Driving proactive decisions: How digitalization improves pharmaceutical manufacturers’ new and existing facility performance
Jeff Zacherl PE, CEM, LEED AP | Industrial Vertical Market Lead - Pharma/Life Science @ Siemens
Pharmaceutical companies have only begun to scratch the surface when it comes to exploiting the benefits of digital technology. According to McKinsey, compared to other key industries, the pharmaceutical industry trails digital maturity leaders by a factor of two to three in the critical dimensions of strategy, culture, organization, and capabilities.
Within the pharmaceutical manufacturing community, companies operate at diverse levels of digitalization maturity. For some, the journey begins as they transform from manual to more automated processes. For many others, the challenge consists of capturing additional operational data and linking that data for better analysis and accurate decisions.
Whatever journey companies are on, there are benefits to becoming more digitally mature. The benefits include higher process reliability, real-time reporting, enhanced data visibility, and improved sustainability. Such improvements contribute to the business goals of faster time-to-market, greater product security, achievement of higher environmental expectations, and less complex regulatory compliance processes.
Emerging digital technologies are helping to facilitate more agile approaches required to discover, develop, and deliver new drugs. However, examining the multitude of digital options available today can be daunting, and the risk of encountering a costly deployment learning curve can be high.
A foundation for digitalization payback success
The fundamental building blocks that pave the way for organizations to enjoy the biggest payback from long-term digitalization investments include:
Instrumentation of lab facility assets- Enables the gathering of more precise operational data.
A common database - Provides one centralized source of truth, simplifying decision-making.
Connectivity to the cloud - Allows organizations to transform from reactive decision-making to a more predictive mindset through better data access and automated analysis.
Ecosystem flexibility - Open digital platforms with packaged capabilities enable easy reuse and simpler targeting of specific business needs.
Integrated platforms such as Siemens Building X link these pillars and maximize the ability of an organization to collect, analyze and monetize their data. Below are examples of how optimizing digital assets using Building X can help pharmaceutical manufacturers improve product quality and operational visibility.
How digital technologies protect product quality
Most pharmaceutical laboratories rely on ventilation, cooling, environmental controls, and pressurization systems to safely manage their operations. These are areas where digitalization can provide significant efficiency improvements, avoidance of deviation from regulatory standards, and lower product losses.
Manufacturing sites require precise environmental control to maintain product purity and avoid defects that can lead to recalls and litigation.
For instance, when freezers operate out of range, excursions will occur, which require a rapid response to correct. Consider an operation with 300 such freezers in a facility. If the environment operates out of the approved temperature range for more than a safe length of time, millions of dollars in losses are possible.
Digital platforms like Siemens Building X can lower such risks. As a suite of AI-enabled and open-platform applications, Building X provides a seamless user experience and enables third-party integration through open APIs. Users apply analytics to gain operational insights, identify efficiencies, and make faster data-driven decisions.
Benefits include:
Capturing more data - As lab managers equip system components with sensors, Building X can use the generated data to populate databases and drive AI engines. As more sensors are added and more data is gathered, they help accelerate the AI learning curves enabling the outcomes to become far more precise.
Predictive analysis - Besides internal databases, Building X can also gather data from external sources (such as weather forecasts) to help drive safer and more precise temperature and humidity control in selected facility spaces. For instance, weather data can help when analysts model the behavior of the facility over previous years to identify environmental trends. This helps operators to anticipate and identify anomalies and potential issues before they result in any undesired fluctuation of internal environmental conditions. As a cloud-based platform, Building X can link disparate data models and apply those to machine learning or AI for tighter environmental control and lower the risk of product loss.
Centralizing data - Digital platforms such as Building X can accept different data streams that are not normally combined and bring those data sources into a common data model. Although devices such as HVAC equipment may operate using disparate protocols, Building X, an open system, communicates through various industry standard protocols, or utilizes a custom API, regardless of equipment type or vendor brand. This provides facility operators with a more holistic process view and enhances their ability to drive proactively as opposed to reactive decisions.
Real-world example: How digital enhances environmental visibility
In addition to the technology solutions provided by portfolios like Siemens Building X, pharmaceutical manufacturers are benefiting from centralized digital platforms in several ways. One US-based operation — a biopharma testing company with hundreds of labs operating across the globe that perform millions of tests per year — experienced unpredictable behavior of their building infrastructure systems. Unanticipated temperature fluctuations were disrupting test process accuracy.
To address the issue, the company decided to pilot Building X in one of their 35,000 sq ft testing facilities. The system provided operators with enhanced visibility to HVAC systems and critical spaces, and they gained the ability for remote command and control. Since the use of Building X significantly reduced instances of out-of-band temperatures, the organization decided to expand deployment to over 200 sites using the platform's operations manager, fire manager, critical environment monitoring, and sustainability manager tools.
Thanks to the digitalization of their testing operations, stakeholders can meet aggressive sustainability goals, experience more reliable operations, execute real-time operational control and reporting, and enhance operational visibility.
Integrating digitalization with new facilities
Besides digitalizing older facilities that require modernization, integrating digitalization with new facility design and construction has an even bigger impact on achieving corporate profitability and compliance goals.
Experienced companies like Siemens help support new-build digitalization in numerous ways:
Digital twin for design - These exceptionally powerful software tools create a digital model of tomorrow's pharmaceutical lab. By running the digital twin through its processes and paces, stakeholders can determine how to best operate the new facility and its environmental systems and accurately predict environmental fluctuations, carbon footprint, and energy consumption - before construction crews ever build the facility. In this way, engineers can design facilities that meet long-term safe production targets. An ISO 19650-certified solution like Siemens Building X Lifecycle Twin, creates an interactive digital twin of any BIM-planned building, enabling informed decision-making throughout the building lifecycle.
ESCO arrangements for financing - To allow the capital upgrades needed that might otherwise be unfeasible, many organizations partner with Siemens in an Energy Services Conservation (ESCO) financing arrangement. Funding assists in the acquisition of smart infrastructure investments. The resulting energy savings fund payments for technology and services, so stakeholders require no large upfront fees.
Building a connected model for optimized operations - Siemens experts can help identify low-cost technology deployment opportunities, provide the elements required for building a connected model around collecting and analyzing data, and help set KPIs to drive safety and performance improvement.
For more information
Siemens supports digitalization efforts across the pharmaceutical industry. By providing robust cloud-based platforms like Building X and advanced software simulation tools, Siemens helps stakeholders to better plan and implement modern technology infrastructures. If you're attending Hannover Messe, March 31-April 4, you'll get the chance to see a live demo of Building X and how we are empowering digital transformation in the Pharma & Life Science industry at the Siemens booth in hall 9. Can't wait until then? Send me a request on LinkedIn to connect!
Featured Product
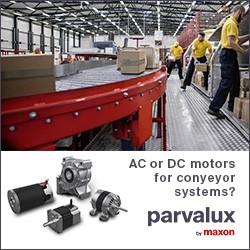
Parvalux by maxon - AC or DC electric motors for conveyor systems?
The material handling industry uses conveyors to ensure that products are distributed effectively, AC or DC motors are chosen depending on the weight it needs to carry and the speed at which it needs to work. Learn which type of conveyor motor might be best for your application and how Parvalux can help you select a geared motor from stock or create a fully custom design.