THE RISE OF AUTOMATION IN METAL AM POST-PROCESSING — TRANSFORMING THE INDUSTRY WITH PRECISION AND EFFICIENCY
Across the continually evolving manufacturing landscape, the integration of automation solutions continues to move quickly. For metal Additive Manufacturing (AM) processes the same is true. However, the post processing of metal parts, which is critical for successful outcomes, has been largely overlooked causing serious bottlenecks in the process chain — until now. The automation of post processing heralds a significant increase in efficiency and precision, reshaping how industries approach production using AM. Metal AM has been a game-changer in producing complex parts and components but without automated solutions the post processing of these complex parts involves heavy manual, labour-intensive, and time-consuming tasks. Below, we delve into how automation in metal AM post processing is setting a new industry standard, and how companies like Rivelin Robotics are leading this change with their Netshape® Robots to unlock new productivity and efficiency gains.
The Current State of Metal AM Post-Processing
The conventional approach to metal AM post-processing is a multi-stage process that demands meticulous attention to detail and a highly skilled, steady hand.
The process begins with the essential removal of support structures that are necessary during the printing phase but become redundant thereafter. These supports must be eliminated without compromising the integrity of the core component, which is no mean feat. Once the supports are detached, the surface finishing phase commences, where the objective is to achieve the desired surface smoothness and texture. This could involve a variety of techniques, from sanding and polishing to more advanced chemical or laser-based methods. Following this, heat treatments are often required to relieve stresses within the material and improve its mechanical properties, ensuring that the part will perform reliably in its intended application. Last but not least, rigorous quality inspections are conducted to validate the precision and reliability of the final product.
Each step in this process not only requires a high degree of technical skill but also introduces opportunities for human error, potentially leading to variations in quality and performance of the final parts.
The labour-intensive nature of conventional, manual metal AM post-processing is a bottleneck that inflates production times and escalates costs, often negating the benefits of utilising AM solutions. Skilled technicians must navigate the delicate balance between speed and precision, which can result in a trade-off between throughput and quality. The reliance on manual techniques for tasks such as support removal and surface finishing means that each component's post-processing time is variable and often lengthy. Additionally, the manual handling of parts through these stages increases the risk of accidental damage or contamination, potentially leading to increased rejection rates and wasted materials.
The cumulative effect of these factors is inconsistent final product quality, which can undermine the reliability of metal AM parts and limit their acceptance in critical applications where consistent performance is a must.
The Emergence of Automation in Post-Processing
Automated post-processing solutions have the potential to usher in a transformative era for production applications of metal AM. Advanced robotics, coupled with artificial intelligence (AI) are at the forefront of this new era. Such robotic systems can be engineered to execute support removal with remarkable dexterity, avoiding damage to intricate parts. Surface smoothing, too, is refined by these intelligent machines, which can adaptively polish and perfect surfaces to meet exact specifications. Furthermore, automated inspection systems employ sophisticated algorithms to detect imperfections with a level of accuracy far beyond the capability of the human eye. This shift to automation plays directly to the need for quality and consistency, ensuring that every product meets a set standard before it leaves the production floor.
The move towards automation in metal AM post-processing is not just about maintaining quality, it also enables a strategic approach to streamlining the entire manufacturing process chain. By deploying automated systems for these critical tasks, manufacturers can achieve significant reductions in cycle times, dramatically decreasing the duration from printing to product completion. Importantly, this increase in speed does not come at the expense of quality. On the contrary, it often enhances it, delivering consistently high-quality parts while simultaneously reducing costs. As a result, the investment in automation technology pays dividends in both the short and long term. In a market where competition is fierce and margins are tight, the ability to produce superior products efficiently and economically is not just advantageous — it can be seen as essential for survival.
The Upside of Automation
The key to automation in metal AM post-processing isn't only about ground-breaking technology, it's about the profound impact it has on the way we create and innovate.
It's a game-changer in efficiency, as automated systems don't tire like we do, they keep going, bringing products from concept to reality at a pace that sets new standards. This means businesses can respond to market demands with agility, delivering new innovations to consumers speedily. It's not just about being fast, though, it's also about being smart. The costs saved on labour, the reduction in errors, these aren't just numbers on a spreadsheet. They are potentially the difference between thriving and just surviving in a competitive market.
With the advanced sensors and controls of today's automated systems, tasks are executed with an exactitude that human hands might find challenging to replicate, especially at scale. And then there's consistency, the assurance that every part, every component meets the same gold standard of quality, every single time.
And we must not forget the human side of things. Automation in metal AM post processing isn't just about protecting the bottom line, it's about protecting the people who make things happen. By taking on tasks that involve sharp tools and fine particles, automated systems shield workers from potential hazards, making the workplace a safer environment for all.
And as we look to the future, to a world where sustainability is not just “nice-to-have” but essential, automation steps up. It's a steward of resources, minimising waste and optimising the use of materials, contributing to a greener, more sustainable manufacturing landscape. Companies stepping into the realm of automated post-processing are not just keeping up with the times, they are driving forward, setting the pace for a new era of production that is as much about speed and cost as it is about smarts and sustainability.
As machines take on the repetitive, the workforce is evolving too. The value now lies in the skilled handling of these sophisticated systems — in the programming, maintenance, and quality control that keep them working properly. This evolution is more than just about keeping up, it's about redefining roles and preparing for a future where technology and human ingenuity work hand in hand.
In the area of automated metal AM post processing, we're not just building better products we are also building a better way of working, a safer and more sustainable industry, and thus, a brighter, more innovative future.
Rivelin Robotics and the Future of Metal AM Post-Processing
A key player in this transformative journey is Rivelin Robotics, which develops innovative solutions for automated post processing of metal parts. Rivelin’s Netshape® Robots are designed to seamlessly integrate into existing metal AM workflows, offering an advanced level of automation.
Netshape® Robots are a testament to the potential of automation in revolutionising metal AM post processing. These robots are equipped with state-of-the-art technology to perform various post-processing tasks with remarkable precision and efficiency. By incorporating these robots, companies can significantly reduce manual labour, enhance the consistency of their products, and lower production costs.
Rivelin Robotics' vision extends beyond the immediate benefits of automation. The company is committed to pushing the boundaries of what is possible in metal AM post processing. Its focus on continuous innovation and improvement is aligned with the industry's growing demand for smarter, faster, and more reliable manufacturing solutions.
Summary
The rise of automation in metal AM post processing is more than a technological evolution — it's a paradigm shift in manufacturing. This transition towards automated systems offers unprecedented levels of efficiency, precision, and consistency, that can fundamentally transform the industry. Companies like Rivelin Robotics and its Netshape Robots are not just adapting to this change, they are actively shaping the future of manufacturing.
Comments (0)
This post does not have any comments. Be the first to leave a comment below.
Featured Product
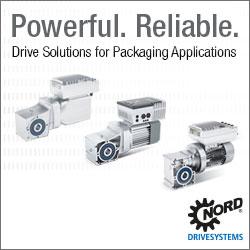