Desktop Metal gets $115 million investment in 3D printing technology
Andy Rosen for The Boston Globe: Desktop Metal, the Burlington-based maker of 3D metal printing devices, announced Monday morning that it had brought in $115 million in new investment — its largest round to date and one of the region’s most significant this year.
The company said the amount represents the largest private haul for any 3D printing company focused on metal. Desktop Metal has now raised $212 million since its launch in 2015.
“The continued support of our investors underscores the power of our metal 3D printing solutions to help engineers and manufacturers, for the first time, apply metal 3D printing for the entire product development lifecycle — from prototyping to cost effectively mass producing complex metal parts,” chief executive Ric Fulop said in a statement.
The investment follows the April launch of two products by Desktop Metal. Full Article:
Comments (0)
This post does not have any comments. Be the first to leave a comment below.
Featured Product
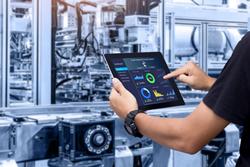