How EU manufacturers are losing ground by ignoring the urgency of modern data management
By Jeroen Coussement, CEO at Factry - With rapid technological advancements and markets demanding smaller, personalised batches and rapid changes, European production companies must be agile and adaptive. Yet, technologies unfit for data-driven operations are undermining their flexibility and competitiveness. Unless they act now, they risk becoming irrelevant.
The European production industry is undergoing a significant transformation, driven by an increasing market demand for smaller, bespoke, and a more varied range of products. This shift requires radically enhanced management capabilities, along with a more flexible supply chain. At the same time, profit margins are under pressure, governments and stakeholders are demanding greater data transparency, and promising technologies are hitting ground.
Yet, European production companies are also struggling to line up the need for agile operations with their technology stack. Legacy tools often lead to fragmented data sets and slow decision-making processes, hampering the ability to quickly and flexibly adapt to changes, or connect with emerging technologies. High employee turnover further complicates the issue, making it hard to retain and manage essential process knowledge within the company.
Delayed digital transition
As illustrated by Deloitte's 2023 Manufacturing Industry Outlook, the role of digital transformation in achieving operational excellence and improving competitiveness is undeniable. Industrial companies that fail to invest in an open, flexible data infrastructure and advanced applications such as AI and cloud analytics, are positioned a lot worse to build reconfigurable supply chains and enable real-time decision-making throughout their organisations.
Often stuck in outdated pricing models and rigid technologies that date back to the 80s, European companies are embracing modernity slowly. Many are rich on data, but poor on information. I see shift leaders write today's process parameters in a report, which the production manager then enters into a weekly Excel sheet. This is passed up to the plant manager, who includes it in KPI reports for management. It can take weeks to get actionable insights, while in a fast-moving plant environment, you actually need them right here, right now.
Retaining process knowledge
At the same time, the workforce has changed significantly. The machine operator's role has evolved into a skilled position requiring the ability to work with complex machines. Unlike in the past, you can't just quickly replace one person with another. This evolution brings new challenges, especially in retaining essential process knowledge. It has become vital for technology to support people, whether through guiding user interfaces, automatic data collection, or providing helpful context to processes.
In the future, market success for European manufacturers will not solely depend on production capabilities but also on how effectively a company handles digitalisation. Even with slightly lower product efficiency, a company with streamlined digital processes and an optimised supply chain might be able to outperform its competitors. Key factors will include a solid and accessible data foundation, self-sustainability of software tools, and the ability to integrate any future AI applications.
Avoiding irrelevance
Meanwhile, global advancements in digital transformation are accelerating. Gartner's recent report 2024 Tech Trends in Manufacturing shows that 54% of global manufacturing companies are spending 10% or more on digital technology in 2024 compared to 2023. Business Intelligence (BI) and production analytics software is a top priority for manufacturers. Their top challenges when planning investment in digital transition include identifying the right technology (47%) and compatibility with their existing systems (44%).
Most industry executives I talk to recognise the disruptive potential and are experimenting with various digital improvement initiatives, yet many find it hard to determine what initiatives to scale up and how, as they are unaware what digital success will look like five years from now. And they're absolutely right: who knows what the future brings? However, you can prepare for it today by making the right technological decisions.
Production companies often tell me: ‘We already own so much data!' But if you are not connecting and centralising data sources, not making data analysis accessible, and not extracting value from it, you're not keeping up with your competitors. Some companies don't feel an urgent need for deep data transformation at this point, thinking their current production and margins are okay. However, if they don't take serious steps towards digitalisation now, they will likely feel the impact in ten years. They risk irrelevance in their industries.
A change in mindset
Companies must think ahead, beyond current needs, and approach the rapidly changing requirements with a strategic mindset. While the specific future applications are unpredictable, data-driven operations are a certainty. By laying a robust data foundation today, companies can later easily integrate subsequent use cases and applications, such as AI. Open technologies are crucial in this journey because they are ready to adapt to the unknown future. I've seen over and over how frictionless access to data sparks the creativity of people and uncovers problem-solving skills. Once you enable people to easily visualise data in dashboards, they start exploring solutions for their day-to-day issues. Often, magic will happen.
Can EU companies still recover?
By replacing outdated technologies with open technologies, companies can build the necessary data foundation to thrive in an uncertain future, foster an open data culture to continuously improve, and offer the data transparency stakeholders increasingly demand. It's not too late yet for European production companies to get their act together. By acknowledging the need for a robust data foundation and infrastructure, and by adopting open technologies that can integrate with any future application, the European industry can still protect its long term market sustainability. However, taking control over its production data is crucial for tomorrow's manufacturing success.
Featured Product
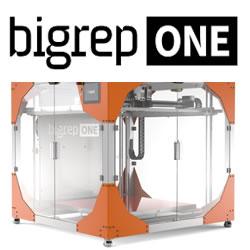