CLEANING UP AM’S DIRTY SECRET
Okay, so it is not really that much of a secret any more that the post processing stage of the additive manufacturing (AM) workflow is a challenge for many applications of AM. “Challenge” is doing a lot of heavy lifting there, for the record. For metal AM applications in particular, the post processing of the parts remains a dirty, costly, time consuming and labour-intensive operation.
This is not rhetoric, it’s not even a sales pitch. It’s a real problem. For a number of years, it was a specific problem that I wrestled with, working as a metals production engineer at 3T-AM (BEAMIT). To be clear, I am a big fan of AM, its current capabilities and its ongoing potential for a more sustainable future. I believe in it and the benefits it can bring for manufacturers large and small; global and local. However, when I say “wrestle”, I use the word advisedly. Hand tools and dremmels were not out of the question in the battle to remove supports and finish parts.
Thus, when I witnessed many of the metal AM OEMs marketing their systems as clean, digital processes, with little to no acknowledgement of the post processing steps that are required, it used to grate somewhat. In the interests of brevity, post processing metal AM parts, especially the complex ones (and let’s face it, that’s a dominant reason for using an additive process in the first place) invariably involves a number of dirty, manual tasks to remove excess powder, remove the part(s) from the essential base plate, remove the intricate supports that complex geometries require, all before finishing the surface to the prescribed standard. These tasks are necessarily performed by skilled workers that are often tucked out of sight and certainly not shown in any marketing videos. Anyone working in this area past or present knows why – it’s just not pretty.
That is the over-arching problem, but it’s not the only one. The fact that post processing metal parts requires such intensive manual intervention throws up a series of follow-on problems. These include part-to-part quality inconsistencies, repetition fatigue, significant health & safety risks, and, of course the high costs associated with such labour intensity and long lead times.
I went in search of solutions, and when nothing was forthcoming, I resolved to come up with one myself. And that is how Rivelin Robotics was founded and we put together an expert team to develop and commercialise a workable and sustainable solution.
Today, Rivelin’s Netshape Robots offer a much cleaner approach for metal post processing and closes the gap that exists in AM’s digital process chain by removing manual finishing steps. Automation is the key, with 8-axis robots (6-axis robots + 2-axis positioner) driven by the advanced and intelligent Netshape® software, which not only automates the support removal and finishing steps, but also provides process data, reliability, consistency and traceability.
In the following sections, I will address some of the key problems in more detail and look at how automation is meeting the needs of industry.
POWDER REMOVAL
The Problem: Due to the nature of the powder bed fusion (PBF) process, whether that’s with lasers or electron beams, unsintered and semi-sintered powder will remain within holes and internal channels of additively manufactured components. If it is not removed, the residual powder can seriously compromise part functionality. The manual work required to remove powder is hazardous and, often, results vary from part to part and from site to site. This variability presents a complex risk in product development that can be costly to manage and resolve.
The Netshape® Solution: Rivelin Netshape® Robots uses a combination of pneumatic and electro-mechanical tools to release caked, semi-sintered, and un-sintered powder from metal parts. They can adapt to variability in the condition and location of holes, corners, and channels using a 3D vision system and dynamic planning capability. Rivelin’s automated calibration system enables engineers and technicians to quickly set-up and start production runs using their existing levels of knowledge and intuition.
PLATFORM REMOVAL
The Problem: Metal parts and components produced using the PBF process are removed from the machine attached to a rigid metal platform. Again, this is due to the inherent nature of the process and is necessary for a successful build.
Wire EDM (Electrical Discharge Machining) is frequently used as a way to de-platform parts, but it can be unreliable around metal powder due to shorting and wire breakages. Another alternative is to use conventional tools such as bandsaws to break the part away from the base plate, but these can be susceptible to drift without any form of positional feedback. It’s an unreliable process at best, and may require rework. At worst, parts have to be scrapped completely. In addition, both of these methods are expensive and require large-footprint machines that require skilled operation. If the job is outsourced, it adds considerably to the lead time and overall costs of the part.
The Netshape® Solution: Rivelin’s Netshape® Robots can accommodate end-of-arm tools that can remove base plates in a wide range of materials, while adapting to warping and variability using a 3D vision system and dynamic planning capability. It includes a grinding-specific force control system that reacts and stabilises non-linear machining forces. The clever bit is the autonomous programming enabled by Netshape®, which empowers engineers and technicians with no prior robotics experience to quickly create robot trajectories and tool operations. It compares favourably against the traditional methods above, and it improves accuracy and reduces waste.
SUPPORT REMOVAL
The Problem: Metal AM parts require metal support structures to prevent sagging and deformation of overhanging geometries. Support removal is, by far, the most labour-intensive part of AM post-processing. I know this from experience, and also from talking with anyone that has ever been directly involved in metal support removal. When including surface witness removal, the entire support removal process can account for upwards of 25% of total part cost.
Support removal is a skilled, sometimes hazardous, and always unpleasant manual task requiring years of experience to perfect. Moreover, irrespective of the skill of individuals carrying out the work, a manual process leads to variability between parts and from person to person. It also introduces inaccuracies that can compromise end-use functionality and design intent. In addition, human error (and no one is infallible) can lead to mistakes that cannot be rectified, meaning parts have to be scrapped altogether.
As you can imagine, I have spoken with innumerable people now about this issue. Here, I am going to quote just one of them, to give a flavour of those conversations. It resonates. This is an early adopter that Rivelin Robotics has been working with: “Automated support removal would mean removing not only one of the most labour intensive processes in the AM chain, but also improve productivity with reliable turnaround times every time for every part.”
The Netshape® Solution: Rivelin’s Netshape® Robots are enabled by Netshape control and perception software. This drives a combination of pneumatic and electro-mechanical tools that can remove supports and surface witnesses in a wide range of metallic materials. The automated robots can adapt to fixture and part variability using a grinding-specific force control algorithm and a “Scan & Plan” system. In addition, the automated calibration system enables engineers and technicians to quickly set-up and start production runs using their existing levels of knowledge and intuition. It’s quick. It’s clean. It's accurate. And it's repeatable.
FINISHING AND POLISHING
The Problem: Additively manufactured components produced using PBF processes often exhibit high surface roughness and visible layers, due to the nature of the process. For some applications the surface finish is a non-issue and polishing is not required. However, for many applications, it is. To date, localised polishing has typically been carried out by hand (more manual labour, with all of the inherent issues outlined in the previous sections, compounded further) or in a rigid machine tool. The latter of these two is also expensive and introduces other quality issues due to the surface variability often found in AM parts.
The Netshape® Solution: Rivelin's Netshape® Robots can utilise metalworking tools to linish, fettle, and polish a wide range of metallic materials. Powered by Netshape®, the robots can adapt to surface feature variability using a 3D vision system and dynamic planning capability. The force control system reacts to machining forces and tracks a desired polishing pressure to achieve a consistent surface finish to required levels, and a non-contact tool wear monitoring system maintains a stable process.
IN CONCLUSION
For anyone directly involved with the production of metal AM parts, manual post processing is likely to be the bane of your job. It’s hard, filthy work and it is not without risk. For anyone responsible for the production of metal AM parts, those post processing costs on your financial spreadsheets are likely causing you a headache. So much so, that it can even result in negating the advantages of using AM in the first place. Rivelin Robotics exists because of those problems and it has developed legitimate and provable solutions to address them. The power of automation is being realised to improve quality output and reduce defects by up to 90%, eliminate human risk and variability, provide traceability and make the whole process cleaner, in line with the promise of AM. What’s more, the financials look good too, with results demonstrating up to a 10-fold reduction in operational costs.
As a company Rivelin aims to drive the uptake of AM, which we see as a major contributor to a sustainable future, and which will have lasting benefits for our environment.
Comments (0)
This post does not have any comments. Be the first to leave a comment below.
Featured Product
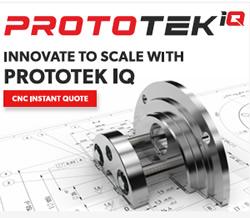