The secret to success in food & beverage manufacturing
In an era of increasing sustainability demands, food insecurity concerns, and escalating material and energy costs, companies in the food and beverage industry face a myriad of challenges. Not only must they deliver safe, high-quality and innovative products, but also adapt to the ever-evolving demands of consumers.
Navigating such a volatile environment leaves little room for error. Be it due to machine downtime, inadequate maintenance, unplanned stops, production rejects, or waste, the list can be endless. But there is light at the end of the production line (or tunnel) and that lies in operational efficiency. Success may take different forms for each business, but one critical ingredient remains constant – data.
The power of OEE
LineView, a smart factory solutions provider, was founded to address precisely this challenge, recognising that it is impossible to understand the true casual losses in a system without high-quality data. In response, it developed a solution that empowers manufacturers to see the bigger picture and identify actual losses along the entire production line, not just isolated machine downtime.
LineView's software leverages the power of Overall Equipment Efficiency (OEE), a key metric for measuring a manufacturing process's effectiveness. OEE takes into account machine availability, performance, and quality to provide a holistic view of a production line's efficiency. By capturing and analysing real-time data, LineView helps manufacturers improve OEE, thereby maximising the utilisation of existing resources.
While the solution may seem straightforward, its benefits are extensive. By unlocking data-driven insights and enhancing OEE, LineView's software enables real-time monitoring, predictive maintenance, optimised production schedules, and improved quality control.
By painting a clear picture with data, businesses can make informed decisions that support resource utilisation and optimisation, resulting in improved energy efficiency, water and waste reductions, and reduced production costs. Ultimately, this leads to maximised output from existing resources and frees up additional capital expenditure (CAPEX).
Coca-Cola Enterprises (CCEP) is a client that has reaped the reward of capturing such data. Selecting LineView as its standard production line monitoring system for their Supply Chain Division, the software was implemented on every production line in Europe to help increase efficiency and reduce manufacturing costs. Within 24 months, CCEP saw a site-wide increase in OEE of 20% as well as improvements in yield, quality consistency and ROI.
The secret ingredient for success
With over 20 years’ experience working with industry giants such as Coca Cola and PepsiCo, and decades of manufacturing expertise, LineView is uniquely positioned to support clients in the food and beverage sector. Their team of industry veterans works tirelessly to help operators in the food and beverage sector achieve maximum productivity across production and packaging lines.
Integrating or introducing technology into production lines can be a daunting task, especially when transitioning away from legacy systems or processes. However, by shifting from manual data entry by operators and reporting via spreadsheets to a connected platform, businesses can unlock efficiency savings of 1-2% simply by replacing labour-intensive logs and checks. Partnering with a team that understands the nuances of the industry can significantly ease this transition.
Data is undeniably the star ingredient for success in improving operational efficiency in the food and beverage manufacturing industry. By leveraging solutions like LineView, manufacturers can navigate the challenges of workforce restraints, optimise their operations, and maximise output from existing resources, ultimately ensuring their long-term success in a dynamic industry.
Comments (0)
This post does not have any comments. Be the first to leave a comment below.
Featured Product
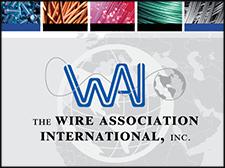