With operations running 24/7, 365 days a year, the company sought to upgrade its variable frequency drives (VFDs) to increase motor efficiency, thus reducing operational costs and enhancing energy efficiency throughout its extrusion processes.
Liquid-cooling VFD Increases Efficiency and Savings in Plastics Machinery
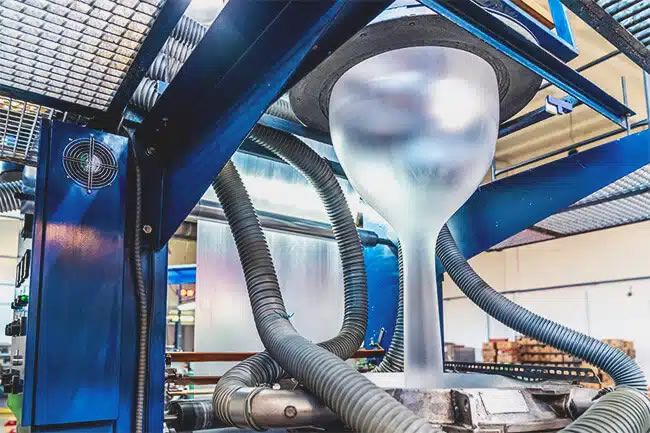
Case Study from | KEB
KEB’s F6 VFD Helps Blown Film Extrusion Machines User Save Nearly $30,000 on Annual Electricity Expenses
A high-quality plastic bag manufacturer (that chose to remain anonymous) operates in a competitive market where efficiency and cost savings are paramount. The company uses 100+ blown film extrusion machines across its North American facilities to produce various durable bag products.
With operations running 24/7, 365 days a year, the company sought to upgrade its variable frequency drives (VFDs) to increase motor efficiency, thus reducing operational costs and enhancing energy efficiency throughout its extrusion processes.
In this pursuit, they partnered with KEB America, leveraging the advantages of its liquid-cooled F6 VFD and reaping substantial benefits.
Reducing Motor Energy Usage
The US-based plastic bag manufacturer faced significant energy consumption costs associated with its 300-horsepower motor-driven plastics extruder equipment.
The company utilized air-cooled variable frequency drives from another manufacturer, which proved to be maintenance-intensive and less efficient, particularly in their demanding operating environment.
Adding to the challenge was sourcing these specific VFDs, compounded by long lead times. As a result, reevaluating its supplier and investing in energy-efficient extruders became paramount.
The client began a search for alternative suppliers that could provide reliable VFDs to control water temperature on its blown film plastic extrusion equipment.
VFD Requirements
The primary considerations were cost, availability, and service. The client needed a North American supplier that offered efficient liquid-cooled VFDs with reliable temperature control capabilities.
Service was also crucial, as downtime could result in significant production and financial losses. Having previously experienced service from KEB, the client reached out to find a solution that could replicate the same level of reliability and support.
Optimizing Liquid-Cooling VFDs
After evaluating several options, the client opted for KEB’s F6 VFD, known for its high efficiency and advanced temperature control features.
The F6 (housing 9) liquid-cooling drive offers a significant advantage over air-cooled alternatives, particularly in the client’s challenging operating conditions. It features stainless steel piping, cooling liquid management, safety functions certified to SIL 3.
KEB engineers worked with the company’s technicians to optimize the drive setup and incorporate the correct protection functions. This was facilitated using KEB’s Combivis 6 software and its integrated start-up wizards.
With the ability to control water temperature independently, the liquid-cooled F6 drive provides optimal efficiency and performance, resulting in substantial energy savings.
Side-by-side comparison of various air cooling and liquid cooled VFDs
Water-cooled versus Air-cooled VFDs
Why did the client move from air-cooled VFDs to water-cooled units? For one, air-cooled VFDs require more maintenance, as they are prone to accumulating dirt and debris in their fans, requiring annual cleaning.
Alternatively, one might opt for an air-conditioned cabinet or a heat exchanger powered by chilled water. However, even in this case, water-cooled systems still have better efficiency than air-cooled solutions.
Increasing the carrier frequency on air-cooled drives can lead to overheating issues. In contrast, water-cooled alternatives allow for operation at higher frequencies, such as 4kHz, resulting in cooler and more efficient motor performance.
For this customer, a 300hp motor operating at 4kHz instead of 2kHz in a water-cooled setup saves $20,000 to $30,000 annually in electricity costs due to reduced heat generation and current load. Given their continuous operation, this type of cooling system is crucial for long-term cost savings and operational efficiency.
Top Benefits of Liquid-cooled Drives in Extrusion Machines
By implementing KEB’s F6 servo drives, the client achieves notable results in:
Energy Savings: The increased motor efficiency from KEB’s liquid-cooled drives led to annual savings of $20,000-$30,000 on electricity bills compared to its previous solution.
Performance: Operating at higher carrier frequencies of 4kHz, the motors ran cooler and more efficiently, enhancing overall performance and reliability. This solution contributed to a high-quality output and minimized production variability.
Reduced Maintenance: Unlike air-cooled VFDs, which required regular cleaning and maintenance, KEB’s liquid-cooled servo drives proved to be low maintenance, contributing to further cost savings and operational efficiency.
Reliable Support: The client’s experience working with KEB was positive. They received prompt and knowledgeable phone and web-based support, ensuring smooth operation and minimal downtime.
KEB Motor and Drive Solutions for Plastics Machinery
By partnering with KEB America and implementing liquid-cooled servo drives, the company significantly reduced operational costs, and improved performance and efficiency in its extrusion and blown film machinery.
Currently seeing annual savings of nearly $30,000 on electricity, the company plans to ramp up an additional 100 lines of blown film extrusion machines with KEB’s liquid-cooled F6 drives.
For those interested in learning more about KEB’s VFDs and large power servo motor solutions for plastics machines, contact a KEB engineer today.
The content & opinions in this article are the author’s and do not necessarily represent the views of ManufacturingTomorrow
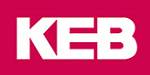
KEB America, Inc.
KEB America is a trusted manufacturer of industrial automation products in North America. We manufacture, assemble, and support our German-engineered suite of controls, drives, motors, brakes, and clutches at an ISO 9001:2015 certified, 150,000-square-foot facility in Shakopee, Minnesota.
Other Articles
Master-Follower Configuration: Precision Control with Encoder-Based VFD Synchronization
More about KEB America, Inc.
Comments (0)
This post does not have any comments. Be the first to leave a comment below.
Featured Product
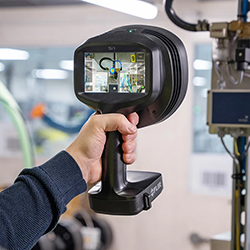