Manufacturing the future: How plants can harness the power of AI
Artificial intelligence (AI) has emerged as a transformative force in manufacturing. From streamlining systems to accelerating decision-making, new tools in the industry have the potential to unlock efficiencies and boost output.
Depending on the challenges a specific company is facing, AI can provide tailored solutions that address particular pain points. Whether improving visibility, optimizing systems or even forecasting the future, the tools available today can solve problems that have long hampered productivity.
With new capabilities being developed every day, now is the time for companies to assess how AI can align with — and improve — their processes. By doing so, they can be among the first to usher in new growth.
A Holistic Picture
For employees in the manufacturing space, there is power in knowing how their work fits into the larger picture. But information technology (IT) systems — those designed to manage information and communication — and operational technology (OT) systems — those that monitor events, processes and devices — are often isolated.
In addition, OT systems are typically organized in layers, meaning different information is visible to different users at different times. When data is siloed in departments or platforms, it can be challenging for individuals to get a holistic view of operations. Without this insight, it can be almost impossible to make data-backed decisions. But with AI, companies can combine data from each piece of equipment in a facility onto one platform. This can break down the barriers separating the people from the plant.
For example, rather than calling their team to gather intelligence, a plant manager could use AI to get direct and real-time data on the facility they oversee. This saves time and enhances synergy, empowering decision-makers to act promptly and with the most relevant information in hand.
Building Forecasts, Mitigating Risk
With IT and OT systems linked, AI tools can interpret information within the context of a company's entire footprint. By harnessing data from across a plant or company, AI can analyze information to detect patterns. Employees can use these capabilities to create forecasts or project hypothetical outcomes based on historical data.
Companies can use AI to model anything from product demand to upkeep needs. Traditional repair practices, for example, can lead to unnecessary downtime and expense. By using AI, manufacturers can assess data from sensors and equipment to predict and mitigate issues before they arise.
In one case, Stefanini worked with a leading steel production and distribution company struggling with a particular maintenance issue. During the steel rolling process, dust and other contaminants frequently cause equipment blockages. These would force the company to pause production, costing them time and money and, in some cases, causing accidents.
Stefanini partnered with the client to create an AI model that would continuously monitor the rolling mill process. Compared with the previous solution, the AI could detect twice as many blockages and determine whether alerts were real or false. By proactively identifying blockages, the company reduced energy consumption by 4% and made the steel rolling process faster and safer for operators.
Companies can also use AI to simulate "what if" scenarios; for instance, how would reducing raw materials affect production? By testing these possibilities, a business can "future-proof" its model, preparing for different scenarios that could impact its processes and profitability.
Streamlining Decision-Making
Once a company has deployed AI to link systems and contextualize data, generative AI can allow decision-makers to request concrete data and analysis. For example, Stefanini’s manufacturing artificial intelligence platform, SAI Plant Assistant, can understand and respond to human language prompts. SAI Plant Assistant can retrieve, group and analyze information, streamlining employee experiences.”
With traditional IT and OT systems, users often have to navigate multiple platforms to gather the information needed to make an informed choice. They would then spend time interpreting this, possibly pulling in other stakeholders with access to additional data points or context.
AI simplifies this process. By leveraging AI to collect and assess data, employees can reduce the time spent analyzing events and move straight to decision-making. In fact, Stefanini’s data suggests that AI can enable companies to cut decision-making time by 50%. For this reason, virtual assistants — which enhance human processes to improve efficiency — will likely be the next mass technology adopted in manufacturing.
In some cases, AI can also support the actual decision-making process. Stefanini recently collaborated with a prominent global paint and coating manufacturing company to optimize the client’s business processes. Stefanini built a platform that uses constraints like data inputs to automate decision-making. The solution increased the client's production capacity by almost 10%.
Embracing a Smarter Tomorrow
Today, manufacturing plants generate massive volumes of data. Companies depend on this data to make decisions about maintaining plants, developing products and distributing materials and goods. As the manufacturing ecosystem becomes increasingly complex, companies will rely on AI to streamline and optimize processes by connecting systems, contextualizing data and communicating information.
AI can augment human labor and decision making at every stage of the manufacturing process. It can manage logistics, predict maintenance needs and ensure products meet quality standards. This, in turn, can bolster productivity, trim costs, decrease energy use and encourage innovation.
As the industry evolves, AI represents a fundamental shift in how companies operate. Businesses that embrace these advancements early on stand to gain the most as manufacturing transitions toward a smarter, data-driven future.
Comments (0)
This post does not have any comments. Be the first to leave a comment below.
Featured Product
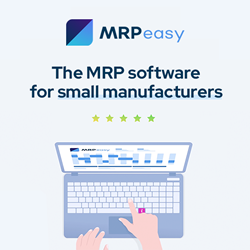