CNC development history and processing principles
From the meshing of mechanical gears to the flow of digital signals, CNC technology has rewritten the underlying logic of the manufacturing industry in 70 years. It is not only an upgrade of machine tools, but also a leap in the ability of humans to transform abstract thinking into physical entities.
CNC ma
chine tools are also called Computerized Numerical Control (CNC for short). They are mechatronics products that use digital information to control machine tools. They record the relative position between the tool and the workpiece, the start and stop of the machine tool, the spindle speed change, the workpiece loosening and clamping, the tool selection, the start and stop of the cooling pump and other operations and sequence actions on the control medium with digital codes, and then send the digital information to the CNC device or computer, which will decode and calculate, issue instructions to control the machine tool servo system or other actuators, so that the machine tool can process the required workpiece.1. The evolution of CNC technology: from mechanical gears to digital codesThe Beginning of Mechanical Control (late 19th century - 1940s)The prototype of CNC technology can be traced back to the invention of mechanical automatic machine tools in the 19th century. In 1887, the cam-controlled lathe invented by American engineer Herman realized "programmed" processing for the first time by rotating cams to drive tool movement. Although this mechanical programming method is inefficient, it provides a key idea for subsequent CNC technology. During World War II, the surge in demand for military equipment accelerated the innovation of processing technology, but the processing capacity of traditional machine tools for complex parts had reached a bottleneck.The electronic revolution (1950s-1970s)After World War II, manufacturing industries mostly relied on manual operations. After workers understood the drawings, they manually operated machine tools to process parts. This way of producing products was costly, inefficient, and the quality was not guaranteed. In 1952, John Parsons' team at the Massachusetts Institute of Technology (MIT) developed the world's first CNC milling machine, which input instructions through punched paper tape, marking the official birth of CNC technology. The core breakthrough of this stage was "digital signals replacing mechanical transmission" - servo motors replaced gears and connecting rods, and code instructions replaced manual adjustments. In the 1960s, the popularity of integrated circuits reduced the size and cost of CNC systems. Japanese companies such as Fanuc launched commercial CNC equipment, and the automotive and aviation industries took the lead in introducing CNC production lines. Integration of computer technology (1980s-2000s)With the maturity of microprocessor and graphical interface technology, CNC entered the PC control era. In 1982, Siemens of Germany launched the first microprocessor-based CNC system Sinumerik 800, whose programming efficiency was 100 times higher than that of paper tape. The integration of CAD (computer-aided design) and CAM (computer-aided manufacturing) software allows engineers to directly convert 3D models into machining codes, and the machining accuracy of complex surfaces reaches the micron level. During this period, equipment such as five-axis linkage machining centers came into being, promoting the rapid development of mold manufacturing and medical device industries.Intelligence and networking (21st century to present)The Internet of Things and artificial intelligence technologies have given CNC machine tools new vitality. Modern CNC systems use sensors to monitor parameters such as cutting force and temperature in real time, and use machine learning to optimize processing paths. For example, the iSMART Factory solution of Japan's Mazak Company achieves intelligent scheduling of hundreds of machine tools through cloud collaboration. In 2023, the global CNC machine tool market size has exceeded US$80 billion, and China has become the largest manufacturing country with a production share of 31%.2. CNC machining principles: How code drives steelThe essence of CNC technology is to convert the physical machining process into a control closed loop of digital signals. Its operation logic can be divided into three stages:Geometric Modeling and ProgrammingAfter building a 3D model using CAD software such as UG and SolidWorks, CAM software "deconstructs" the model: automatically calculating parameters such as tool path, feed rate, spindle speed, and generating G code (such as G01 X100 Y200 F500 for linear interpolation to coordinates (100,200) and feed rate 500mm/min). Modern software can even simulate the material removal process and predict machining errors.Numerical control system analysis and implementationThe "brain" of CNC machine tools - the numerical control system (such as Fanuc 30i, Siemens 840D) converts G codes into electrical pulse signals. Taking a three-axis milling machine as an example, the servo motors of the X/Y/Z axes receive pulse commands and convert rotary motion into linear displacement through ball screws, with a positioning accuracy of up to ±0.002mm. The closed-loop control system uses a grating ruler to feedback position errors in real time, forming a dynamic correction mechanism.Multi-physics collaborative controlDuring the machining process, the machine tool needs to coordinate multiple parameters synchronously: the spindle motor drives the tool to rotate at a high speed of 20,000 rpm, the cooling system sprays atomized cutting fluid to reduce the temperature, and the tool changing robot completes the tool change within 0.5 seconds. For example, when machining titanium alloy blades, the system needs to dynamically adjust the cutting depth according to the hardness of the material to avoid tool chipping.3. The future of CNC technology: cross-dimensional breakthroughs and industrial transformationCurrently, CNC technology is facing three major trends:Combined: Turning and milling machine tools can complete turning, milling, grinding and other processes on one device, reducing clamping time by 90%;Additive-subtractive integration: Germany's DMG MORI's LASERTEC series machine tools combine 3D printing and CNC finishing to directly manufacture aerospace engine combustion chambers;Digital Twin: By using a virtual machine tool to simulate the actual machining process, China's Shenyang Machine Tool's i5 system has increased debugging efficiency by 70%.From the meshing of mechanical gears to the flow of digital signals, CNC technology has rewritten the underlying logic of the manufacturing industry in 70 years. It is not only an upgrade of machine tools, but also a leap in the ability of humans to transform abstract thinking into physical entities. In the new track of intelligent manufacturing, CNC technology will continue to break through the limits of materials, precision and efficiency, and write a new chapter for industrial civilization.Featured Product
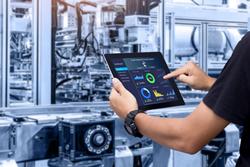
Using AI to Collect & Leverage Data
Data is the foundation of Industry 4.0. While skilled workers will always be essential, data is reshaping the manufacturing landscape, enabling automation of repetitive tasks, empowering smarter decision-making with AI assistance, and reducing defects and downtime. This shift allows small and medium-sized manufacturers (SMMs) to compete more effectively on quality, speed, and cost. While AI and machine learning systems typically require around two years to collect enough data to reach their full potential, manufacturers can start seeing benefits almost immediately with basic analysis tools and dashboards. Our MEP National NetworkTM expert explains how in this Manufacturing Tomorrow article.