HOW COMPOSITES BENEFIT THE TRANSPORTATION INDUSTRY
In 2018, an estimated 142 billion gallons of gasoline were consumed in the United States, with heavy goods vehicles (HGVs) attributing to 20 per cent of this figure. With the environmental impact of fuel clear to see, composite materials have the power to drastically reduce unnecessary fuel consumption. This is only one way composites can benefit the transportation industry. Here, Jari Sopanen, Product Business Owner for Transportation at global composites manufacturer Exel Composites, explains more.
American retail giant Walmart demonstrated that, by using carbon fiber in the panels of its “green” concept truck, it could reduce vehicle weight by one third, while conserving fuel. With a high strength to weight ratio, environmental advantages and reduced maintenance costs, the transportation industry is reaping the benefits of composite materials.
Larger, but lighter
There is a trend in the transportation industry for larger vehicles. Whether it’s busses, trains or articulated trucks, the idea is simple; carry more cargo. The challenge is to find ways to safely carry greater loads, while saving fuel and reducing environmental impact. Composites offer impressive answers to this challenge.
Depending on the vehicle’s purpose and its number of axles, road traffic regulations such as those developed by the European Commission restrict the weight limit a HGV can carry. However, a lighter vehicle is able to carry more payload. Replacing heavier metal parts in HGVs with composites frees up more cargo payload capacity while remaining within the legal limits.
As a result, fewer vehicles are required to transport the same amount of goods, improving the overall fleet fuel efficiency, and reducing fuel, fleet and personnel costs.
Better for the environment
Besides fewer vehicles on the road, many automotive producers are looking to grow their electric vehicle (EV) fleets. Here, composites also offer additional benefits when it comes to an EV’s battery box, providing good thermal management that helps demonstrate the environmental advantages of composite materials.
The enclosure that houses the vehicle batteries can also benefit from composites. Rather than building a battery box from aluminum or steel, composites such as carbon fiber, can save around 40 per cent of the weight.
Another option, fiberglass, is 200 times more thermally efficient than aluminum, which makes it an ideal material for the battery enclosure as it better shields the battery from the heat and contributes to a faster and more energy saving coldstart in colder conditions. This is important because maintaining the battery box’s internal temperature requires energy to heat or cool the box accordingly. Using more thermally efficient materials in the battery box’s construction reduces the energy consumption of the vehicle.
Reduced maintenance
Vehicles in the transportation industry must operate for long durations and can become susceptible to corrosion from moisture and chemicals in road salts, increasing maintenance frequency. Many vehicles with metal components are treated with a substance containing a corrosion inhibitor, which adds a corrosion resistant coating to the material’s surface. This is less effective as it wears off over time and maintenance must be carried out to restore the part’s condition.
However, composites are naturally resistant to corrosion, which means that vehicles can operate for longer without the need for frequent maintenance.
Exel Composites works closely with transportation customers to design and manufacture composite solutions for trucks and trailers, buses and coaches and rolling stock. Using profiles from fiberglass, carbon fiber and hybrid composites, we design components to make vehicles lighter, improve fuel efficiency and help to reduce lifetime operating costs.
Recently, Exel provided fiberglass profiles for the skirt and side panels of electric buses from Chinese bus and coach supplier, Yutong. The buses were delivered to Finland as part of the country’s goal to reduce its carbon dioxide emissions by five million kilograms a year.
As HGVs account for a huge proportion of fuel consumption, it’s vital that manufacturers look towards new ways to optimize essential transport fleets. Walmart has demonstrated that it is possible to cut vehicle weight and conserve fuel by calling on composite parts, and the wider industry should take note.
Comments (0)
This post does not have any comments. Be the first to leave a comment below.
Featured Product
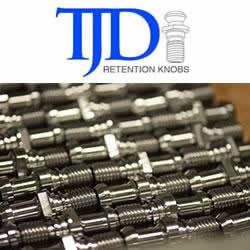