MICRO MOLDING — THE TOOLROOM PERSPECTIVE & DfMM
There is a world of difference between how a product looks on a computer screen when it comes to scale, and its scale in reality. Right at the beginning of the design stage of product development, it is vital when looking to micro mold a part that the scale of the part itself — and especially the scale of some of its internal features — are given due consideration. In other words, parts may look great conceptually, but they may be impossible to actually make.
In this article, the central importance of Design for Manufacturing (DfM) will be emphasized, and indeed I will go as far as to say that we should perhaps emphasise Design for Micro Molding (DfMM), as the unique challenges of micro molding can hugely influence the success or failure of a project. DfMM has a massive impact on the tool build; this will therefore have a disproportionate effect on product development time, cost, and indeed the quality of final product.
360 DEGREE PERSPECTIVES
Success in micro molding is truly a result of multi-disciplinary expertise. Tooling is only one of a number of critical areas where your chosen micro molder must show experience and knowledge. The best micro molders are truly vertically integrated, and teams from design, tooling, molding, validation, and automated assembly must work collaboratively to optimize the outcomes of product development on behalf of customers.
It is also important that individuals within specific departments have a rounded view of their own area of focus. For example, my career in toolmaking started at a die shop which I left after a year to come to Accumold where I have worked for 17 years. At Accumold, I began by applying my die experience to the development and maintenance of dies and molds in lead frame systems. While working with these systems I gained some automation experience, and I also began to focus on mold maintenance and repair. With some cross training I learned to program and cut electrodes that were used on all my repairs, which led me to program and cut electrodes full time for about 2 years before returning to the bench to build micro molds. Exposure to many different areas of the business has given me a unique perspective which has proven valuable when working with DfMM and tool fabrication. This rounded view of the world, depth of knowledge, and experience in all areas of Accumold is the key driver for customer product development success.
MICRO TOOLING – SPECIFIC CONSIDERATIONS FOR DfMM
When the team at Accumold start discussions about a potential project, we discuss things such as gating, ejection, mold splits, and direction of pull.
Ejection & Gating. Often when a part gets smaller, the first thing that gets eliminated or ignored in the design is any consideration of ejection or gating, however the engineering team understands that a part cannot be made without either of these. Keeping gating and ejection in mind during part design can optimize the DfMM and tool build process. For example, having a small ejector pin on a thin and deep feature can make burning a start hole difficult or impossible. Also, gating in a thin area when there are other thick areas on the part can cause non-fill and sink. When planning for gating and ejection we must anticipate some gate vestige or flash, so in an assembly of parts this may have to be planned for. When deciding mold splits it can turn a simple tool build into a very complex one or it can turn a tool that was going to be very difficult to run into a tool that runs extremely well.
Split Lines. When looking at split lines, very often customers prefer not to have them in certain areas due to flash. However, changing from an ideal split line from the tool perspective can cause unforeseen consequences to the tool build.
A project comes to mind where the preferred split from the tool making perspective would have been a saddle shutoff, but due to flash concerns, the shutoff was placed on a slide to make the flash direction perpendicular rather than parallel. The slide created some cosmetic areas on the part, so this caused us to shutoff on the cosmetic surface. The unforeseen consequence of this was that there was more flash than anticipated in the windows in the preferred flash direction, and there was some mismatch between the slide and the rest of the cavity. Doing a saddle shutoff in this case would have put all the cosmetic surfaces on one side of the tool, and while the potential for flash would still have existed, the shutoff would have been in the direction of clamp rather than on a slide pull. This would also have eliminated a split line on the cosmetic surface and would have improved the overall part appearance.
A slide with a large surface area presents the possibility for injection pressure to flex the mold so if you can have a shutoff in the direction of pull it is always a more robust shutoff. The direction of clamp holds a shutoff together as a direct result of clamp tonnage, while alternatively a slide is a factor of the tonnage reduced by the heel angle and strength surrounding mold steel.
Feature Size. Another thing that can influence tool build is feature size. I can think of several times where the part tolerance was used to increase the thickness of an area in order to fill. When working with micro molded parts it is best to remember that although it may sound like a small change it may represent a large percentage of the feature size. For example, if you have a part with a .004” (0.1 mm) wall thickness, changing that wall thickness by .0005” (0.013 mm) is a 12% change and may mean the difference between filling the area reliably or not.
When it comes to creating electrodes to burn the cavity the amount and difficulty can be greatly affected by the design of the part. For example, if there is a square counterbore with sharp corners we may have to use 4 different electrodes to create this feature; If the part had radii added at the corners this may be possible using only 1 electrode. The depth of the feature is something to think about when adding radii as well. An extremely small radius on a deep feature may not be possible to cut, so if the radius can be increased slightly it can change the difficulty of the electrode significantly.
When it comes to ensuring a part will release from the cavity, an important factor — especially when dealing with very small features — is draft. Often with small parts, draft is an oversight because it is going to be such a small amount. Again, it is important to look at percentages instead of actual sizes. Adding 0.5 degrees draft on a 0.10” (0.25 mm) tall feature may not sound important, but that can add 0.0009” (0.023 mm) of draft, so on a thin 0.010” (0.25 mm) feature, it is almost 10% of the feature’s thickness.
Assembly. Consideration of assembly of several parts is also important in terms of final product optimization and ease of tool build. When building a mold, it can be easy to believe you are in a situation where everything must be machined exactly to size. I prefer however, to hedge my bets and add clearance when possible to minimize the amount of areas that need to be accurate. Adding clearance allows the choice of a less accurate method to manufacture for certain parts, leaving the accurate machining to areas where it is needed which saves time. Clearance on the parts being molded can be approached the same way. This also applies to the part tolerance on a plastic part.
Accumold offers a service that many other molders do not, and that is the involvement of the technical team very early on in the process of product development. This involvement from project kickoff all the way through production of customer parts ensures that a consistent view of DfMM will not only improve the reliability of the mold but also reduce the time it takes to manufacture. The Accumold team is focused on finding solutions for issues that may seem insurmountable and optimizing project outcomes.
Jeremy St. Peter is the New Tooling Team Leader at Accumold. The company has grown to a 130,000 square foot fortified facility designed for assurance of supply, employs over 350 staff, and is a net exporter shipping all over the world every day from its Ankeny, IA, USA facility which runs 24 hours a day, 7 days a week.
Comments (0)
This post does not have any comments. Be the first to leave a comment below.
Featured Product
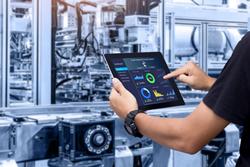