More assembly processes in a smaller space and using less energy
The market for electronic controllers for vehicles is growing. The driving forces are electrification and the increasing number of assistant systems. However, this does not change the competitive pressure to which manufacturers are exposed – especially as a result of Asian companies entering the market. Bosch is meeting this challenge at its plant in Ansbach with a new generation of modular production cells for different production volumes and device types. The aim was to reduce not only the amount of space required through a compact design but also the CO2 footprint. The use of the new compact drive system ctrlX DRIVE plays an important role here.
Robert Bosch GmbH has operated a production plant in Ansbach since 1957. Electronic controllers and mechatronic components for vehicle systems are manufactured there. As the key plant for specific controller types, Ansbach is responsible for industrializing specific products within the international production network.
In addition to reduced costs with increased functionality, customers expect the new controllers to reduce the CO2 emissions resulting from their production activities. It was therefore time to adapt the existing production concept to meet the new requirements.
Compact drives for compact production cells
Following an evaluation phase, those responsible decided to use the automation toolkit ctrlX AUTOMATION from Bosch Rexroth in order to achieve much of this goal. As a provider of automation solutions, Bosch Rexroth has always been a valued partner for the mechanical engineers at Bosch Ansbach.
Friedrich Großmann, who is responsible for control technology and electrical planning at the Ansbach plant, explained: “We have had positive experiences with the IndraDrive Cs drive controllers. Initial tests with prototypes of the new system ctrlX DRIVE gave us the confidence to take the next step towards the more compact design. Working with those responsible, it was easy for us to come up with a plan for production of the new ctrlX DRIVE and to integrate them into our compact production cells from the very start.”
Planning started at the beginning of 2020 and work on the new controllers was completed in mid-2022 with the handover of the final safety functions for EnDat2.2 encoders. As a result of regular consultations between users and developers, any problems which occurred were quickly solved. Thanks to the advance planning, Bosch Rexroth was able to provide the necessary drives on schedule in spite of their high degree of novelty.
Space saved – complexity reduced
The new drives met Bosch's demands for reduced heat generation in a smaller installation space with increased functionality. The use of the latest generation of components with low power loss, i.e. waste heat, coupled with compact designs allows a high drive axis density in the cell with low space requirements in the control cabinet. The central power supply also requires less cabling.
The result achieves exactly the goals described above. Friedrich Großmann explained: “With ctrlX DRIVE, we have taken a huge step forwards and are well prepared for the future. The electrical planners and developers certainly overcame their initial reservations. Both the compact design and the trouble-free integration of functional safety are compelling factors. The first production lines equipped exclusively with the drive system ctrlX DRIVE are already producing standard parts.”
Klaus Kamps, head of technical functions in Ansbach, added: “This development was important to achieve greater sustainability in production. It is also essential that we reduce complexity and are able to use tailored packages comprising control systems, drive controllers and drives.”
Powerful drives for energy efficiency and future-proofing
At the same time, ctrlX DRIVE is addressing an increasingly important issue in the market: Bosch in Ansbach is now able to achieve greater energy efficiency. One way it does this is with a shared DC bus which helps to avoid energy wastage with a braking resistor during the deceleration process of a drive axle. Because this surplus energy is available to all drives in the axis group through replacement, less energy is required from the grid overall and the power supply to the machine can also be reduced.
Klaus Kamps said: “With ctrlX DRIVE we are on the safe side too. It features a comprehensive safety concept. For example, the SafeMotion options can be selected reliably via the FailSafe over EtherCAT (FSoE) protocol. This ensures efficient wiring via existing EtherCAT lines. As a result, we can adapt to the particular situation optimally in order to ensure the safety of personnel in the assembly cell.”
By using the drive system ctrlX DRIVE, Bosch in Ansbach can significantly reduce the resources needed for its industrialization solutions, achieve a high level of energy efficiency and ensure complete safety. With the overall ctrlX AUTOMATION concept, the company is also ready for future challenges and can carry out expansions flexibly if necessary. Klaus Kamps explained: “We want to continue on the way towards greater sustainability, efficiency and agility. Given the very positive results when using ctrlX DRIVE, we are also planning to use the control system ctrlX CORE in our plant. With its app technology and openness, the industrial control system will help us to achieve our goal of agile production.”
Comments (0)
This post does not have any comments. Be the first to leave a comment below.
Featured Product
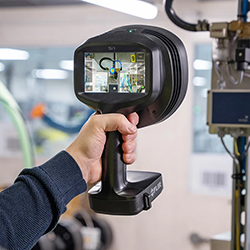