Semiconductor Manufacturing: The Six Essential Steps Behind Every Chip
The semiconductor industry is often considered the backbone of the modern technological landscape. From the devices we carry in our pockets to the machinery that powers industries, semiconductors are essential. However, many of us take for granted the complex and intricate process that goes into manufacturing these tiny yet powerful components.
What Are Semiconductors?
6 Essential Steps in Semiconductor Manufacturing
1. Wafer Production
The very first step in semiconductor manufacturing is to create a silicon wafer. Silicon, a widely available material, is chosen due to its excellent semiconducting properties. The process begins with obtaining silicon dioxide (SiO2) from natural sources like sand. Here's how it's processed:
• Purification: The silicon is extracted and purified to a high degree, creating a material called polycrystalline silicon.
• Crystal Growth: The purified silicon is then melted and crystallized into long cylindrical ingots using a method known as the Czochralski process. These ingots are cooled and sliced into thin wafers with a diamond saw. The wafer is then polished to a mirror-like finish to remove any imperfections that could affect the subsequent processes.
• The result is a thin, circular silicon wafer, typically 200mm or 300mm in diameter, which will serve as the foundation for the microelectronic components.
2. Photolithography
Photolithography is one of the most critical processes in semiconductor manufacturing, where the intricate circuit patterns are transferred onto the wafer. The process involves several stages:
• Coating: The wafer is first coated with a thin layer of a photoresist material, which is sensitive to ultraviolet (UV) light.
• Mask Alignment: A photomask, which contains the detailed circuit design of the chip, is placed over the wafer. This mask will block or allow UV light in specific areas to create the desired pattern.
• Exposure: The wafer is then exposed to UV light. Where the UV light hits the photoresist, it chemically reacts to make the material either more or less soluble in a developer solution (depending on whether a positive or negative resist is used).
• Development: After exposure, the wafer is immersed in a developer solution, which washes away the exposed or unexposed areas, depending on the type of photoresist used. This leaves behind a pattern that corresponds to the circuit design.
This process is repeated multiple times with different photomasks for each layer of the semiconductor, building up a complex pattern of transistors, interconnections, and other components on the wafer's surface.
3. Etching
Once the pattern has been developed on the photoresist layer, the next step is etching, which involves removing material from the wafer's surface to define the desired structure.
• Etching Methods: There are two primary etching techniques:
o Wet Etching: The wafer is immersed in a chemical solution that removes specific layers from the surface.
o Dry Etching (Plasma Etching): A more advanced and precise method, dry etching uses plasma (ionized gas) to etch away material. The plasma is created by applying an electric field to gases like chlorine or fluorine, which react with the wafer material to etch away the unwanted areas.
• Selective Removal: Etching selectively removes the material in areas where the photoresist has been cleared, leaving behind the desired pattern. This process helps to create narrow trenches, vias, and other essential features that form the microstructure of the semiconductor device.
4. Doping (Ion Implantation)
The next critical step is doping, where the electrical properties of the semiconductor are modified by adding impurities, known as dopants, into specific regions of the silicon wafer.
• Ion Implantation: Doping is usually achieved by ion implantation, in which ions of elements like boron (for p-type doping) or phosphorus (for n-type doping) are accelerated and shot into the wafer. The process alters the electrical properties of the silicon, creating regions where the flow of electricity is either enhanced or suppressed.
• Controlled Doping: By carefully controlling the amount and location of doping, specific regions of the wafer can be made either more positively charged (p-type) or more negatively charged (n-type). These regions form the essential building blocks of transistors—the tiny switches that control the flow of electricity.
This step is essential for creating the p-n junctions that are central to transistor operation, and ultimately, the functioning of the microchips.
5. Deposition
Deposition is the process of adding thin layers of various materials onto the wafer to create the different components of the microchip. There are two major deposition methods used in semiconductor manufacturing:
• Chemical Vapor Deposition (CVD): In this method, gases are introduced into a reaction chamber where they chemically react to form solid thin layers of material on the wafer surface. Common materials deposited via CVD include silicon dioxide (SiO2) and polysilicon.
• Physical Vapor Deposition (PVD): In PVD, materials are vaporized using heat or a plasma source and then deposited onto the wafer as thin films. This process is often used to deposit metal layers, such as copper, for interconnecting different parts of the semiconductor.
• Atomic Layer Deposition (ALD): This is an advanced method that deposits extremely thin, highly uniform layers, typically for insulating or gate dielectrics in advanced chips.
Deposition is essential for building up the different layers of the device, such as insulating layers, conductive layers, and gate materials, which are needed to form the transistors and the interconnections between them.
6. Testing and Packaging
Once the wafer has gone through multiple layers of photolithography, etching, doping, and deposition, the individual chips need to be tested, separated, and packaged:
• Wafer Testing: The wafer is first tested for functionality using a process known as probe testing, where small electrical probes are used to check if the transistors are working correctly. This helps identify defective chips that will be discarded.
• Dicing: The wafer is then diced into individual chips (also called dies). This is done using a diamond-tipped saw or a laser.
• Packaging: The individual chips are then packaged into protective casings that allow them to be integrated into electronic devices. This packaging process involves connecting the chip to external leads or pins through tiny wires (using wire bonding) and encapsulating the chip in a protective package.
Semiconductor Manufacturing Industry Overview
The semiconductor manufacturing market is poised for significant growth, with the market size expected to reach USD 278.44 billion in 2024 and projected to expand to USD 762.58 billion by 2034, reflecting a compound annual growth rate (CAGR) of 10.6% from 2023 to 2034. This growth is driven by the increasing demand for advanced semiconductor devices across industries like electronics, automotive, telecommunications, and artificial intelligence, as well as the rise of emerging technologies such as 5G, autonomous vehicles, and IoT. As technology continues to evolve, the need for faster, more efficient, and energy-saving semiconductor solutions will further fuel the market's expansion.
Get More Details Here
Key Technologies in Semiconductor Manufacturing
• Extreme Ultraviolet Lithography (EUV): Used for creating the smallest possible transistors, EUV enables the production of chips with smaller nodes, such as 5nm or 3nm, which are critical for improving performance and reducing power consumption.
• 3D Integration: Involves stacking multiple layers of circuits on top of each other to improve performance and reduce the physical footprint of chips.
• Quantum Dot Technology: Explores the use of quantum properties to improve the efficiency and capabilities of semiconductors.
The Importance of Semiconductor Manufacturing
The world's shift toward digitalization, artificial intelligence (AI), autonomous vehicles, and the Internet of Things (IoT) has made semiconductors more critical than ever. Microchips embedded in everything from smartphones to medical devices are powered by semiconductors.
What makes semiconductor manufacturing so important is its role in driving technological advancement. With the demand for faster, more powerful, and energy-efficient devices on the rise, the innovation of new semiconductor technologies will determine the future of industries such as telecommunications, computing, healthcare, and automotive.
Applications of Semiconductor Devices
• Consumer Electronics: Smartphones, laptops, TVs, tablets, gaming consoles.
• Automotive Industry: Autonomous driving systems, electric vehicles, infotainment systems.
• Industrial Automation: Robotics, industrial IoT (Internet of Things), machine learning systems.
• Healthcare: Medical devices, imaging systems, and diagnostics.
• Telecommunications: Network equipment, data centers, 5G technology.
The Challenges of Semiconductor Manufacturing
Despite its immense importance, semiconductor manufacturing is fraught with challenges. One of the most pressing challenges is the physical limitations of the materials themselves. As semiconductor technology advances, the size of transistors shrinks, and there's a limit to how small these transistors can get before quantum effects interfere with their function.
Another challenge is the growing complexity of designs. With the advent of technologies like 5G, AI, and autonomous systems, semiconductor chips have become incredibly complex, requiring more precision and increasingly advanced fabrication techniques. Manufacturers are continually pushing the boundaries of innovation to ensure that these devices can keep up with rapidly evolving demands.
Moreover, the global supply chain for semiconductors has been disrupted by geopolitical tensions and trade policies. A single disruption in the supply chain can have ripple effects across industries, affecting everything from smartphones to automotive manufacturing. This has made it clear how critical it is to ensure a resilient and diversified semiconductor manufacturing process.
The Future of Semiconductor Manufacturing
As the world becomes more interconnected and reliant on technology, the future of semiconductor manufacturing looks incredibly bright. We are already seeing advancements in semiconductor technology, such as the move toward smaller nodes (3nm and 2nm processes), quantum computing, and advanced packaging techniques that allow for more powerful and efficient chips.
There is also a shift toward sustainable practices in semiconductor manufacturing, as the industry works to reduce energy consumption and waste. The development of new materials, such as gallium nitride (GaN) and silicon carbide (SiC), may revolutionize industries such as power electronics and renewable energy by enabling more efficient energy conversion and storage.
Finally, semiconductor manufacturing is expected to become increasingly localized as nations seek to reduce dependence on foreign production. This could lead to the growth of semiconductor manufacturing hubs outside traditional areas like Taiwan and South Korea.
𝐀𝐛𝐨𝐮𝐭 𝐔𝐬:
Statifacts is a leading provider of comprehensive market research and analytics services, offering over 1,000,000 market and customer data sets across various industries. Their platform enables businesses to make informed strategic decisions by providing full access to statistics, downloadable in formats such as XLS, PDF, and PNG.
Connect with Us at sales@statifacts.com
Featured Product
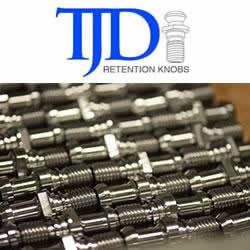
T.J. Davies' Retention Knobs
Our retention knobs are manufactured above international standards or to machine builder specifications. Retention knobs are manufactured utilizing AMS-6274/AISI-8620 alloy steel drawn in the United States. Threads are single-pointed on our lathes while manufacturing all other retention knob features to ensure high concentricity. Our process ensures that our threads are balanced (lead in/lead out at 180 degrees.) Each retention knob is carburized (hardened) to 58-62HRC, and case depth is .020-.030. Core hardness 40HRC. Each retention knob is coated utilizing a hot black oxide coating to military specifications. Our retention knobs are 100% covered in black oxide to prevent rust. All retention knob surfaces (not just mating surfaces) have a precision finish of 32 RMA micro or better: ISO grade 6N. Each retention knob is magnetic particle tested and tested at 2.5 times the pulling force of the drawbar. Certifications are maintained for each step in the manufacturing process for traceability.