AM Solutions presents first results of the collaboration with EOS at Formnext 2024
Last year, EOS and AM Solutions - 3D post processing technology entered into a partnership with the aim of optimizing the process chain in the field of SLS printing. The first joint developments are now in the starting blocks.
Last year, EOS and AM Solutions - 3D post processing technology entered into a partnership with the aim of optimizing the process chain in the field of SLS printing. The first joint developments are now in the starting blocks.
EOS, one of the leading technology providers for industrial 3D printing, and AM Solutions - 3D post processing technology, a proven expert in industrial post-processing solutions, have a common goal: to advance the additive manufacturing process chain in the SLS sector and pave the way for series production. To achieve this, the two companies are combining their expertise and have been developing solutions to automate post-processing and increase cost efficiency since last year.
"We have been working together intensively over the past year and have already made great progress," explains David Soldan, Head of AM Solutions - 3D post processing technology. He is referring to two machine concepts that are being developed specifically, but not exclusively, for the new generation of EOS P3 NEXT polymer printers.
Two innovative post-processing solutions for greater efficiency
In addition to an unpacking solution that automatically, economically and reproducibly depowders parts and minimizes powder contact for the operator, an innovative 2-in-1 solution will be available that screens and mixes the powder. This system combines both process steps in a single machine to save space and costs. It employs a unique process to create a high-quality mixture of used and new powder. The mixing ratio can be tailored to specific needs, and it is capable of producing small batches. The first printing results from EOS have been very promising.
Both companies express their satisfaction with the current project status. "The collaboration with EOS is extremely constructive and based on partnership. In our view, the two machine solutions will prove to be real game changers," says David Soldan. Fabian Krauß, Head of Product Management Polymer Solutions at EOS adds: "AM Solutions' technology is a perfect complement to the EOS P3 NEXT. As a result of this collaboration, our customers will have an end-to-end production solution that streamlines their production workflow and allows them to grow at their own pace."
Debut at this year's Formnext
The current development status and further information will be presented to interested trade visitors for the first time at Formnext 2024 at the AM Solutions booth in Hall 11.1, booth E41. Directly across at booth D41, EOS will present the associated printer solution for the first time in the form of the new EOS P3 NEXT system.
Rösler Oberflächentechnik GmbH / AM Solutions
For over 80 years, the privately owned Rösler Oberflächentechnik GmbH has been actively engaged in the field of surface preparation and surface finishing. As global market leader, we offer a comprehensive portfolio of equipment, consumables and services around the mass finishing and shot blasting technologies for a wide spectrum of different industries. Our range of about 15,000 consumables, developed in our Customer Experience Centers and laboratories located all over the world, specifically serves our customers for resolving their individual finishing needs. Under the brand name AM Solutions, we offer numerous equipment solutions and services in the area of additive manufacturing/3D printing. Last-but-not-least, as our central training center the Rösler Academy offers practical, hands-on seminars to the subjects mass finishing, shot blasting and additive manufacturing. The Rösler group has a global network of 15 locations and approx. 150 sales agents.
For more information, please go to: www.rosler.com / www.solutions-for-am.com
Featured Product
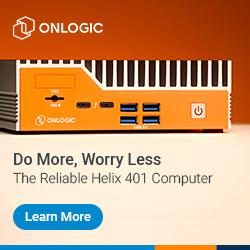
OnLogic's Helix 401 Compact Fanless Computer
OnLogic's Helix 401 Compact Fanless Computer offers scalable, high-performance processing and can simultaneously drive multiple 4K displays, making it the ideal computing platform for many automation and IIoT applications. The Helix 401 has the horsepower to drive mission-critical applications while requiring less than 28W of power, and is small enough to fit in space-constrained locations or enclosures. It can be configured with a range of Intel® 12th generation processors, up to a Core i7 and has Intel Iris® Xe graphics onboard.