimination of work-related injuries due to repetitive task
- Ability to take on new customer demands
- Flexibility to rapidly adjust to changing production needs
For example, a leading innovator of residential storage products found an automated solution that would cost an average of $350,000, but this solution would ensure $150,000 of cost savings per year. In addition to reaching a ROI in less than 20 months, employees could be reallocated to higher-value tasks enabling production output to increase, resulting in a strong business case.
Introducing automation can be daunting at the project’s start. There are many factors to consider, risks to mitigate, and impacts to navigate. Set yourself and your team up for success by following the steps outlined in this series on kickstarting your automation journey.
The more you plan, prepare, and document, the better the result.
Comments (0)
This post does not have any comments. Be the first to leave a comment below.
Featured Product
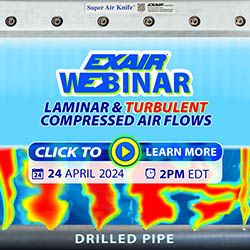