voxeljet Expands HSS Network with FKM Sintertechnik as Production Partner
-voxeljet AG is expanding its high-speed sintering (HSS) network in collaboration with FKM Sintertechnik GmbH as a production partner. -Since the announcement of the cooperation in November 2023, the VX1000 HSS has undergone significant improvements. In addition to optimizing the mechanical properties of the parts, a homogeneity in part properties and quality across the entire build field has been achieved. -The VX1000 HSS at FKM meets industrial requirements for mechanical strength, homogeneity of the build field and reproducibility and is the largest ink-based polymer 3D printer on the market. -Polyamide 12 (PA12) components can now be ordered from FKM.
voxeljet AG announced the expansion of its High Speed Sintering (HSS) network with the addition of a new production partner, FKM Sintertechnik GmbH, located north of Frankfurt. As part of the beta program, the two companies are working closely together to further optimize the process parameters of the VX1000 HSS, the largest ink-based polymer 3D printer on the market. The goal is to increase the efficiency and quality of the printing process. The VX1000 HSS at FKM, one of Germany's leading 3D printing service providers, meets the requirements of industrial applications, including mechanical strength, homogeneity of the build field, and reproducibility of results.
Following the announcement of the cooperation in November 2023, the VX1000 HSS has undergone significant improvements. In addition to optimizing mechanical part specifications, there has been a successful effort to homogenize part properties and quality across the entire building platform. With a print volume of 1,000 x 540 x 180 mm (for PA12), the VX1000 HSS is one of the largest and most powerful 3D printers for polymers on the market. The powder and ink-based HSS process requires consistent and highly precise temperature management to achieve the desired part properties. The VX1000 HSS demonstrates clear advantages in terms of production speed, quality, dimensional accuracy, and unit costs, particularly in comparison to SLS systems, even for large components.
"From the outset, our collaboration with FKM was focused on optimizing the quality of components across the expansive building platform," states Dr. Alfred Grießer, Director of Research and Development at voxeljet. "FKM has been a trusted supplier to a range of industries for decades, including aerospace, automotive, and special plant engineering. By combining our development with FKM's expertise as a powder bed specialist, we have been able to ensure that our VX1000 HSS meets the high standards of these industries."
VX1000 HSS has now been successfully installed, and FKM has joined voxeljet's HSS Polymer Network as a production partner. The network operates on an interdisciplinary and collaborative basis, with the objective of generating knowledge about 3D printable materials and their sintering strategy for the HSS process, as well as qualifying new materials. Having originally concentrated on R&D, the network is now being expanded with its first production partner. This collaboration provides customers with an end-to-end solution, from materials research to parts production.
"FKM has consistently positioned itself as a leader in the introduction of advanced technologies," states Jürgen Blöcher, Managing Director of FKM Sintertechnik GmbH. "The HSS technology from voxeljet unites the benefits of two distinct approaches: the precision and productivity of SLS as well as the reproducibility and speed of binder jetting. The investment in the VX1000 HSS 3D printer allows us to further advance our proven FKM principle: to produce large components rapidly and/or numerous small components in a short time."
About voxeljet:
voxeljet is a leading provider of high-speed, large-format 3D printers and on-demand parts services to industrial and commercial customers. The Company's 3D printers employ a powder binding, additive manufacturing technology to produce parts using various material sets, which consist of particulate materials and proprietary chemical binding agents. The Company provides its 3D printers and on-demand parts services to industrial and commercial customers serving the automotive, aerospace, film and entertainment, art and architecture, engineering, and consumer product end markets.
For more information, visit our website www.voxeljet.com or follow us on YouTube, LinkedIn, Facebook and Instagram.
About FKM Sintertechnik GmbH:
FKM Sintertechnik GmbH was founded in 1994 as a development service provider and quickly developed into a specialist in the field of plastic and metal laser sintering.
The medium-sized company currently employs 60 people and is one of the leading manufacturers in the 3D printing industry. It is a development partner and supplier to numerous well-known customers in the automotive, machinery and equipment manufacturing sectors.
In 2023, FKM Sintertechnik realized a wide variety of plastic and metal components in more than 10,000 individual orders with varying batch sizes. FKM currently produces prototypes and industrial-scale series on over 50 systems.
FKM Sintertechnik's additive manufacturing is certified in accordance with IATF 16949, ISO 9001 and ISO 14001. In 2024, the company was awarded the TOP 100 award for its innovative strength.
Featured Product
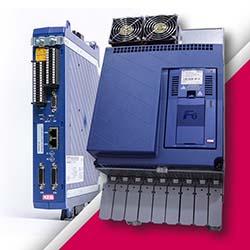