What's The Differences Between SLA and SLS in Rapid Prototyping?
Rapid Prototyping(RP) is a manufacturing technology that quickly generates models or parts. There are more than ten different processes, such as stereolithography (SLA), laminated object manufacturing (LOM), selective laser sintering (SLS), fused deposition modeling (FDM), solid ground curing (SGC), three dimensional printing (3DP_Binder Jetting), ballistic particle manufacturing (BPM), etc. Among them, SLA is the earliest and most widely used technology, accounting for about 70% of all rapid prototyping equipment.
Today we'll discuss the differences between SLA and SLS from four aspects.
The principle of SLA: use laser of a specific wavelength to solidify the resin.
The material of SLA is the category of resin.
The characteristics of SLA:
1. Stereolithography is the earliest rapid prototyping process, with high maturity and time-tested.
2. The prototype is made directly from the CAD digital model, with fast processing speed, short production cycle, and no need for cutting tools and molds.
3. It can process prototypes and molds with complex structures or difficult to form using traditional means.
4. Make CAD digital models intuitive and reduce the cost of error repair.
5. Provide samples for experiments can verify and check the results of computer simulation calculations.
6. It can be operated online and remotely controlled, which is conducive to production automation.
The disadvantages of SLA:
1. The SLA system is expensive to build, use and maintain.
2. The SLA system is a precision device that operates liquids and has strict requirements on the working environment.
3. Most molded parts are made of resin, which has limited strength, rigidity and heat resistance, and is not conducive to long-term storage.
The principle of SLA: heat the powder sintered to near melting point of the material and then add laser energy to sinter it.
The material of SLA is nylon and various materials and mixed materials.
The characteristics of SLS:
1. A variety of materials can be used. In principle, this method can use any powder material that reduces viscosity when heated, and can produce any shape through materials or various types of coated particles containing binders to meet different needs.
2. The manufacturing process is relatively simple. Since a variety of materials can be used, the selective laser sintering process can directly produce complex-shaped prototypes, cavity mold three-dimensional components or parts and tools according to the raw materials used.
3. No support structure is required. The overhanging layers that appear during the lamination process can be supported directly by the unsintered powder.
4. High material utilization rate. Since the process does not require a support structure, most of the powders used in the SLS process are relatively cheap, so the cost of the SLS model is relatively low.
5. Short production cycle. It only takes a few hours to dozens of hours from CAD design to the completion of parts processing. The entire production process is digitalized and can be modified and manufactured at any time. This feature makes it particularly suitable for the development of new products.
6. Combined with traditional process methods, it can realize functions such as rapid die casting, rapid molding and small batch manufacturing, injecting new vitality into traditional manufacturing methods.
7. Wide application. Due to the diversity of molding materials, the SLS process is suitable for a variety of application fields, such as prototype design verification, mold master, precision casting investment, casting shell and core, etc.
The disadvantages of SLS:
1. Rough surface. Since the raw material of SLS process are in powder form, the prototype is built by melting the powder layer by layer through heating. Therefore, strictly speaking, the surface quality of the prototype is not good enough as in powder form.
2. Polymer materials or powder particles generally emit odorous gases during laser sintering and melting.
3. Sometimes more complicated auxiliary processes are required. SLS technology varies depending on the materials used, and sometimes more complicated auxiliary processes are required, such as preheating the raw materials for a long time, cleaning the surface powder of the model after the modeling is completed, etc.
The advantage of RP prototype is its rapidity, but it is mainly formed by stacking technology, so RP prototype is generally relatively rough, and has centain requirements on the wall thickness of the product. For example, if the wall thickness is too thin, it cannot be produced.
Featured Product
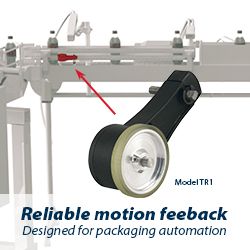