Siemens invests in new 3D-printing facility in UK
Siemens is to make a €30 million investment in a new, state-of-the-art manufacturing facility for Materials Solutions Ltd., it’s Additive Manufacturing, or 3D-printing specialist. The new building in Worcester, UK, set to open in September 2018, will more than double the company’s current footprint, enabling it to increase its fleet of 3D-printing machines to 50. The expansion is also expected to support the creation of more than 50 high quality new jobs in Worcester. This major investment is part of Siemens' plans to build and grow a global business with Additive Manufacturing services for the aerospace industry, the automotive industry and other industries. The new factory will be fully powered by Siemens Digital Enterprise solutions, an end-to-end portfolio comprising software-based systems and automation components which cover every conceivable requirement arising along the industrial value chain. It will therefore harness the potential of digitalisation.
“Additive Manufacturing is a major pillar in our digitization strategy,” said Willi Meixner, CEO of Siemens Power and Gas Division. “This significant investment underlines our belief that there is huge potential for innovation and growth within the Additive Manufacturing sector. It is also the next step towards achieving our ambition of pioneering the industrialisation of this exciting new technology and demonstrates how we are leading the way for the fourth industrial revolution,” he added. Siemens is leading not only as a user of 3D-printing but also as a supplier of software and solutions for the automation of this technology. Moreover, with Materials Solutions, the company also offers comprehensive services for engineering and printing up to the complete manufacturing of parts for external customers for example in the aviation industry, the automotive industry and motor sports.
Siemens acquired a majority stake in Materials Solutions Ltd. in 2016. The business is a pioneer in the use of Selective Laser Melting (SLM) technology for the manufacture of high-performance metal parts, with a focus on high-temperature super alloys. Materials Solutions has grown its business considerably over the last two years. It has developed proven applications, know-how and a supply chain for some of the world’s most advanced engineering companies operating in a broad range of industries. The company also works closely with Siemens’ Power & Gas Division and it is anticipated that, thanks to its expanded footprint, it will manufacture thousands of parts for use in Siemens power generation equipment over the coming years.
Siemens AG (Berlin and Munich) is a global technology powerhouse that has stood for engineering excellence, innovation, quality, reliability and internationality for 170 years. The company is active around the globe, focusing on the areas of electrification, automation and digitalization. One of the world's largest producers of energy-efficient, resource-saving technologies, Siemens is a leading supplier of efficient power generation and power transmission solutions and a pioneer in infrastructure solutions as well as automation, drive and software solutions for industry. With its publicly listed subsidiary Siemens Healthineers AG, the company is also a leading provider of medical imaging equipment – such as computed tomography and magnetic resonance imaging systems – and a leader in laboratory diagnostics as well as clinical IT. In fiscal 2017, which ended on September 30, 2017, Siemens generated revenue of €83.0 billion and net income of €6.2 billion. At the end of September 2017, the company had around 377,000 employees worldwide. Further information is available on the Internet at www.siemens.com.
Comments (0)
This post does not have any comments. Be the first to leave a comment below.
Featured Product
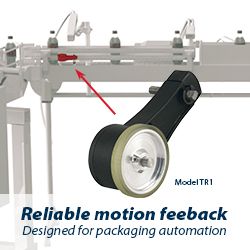