MakerBot says its new print process reduces times and costs by around 30 percent
Brian Heater for TechCrunch: MakerBot’s MinFill arrived quietly last night as a firmware upgrade for existing customers, and the company is already calling it a “big benchmark in speed and widespread adoption of 3D printing.” Many are understandably a bit cautious around such grandiose proclamations from players in this space, particularly when it comes to something as unabashedly unsexy as infill — the support structures inside a model that keep it from collapsing.
At a bare minimum, however, the newly released MinFill setting boasts some potentially impressive numbers. The technology, designed in-house for the company’s Print software, runs an algorithm that determines the minimal amount of material required to create sufficient infill for a model, saving on material and print costs — both major sticking points in the technology’s adoption.
“You can imagine as you print a complex shape, you get a lot of interesting internal geometries that support the shape in the right places,” the company’s VP of Engineering Dave Veisz tells TechCrunch. “The net effect is that it’s going to reduce the amount of filament used and reduce the print time. So, you’re printing less to get your finished product.” Full Article:
Comments (0)
This post does not have any comments. Be the first to leave a comment below.
Featured Product
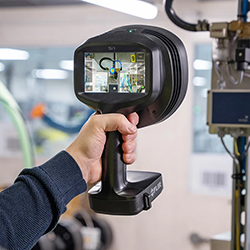