The Booming 3D Printing Materials Market: Poised to Surpass USD 5.06 Billion by 2032
Over the years, advancements in 3D printing materials have fueled innovation, allowing manufacturers to explore new possibilities in aerospace, healthcare, automotive, and consumer goods. With the market set to exceed USD 5.06 billion by 2032, the demand for high-performance and sustainable materials is rising rapidly.
3D printing has revolutionized modern manufacturing, paving the way for cost-effective and highly customizable production methods across industries. Over the years, advancements in 3D printing materials have fueled innovation, allowing manufacturers to explore new possibilities in aerospace, healthcare, automotive, and consumer goods. With the market set to exceed USD 5.06 billion by 2032, the demand for high-performance and sustainable materials is rising rapidly.
Key Growth Drivers of the 3D Printing Materials Market
1. Expanding Applications Across Industries
The increasing adoption of 3D printing in various industries has been a crucial factor driving the demand for specialized materials. In the healthcare sector, biocompatible polymers and resins are being used for prosthetics, implants, and dental restorations. The aerospace industry relies on high-performance thermoplastics and metal powders to produce lightweight yet durable components, reducing production costs and improving fuel efficiency.
2. Advancements in Material Science
The development of new 3D printing materials with enhanced mechanical, thermal, and chemical properties is transforming the industry. Innovations such as carbon fiber-reinforced polymers, biodegradable resins, and conductive filaments are expanding the range of applications. Additionally, metal 3D printing materials, including titanium, aluminum, and stainless steel, are increasingly being used in precision engineering.
3. Growing Demand for Sustainable Materials
Sustainability is a key trend influencing the 3D printing materials market. Manufacturers are focusing on eco-friendly alternatives such as bio-based polymers and recycled filaments. These materials not only reduce environmental impact but also align with global initiatives aimed at minimizing plastic waste and carbon emissions.
4. Rise in Customization and Personalization
The ability to create customized products with intricate designs is another driving force behind the growth of 3D printing materials. Industries such as fashion, jewelry, and consumer electronics are leveraging 3D printing to develop personalized items with unique aesthetics and functionalities. This shift is fostering innovation in material formulation to meet the demands of complex geometries and high-resolution prints.
Market Segmentation: Analyzing Key Material Types
The 3D printing materials market is categorized into various material types, each serving distinct applications:
1. Polymers
Polymers dominate the market, accounting for a significant share due to their versatility and affordability. Common polymer-based materials include:
• PLA (Polylactic Acid): A biodegradable and easy-to-use material ideal for prototyping.
• ABS (Acrylonitrile Butadiene Styrene): Known for its durability and impact resistance.
• Nylon: Used in functional prototyping and end-use applications due to its flexibility and strength.
2. Metals
Metal-based 3D printing materials are gaining traction in industries requiring high strength-to-weight ratios. Key metals include:
• Titanium: Widely used in aerospace and medical applications for its excellent strength and corrosion resistance.
• Stainless Steel: Ideal for industrial applications where durability is critical.
• Aluminum: Preferred for automotive and lightweight engineering solutions.
3. Ceramics
Ceramic-based materials are increasingly being used for applications requiring high heat resistance and superior aesthetics. Industries such as dentistry and electronics are driving demand for ceramic 3D printing materials.
4. Composites
Composite materials, including carbon fiber-reinforced filaments and graphene-infused polymers, are emerging as high-performance alternatives for advanced manufacturing. These materials offer improved strength, conductivity, and lightweight properties, making them suitable for high-end industrial applications.
Regional Insights: Global Market Expansion
1. North America: A Hub for Innovation
North America remains a dominant player in the 3D printing materials market, driven by significant investments in research and development. The presence of key market players and a strong emphasis on technological advancements contribute to the region's growth.
2. Europe: Advancing Sustainability in 3D Printing
Europe is witnessing a surge in demand for sustainable 3D printing materials, supported by government initiatives and regulatory frameworks promoting eco-friendly manufacturing. Countries like Germany, the UK, and France are at the forefront of material innovations.
3. Asia-Pacific: Rapid Industrialization and Adoption
The Asia-Pacific region is experiencing rapid market expansion due to the growing adoption of 3D printing in manufacturing, healthcare, and automotive sectors. Countries like China, Japan, and South Korea are investing heavily in additive manufacturing technologies.
Challenges and Opportunities in the Market
1. High Material Costs
Despite the potential of 3D printing materials, high costs remain a barrier to widespread adoption. Developing cost-effective alternatives and optimizing production processes are crucial for market growth.
2. Standardization and Quality Control
Ensuring consistent quality across different 3D printing materials is a challenge. Industry standards and certifications are necessary to enhance reliability and performance.
3. Emerging Opportunities in Bioprinting and Electronics
The integration of 3D printing in bioprinting and electronics manufacturing presents lucrative opportunities. Researchers are exploring bio-inks for tissue engineering and conductive materials for printed electronics, paving the way for groundbreaking applications.
With technological advancements, increasing demand for sustainability, and expanding industrial applications, the 3D printing materials market is on a trajectory toward significant growth, reshaping the future of manufacturing.
Source: https://www.gminsights.com/industry-analysis/3D-printing-materials-market
Featured Product
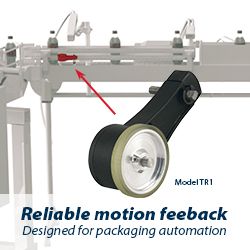