6 Benefits Of Augmented Reality In Manufacturing
Manufacturers are increasingly incorporating augmented reality in their digital transformation strategy. Augmented reality provides a multiplier effect for improving the efficiency and quality of production and inspection processes.
Defect detection assistance, improved production rate, increased safety for your factory and teams, increased productivity, reduced cycle times, and, above all, reduced costs: the benefits are numerous!
AR allows the industrial sector to gain effectiveness and efficiency while reducing errors and the additional costs generated, but it does not stop there. The team at DELMIA take a closer look at some of the main benefits of augmented reality in manufacturing.
1- Increasing productivity through augmented reality
AR is a solution whose effectiveness and value to the industry are more proven than ever to increase industrial productivity. When used in factory and production processes, there are many gains you can make in your quest for operational excellence.
In addition to allowing you to be more effective and fast in each of your tasks (assembly, inspection, maintenance), such a solution will enable you to be more efficient by optimizing processes and providing digital instructions for operators.
Your teams can identify non-conformities faster and drastically reduce errors and related costs. Operations are performed correctly by having the right information in the right place at the right time and assigned to the right person.
To summarize, whatever your industrial performance, it will be optimized thanks to:
- Faster learning curve for new operators
- Reduction of inspection time (DELMIA Augmented Experience provides up to 84% reduction of inspection time measured at our customers)
- Reduction of your cycle times and reporting
- Automatically updated reports and documentation
- Better traceability
2 –Improving quality through AR
The detection and reduction of non-conformities are one of the main objectives of the teams in charge of inspection and quality. As we all know, the slightest error can be extremely costly and leads to a series of time-consuming corrective actions, such as:
- Correct identified defects
- New production runs
- Several additional quality controls
- Possible additional logistical costs
- Generate dissatisfaction for end customers
A detected non-conformity or error often implies more time to devote to the handled part, which can even go as far as stopping the production to identify and resolve the problem. The challenge is to detect errors as early as possible in the process to avoid late detection and the need to stop production. A major challenge, especially when you want to be part of an operational excellence strategy.
An augmented reality solution allows you to anticipate these errors. With an AR tool, quality control information is contextualized and localized to simplify the inspection process. Operators are guided through each inspection point using 3D data imported directly into the field and superimposed on the part to be inspected throughout the manufacturing process. This capability supports efficient validation of product conformity. In addition, errors are precisely localized, allowing the proper corrective and repair actions to be applied. DELMIA Augmented Experience solutions are already helping many industrial customers identify and efficiently report production defects.
But the best way to reduce quality problems is to avoid assembly errors in advance. AR effectively guides the operator to achieve “first time right” via the contextualization of work instructions and their display in the field, making them intelligible.
3 – Connecting the field with new digital capability
What if the augmented operator was the connection point that could reconcile the real and virtual worlds? Displaying digital data from the design teams on the shop floor places allows the operator to interact with the data. AR becomes the link to creating a tangible connection between the Virtual (and all the digital information from the engineering office), with the Real, meaning the operations happening on the field.
Implementing an augmented reality solution, especially if the chosen technology offers integration capabilities with the existing systems (MES, for example), may be the answer to the digital gap between V + R.
4 – Supporting the future operator by boosting skills development
Integrating AR solutions in your factory can positively affect team training. The simple fact of using augmented reality contributes to your operators’ training and increases their skills. Using digital work instructions projected in the field or visualized through a tablet or augmented reality glasses, your field teams receive the right information at the right time and become operational more quickly.
It is proven that using a virtual world facilitates the assimilation of information communicated and its application in the field. This way, your operators develop much more intuitive gestures allowing them to become more autonomous and to respond well to possible issues. In addition, it also facilitates the memorization of the information that you transmit to your teams.
Integrating an augmented reality solution fits perfectly into a training strategy. It facilitates the transmission of knowledge within your company and develops your operators’ autonomy more quickly, thanks to its more intuitive content.
5 – Providing a safer and more comfortable work environment
Better security and fewer errors for your industry
Augmented reality technologies can also improve your factories’ safety and comfort. Complex assembly operations or maintenance actions provide significant support, consider many risk factors and detail faults with better accuracy than any other resource (documentation or technicians).
Comfort: The various hardware configurations compatible with augmented reality solutions allow workers to adapt to the workstation. The variety of hardware enables them to work hands-free and avoid numerous return trips to the office. A savings of time and energy that also provides comfort for your teams.
Technician safety: Your operators are better guided and accompanied step-by-step with alerts displayed in AR at the proper process moment.
As a result, the risk of human or technical errors is reduced, and your field teams better understand your processes.
6 – Optimize documentation, traceability and reporting
Augmented reality supports a solution for better industrial traceability. Getting the right information at the right place at the right time can be complex. Manufacturers need to be aware of a lack or break in collecting field data and documentation that is not up to date and too difficult to use.
Using augmented reality in your plant can positively impact your traceability. A good AR solution offers “as-built” data collection capabilities in the field with automated reporting, which provides full visibility into the assembly and inspection processes throughout the product production and distribution chain.
We help industries optimize their traceability with innovative digital solutions that provide automatic data collection directly from the field following quality control. With such a solution’s capabilities, you can conduct documented inspections for internal traceability purposes and better communication with your customers.
Digital continuity thanks to augmented reality
In summary, augmented reality has many advantages in industry
- Augmented Reality helps achieve operational excellence (getting it right the first time)
- AR solutions bring rapid ROI by improving quality, deadlines, productivity, etc.
- AR improves your traceability and contributes to the collection of data that will feed the digital twin
- It encourages the development of your operators’ skills
- It contributes to the reduction of your cycle times by reducing your assembly and inspection times
Thus, you can optimize your performance considerably and reinforce your manufacturing processes with augmented reality.
Comments (0)
This post does not have any comments. Be the first to leave a comment below.
Featured Product
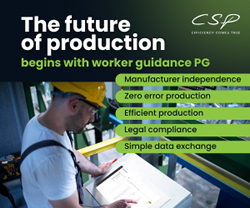