Digital transformation: How manufacturing is riding the cloud to new heights
Once a laggard in adopting digital technology, the manufacturing sector has made significant gains in recent years. Today, companies are hooking into cloud technology and continually digitizing operations. As a result, they’re able to better handle disruption and dramatically advance efficiency and initiatives across their organizations.
Still, those in manufacturing do face more obstacles than other industries as part of their digital transformation journey. From headquarters to satellite offices to overseas facilities, data can get trapped in disconnected systems. To integrate and leverage this trove of siloed information, special applications are needed, as are purpose-built devices to harness sensor data which is critical in the manufacturing process. All of this greatly expands a manufacturer's attack surface, creating security vulnerabilities that are drawing cyber criminals in record numbers.
That said, the following can help manufacturers advance their digital efforts, while safeguarding their companies from threats that could severely undermine their business and reputation.
Staving off attacks
According to a recent Sophos survey and report, the manufacturing sector has been significantly impacted by cyberattacks. More than 60% percent of respondents noted an increase in the volume of attacks over the prior year, with 66% reporting greater attack complexity. When it came to the greatest threat of all, ransomware, 55% said their organization had been hit, an increase of nearly 40%. Such a breach can bring an operation to a screeching halt, the resulting downtime impacting both the manufacturer and their customers.
The main problem is far too many manufacturers manage and protect staggering amounts of data with aging IT systems that are bound to come up short. Increasing IT resources can help counter this, but equally important is updating and enforcing cybersecurity best practices. Requiring employees to use strong, regularly changed passwords that are never shared is vital. Furthering protection with dual-factor authentication should now be standard practice.
Educating employees on cyber hygiene is paramount. Hackers often gain entry to company systems by targeting employees with phishing attacks, which can launch a file infected with malware or expose credentials by simply clicking a link. That said, ongoing threat training for everyone – from the factory floor to the CEO – can go a long way in reducing exposure and staving off attacks.
Back to business
Today, it’s not a matter if you’ll be hit by attacks like ransomware, it’s a matter of when. And when it does happen, what matters most is the speed of recovery. That’s why every manufacturer should have a plan in place to ensure fast, effective response.
Most companies rely on legacy storage and antiquated backup systems to recover from a ransomware attack. Unfortunately, these can’t handle the massive amounts of data generated in manufacturing; many companies have locations worldwide that collectively generate thousands of terabytes of data on a monthly or yearly basis.
Recovering volumes of information that has been infected consumes a lot of time and effort, and in the process, clean data that was never impacted can be lost. What’s more, even if IT responds immediately to an attack, full recovery could still take weeks or months depending on the spread of the attack. That said, it’s understandable that the toll of downtime and disruption can lead many executives to decide it’s less costly to pay the ransom and get back to business.
Keep in mind, though, that meeting ransom demands doesn’t necessarily result in a fast or full recovery. An estimated one-third of businesses that pay up never recover all their data. Furthermore, paying the ransom can paint a big target on a company’s back as it only encourages hackers to return knowing that the target promptly paid previously.
Manufacturers need continuity, not cyber chaos. They must develop and have at the ready an effective response plan, one that is reviewed and updated regularly to keep pace with the increased sophistication of threats.
Riding the cloud
Increasingly, manufacturers are finding answers to such issues in the cloud. There, data can be immutably stored so it can’t be encrypted or altered in any way to create what could be a company-saving master copy. File storage systems can also enable IT to rapidly identify the exact source of an attack, supported by capabilities such as alerts, in-line edge detection and detailed logging of activity and IP addresses.
Through the cloud, ongoing file versioning can provide endless recovery points, with snapshots able to be taken minutes apart. IT teams can quickly assess the damage and begin recovering only infected files without adversely impacting unaffected data. In doing so, a recovery that could take weeks or months can be accomplished in hours, even minutes.
Further, this increased protection doesn’t sacrifice usability. With the cloud, global file systems, that can cache active data at the edge, can maintain data integrity and facilitate management. And wherever users are they can access their data, which can provide even the most distributed organization with easy access to file data that covers all company locations.
New heights
Cloud-based file systems can reduce costs significantly compared to legacy technology. In the event of an attack, these systems offer a much faster recovery and return to productivity, regardless of the location of facilities or employees. Manufacturers can detect ransomware at the edge to head off its damaging spread. And not only can the cloud accommodate the restoration of millions of files in moments, but it also updates security to handle new and evolving threats.
Cyber threats aren’t going away, they’re becoming more complex and frequent. A cloud-first approach that incorporates a robust data protection, recovery and distribution strategy is now a must-have in manufacturing. A cloud-based platform will not only offer formidable protection, it ensures uptime, delivering business continuity that’ll take them to new heights even in the midst of a difficult economy.
About Russ Kennedy
Russ Kennedy is chief product officer at Nasuni, which provides a file services platform built for the cloud. Previously, he directed product strategy at Cleversafe through its $1.3 billion acquisition by IBM. He has served in a variety of product management and development roles, most notably at StorageTek (acquired by Sun Microsystems), where he brought several industry-leading products to market. Kennedy has a BS degree in Computer Science from Colorado State University and an MBA from the University of Colorado.
Comments (0)
This post does not have any comments. Be the first to leave a comment below.
Featured Product
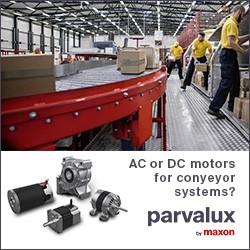