Additive Manufacturing Users Group Names Technical Competition Winners
A panel of industry veterans selected the University of Dayton Research Institute (UDRI) and Custom Prototypes as Advanced Concepts and Advanced Finishing winners. AMUG Members also selected UDRI for the Members' Choice Award.
The Additive Manufacturing Users Group (AMUG) today announced the winners of its annual Technical Competition, which recognizes excellence in additive manufacturing applications and finishing techniques. A panel of industry veterans selected the University of Dayton Research Institute (UDRI) and Custom Prototypes as Advanced Concepts and Advanced Finishing winners. AMUG Members also selected UDRI for the Members' Choice Award.
The Technical Competition took place at the annual AMUG Conference in Chicago, Illinois. Bonnie Meyer, Chair of the Technical Competition Committee, said, "I was so impressed with the entries this year. The quality displayed and the range of industries and applications was outstanding." She continued, "Every year, the judges have a bigger challenge to evaluate all of the high-quality entries. The entries just keep getting better and better!"
Ten judges scrutinized every detail of the competition entries to select Advanced Finishing and Advanced Concepts winners.
Custom Prototypes' winning entry in the Advance Finishing category was titled "Tomlinsonus Dimitrii - The oldest fossil of marine animal ever found." Representing the company's entry, Daniel Goncalves and Jung Kyu Im spearheaded the work to bring the 450-million-year-old fossil back to life. In collaboration with a University of Toronto science team, the pair created a digital model of the fossil and then printed it with stereolithography.
Goncalves and Im stated, "By carefully selecting the materials and post-processing systems, we managed to create various soft, hard, transparent, and opaque tissues of the animal." The pair noted that Custom Prototypes had developed a process that alters the properties of 3D-printed materials in terms of hardness and transparency. With the physical model complete, they then painstakingly prepared the piece and applied color to the delicate features of this sea creature.
Judges noted the impressive talent, craftsmanship, and artistry that went into the piece. One judge said, "It is clear that they have an advanced level of talent in painting. I saw techniques that I rarely see. A master level of their craft was apparent in the project."
Meyer said in her on-stage announcement of the Advanced Concepts winner, "I don't know where to start when talking about this category's highlights. There were so many unique entries that ranged from lifesaving to highly technical." She then named UDRI the Advanced Concepts winner for an additively manufactured micro-turbine engine submitted by Ben Loerke, who represented the organization's engineering team.
The program sponsor for the micro-turbine engine is the Environmental Security Technology Certification Program (ESTCP). Additionally, contributions of skills, talents, and resources were made by the Air Force Life Cycle Management Center (AFLCMC), with Michael Froning as the Principal Investigator, and Belcan Engineering.
The micro-turbine project used additive manufacturing to produce and test the novel design that has only four main components: rotor, housing, nozzle, and starter-motor mount. The team reduced the part count by nearly 90 percent compared to traditional designs.
The team employed a multi-disciplinary approach that leveraged the strengths, sidestepped the limitations, and pushed the boundaries of additive manufacturing. Its success also overcame the belief that additive manufacturing could not produce complex features while holding dimensional tolerances and delivering on surface finish specifications. Ben Loerke said, "The successes of this project have aided in redefining what was thought possible in metal AM design and in the use of metal AM for functional rotating hardware."
Loerke added, "The long-term goal of this project is to fill a growing DoD need for power plants that are sourced in a cost-effective and environmentally friendly manner. Based on a Life Cycle Analysis of the AM engine and similar traditional engines, it is believed that AM provides a unique opportunity to strike both of these criteria and fill this need in the micro-turbine engine market."
The competition judges selected the micro-turbine engine as the Advanced Concepts winner, recognizing the team's innovation, effort, and achievements. And one judge stated, "This project definitely has the 'wow' factor."
Through voting by AMUG's Members, UDRI also received the Members' Choice award. Meyer commented, "Unlike Advanced Concepts and Advanced Finishing, the Members' Choice award has no required evaluation criteria. It is open to personal and subjective impressions. This year, the members and judges came to the same conclusion. The micro-turbine engine was impressive in so many ways."
For Advanced Finishing, Dinsmore, Inc., represented by Bill Braune, took second place for "Transformers: Rise of Soundwave." Third place was awarded to Artcast Inc. for "Optimized Cast Tiger," submitted by Marcus Knoespel.
In Advanced Concepts, there was a tie for second place between Addman Engineering and Wilson. Mark Saberton represented Addman Engineering with "Non-coplanar Layering of 3D Printed Parts Rendering 'Slicing' Obsolete." Nadine Lippa represented Wilson for its entry, "Wilson Airless Prototype Basketball."
A representative of the UDRI and Custom Prototypes teams will receive complimentary admission to the 2024 AMUG Conference so that they can elaborate, from the stage, on the project details and processes used.
The Technical Competition judging panel was comprised of ten AMUG DINOs. These judges were David Flynn, Andrew Graves, David Leigh, Jason Lopes, Bruce LeMaster, Tom Mueller, Todd Reese, Harold Sears, Sean Wise, and Mark Wynn.
ABOUT ADDITIVE MANUFACTURING USERS GROUP (AMUG)
AMUG is an organization that educates and advances the uses and applications of additive manufacturing technologies. AMUG members include those with industrial additive manufacturing/3D printing solutions used for professional purposes from companies such as Dyndrite, GoEngineer, Nexa3D, Evonik, Tekna, DMG MORI, Stratasys, EOS, Würth Additive Group, Meltio, and ADDiTEC. AMUG meets annually to provide education and training through technical presentations on processes and new technologies. This information addresses the operation of additive manufacturing equipment and the applications that use the parts they make. Online at http://www.amug.com.
Featured Product
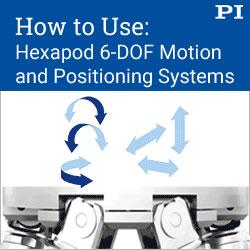