Did COVID-19 help reveal the path forward for industry?
While initially concerned at the impact of remote work mandated as part of COVID-19 safe working practices, many industrial leaders were encouraged to find the use of manufacturing executions systems (MESs) and plant data repositories (Historians) reduced the challenge of maintaining effective control of production from afar. So what’s going to happen at firms that weren’t so well prepared at the outset? Here, Sean Robinson, service leader at industrial automation provider Novotek UK and Ireland, explains why modern plant systems should be part of a competitive toolkit even when there is no pandemic.
50 years ago, the thought that a plant manager could stay home and be able to have meaningful oversight of operations, while collaborating with other remote colleagues on the details, was unbelievable. If COVID-19 had struck at that time, most factories would have simply closed entirely.
Today, instead, with the right industrial IT solutions, plant management — along with team supervisors, quality leaders, engineers and continuous improvement managers — can work as a team as if they were together, regardless of where they are. A combination of developments in IT and OT have come together to make this possible.
There are now ways to securely deliver existing automation software applications such as SCADA via the web. Likewise, plant data repositories, or Historian software, have had the speed and power of their collection and storage capabilities supplemented with modern, web-based tools for exploring data. This includes ways to quickly add context and description to otherwise technical data points, so there can now be one source of raw truth that is accessible from anywhere, comprehensible by anyone.
Full-fledged production tracking systems or MESs have similarly had rich web-based front ends built, so that the detailed flow of events and activities can be tapped into from anywhere, regardless of how those systems may have had to be tied to on-site automation and sensors
The driving force behind the evolution of plant tech, though, was to enable greater productivity. With information from core operations readily at hand, alongside information from the broader enterprise, leading firms began to accelerate their continuous improvement efforts, undertake deeper collaboration with suppliers and other industrial partners and develop better insights into how to refine products and processes. The fact that their modern systems lent themselves to remote work and collaboration would come to be seen as a bonus aspect to these capabilities.
Despite the ready availability of modern plant IT and automation, and the numerous documented cases of manufacturers realising the benefits of modern systems, many factories remain wedded to paper, spreadsheets and ad-hoc/as-able machine data analysis efforts (often based on manual extraction and collation of data from individual assets). The implications of this go beyond it being comparatively inconvenient to deal with remote working.
Firms that have incorporated more modern plant solutions already enjoy significant advantages in their cost of production, their operational flexibility and their predictability in relation to meeting demand. The question is whether such current advantages will be further entrenched, or whether we will see a surge of investment from others to take on these capabilities. There is also a question of whether the firms catching up will look to go beyond simply sustaining their operations and towards fine-tuning or even re-shaping them.
Lessons from leading organisations
The next wave of technology adopters can benefit from observing how organisational structures and behaviours have been changed as modernisation has unfolded. New tech has certainly changed the way line-side operators stage, execute and manage production. However, the freer flow of data to different stakeholders has also seen improvement in surrounding business processes such as supply chain coordination and product design.
One of the cultural changes common in leading firms is broad recognition that detailed operational data supports the work of many stakeholders traditionally seen as removed from the production process. This has prompted the formation of cross-functional teams responsible for ongoing learning about the continuing evolution of automation and software.
Tasked with spotting developments that could yield outsize impact, not just sustain incremental gains in capability, cross-functional teams embody the recognition that technology is not only a critical tool to enable existing strategies, but potentially the key to new ones. That behavioural change also means that tech adoption is no longer intimidating or mysterious. With IT, operations, product design, engineering and quality leaders learning together, each group’s perspective and knowledge becomes part of a common understanding of how to understand the next technology wave in the context of the firm’s challenges and opportunities.
If the COVID outbreak showed how rapidly our steady work routines and supply networks can be disrupted, this is the time to see how technology can provide UK plc with increased resilience and a renewed operational vigour. It’s vital that manufacturers adopt the tools that support better insight and collaboration for the impact they can have on productivity, flexibility and even innovation. Modern plant systems should be seen as critical to success all the time, not just as a convenience during a pandemic.
Comments (0)
This post does not have any comments. Be the first to leave a comment below.
Featured Product
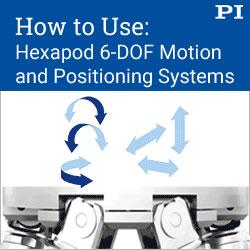