Materialise Announces Collaboration with HP, Nikon and Essentium to Support Adoption of 3D Printing
Materialise Streamics 8 improves connectivity with factory floor
Detroit (USA) - May 20. Materialise NV (Nasdaq: MTLS), a global leader in 3D printing solutions, has partnered with HP, Nikon and Essentium to bring improved productivity and connectivity to additive manufacturing operations. The partnerships, announced during the 2019 RAPID+TCT Conference in Detroit, will support the adoption of 3D printing by industrial manufacturers. Materialise also announced that it will release a new version of its 3D printing operations management software, Streamics 8 in June 2019.
The development of better machines, materials and software and advanced metal printing increasingly position 3D printing as a complementary technology for the production of final products. These advances have led to growing awareness among industrial manufacturers about the opportunities and competitive advantages it creates.
"To take advantage of large-scale 3D printing in an increasingly cost-competitive environment, manufacturing companies require increased productivity and efficiency and a seamless integration of 3D printing into their existing and proven production processes," says Fried Vancraen, Founder and CEO of Materialise. "Overcoming some of the remaining limitations attributed to 3D printing will require continued innovation and collaboration to create a more open market model with more control, more choice and ultimately lower cost."
At the 2019 Rapid+TCT Conference Materialise announced strategic collaborations and innovations to its flagship software suite that will drive the adoption of 3D printing and allow industrial manufacturers to scale their operations and transform their factory floors.
HP and Materialise collaborate to advance industrial-scale 3D printing
Materialise has expanded its collaboration with HP, developing a new version of its build processor to support the full range of printers in the HP Multi Jet Fusion portfolio, including the Jet Fusion 5200 and Jet Fusion 500/300 Series of 3D printing solutions. This provides customers with a seamless connection between the Materialise Magics 3D Print Suite and HP Jet Fusion printing solutions, enabling advanced data preparation and operation management. In addition, the Materialise HP Build Processor 2.0 allows users to retrieve operational data from the HP machines for better production monitoring. In combination with Materialise Streamics software, it allows users to store relevant build- data for improved traceability. The Materialise HP Build Processor 2.0 will be available in the second half of the year.
Customers who purchase an HP Jet Fusion 500/300 Series printer, will also gain access to the Materialise Magics Essentials software for a period of six months. This will allow customers to benefit from the advanced color and texture handling of Materialise's data preparation software, in combination with the full-spectrum color capabilities of the HP Jet Fusion 500/300 series.
Materialise runs one of the largest 3D print factories in the world and is one of the first to explore new applications and offer manufacturing services based on HP's new Jet Fusion 5200 Series printers. Materialise is also working with customers to develop innovative solutions for HP's new certified thermoplastic polyurethane (TPU), ULTRASINT™ developed by BASF, which is ideal for flexible and elastic parts.
HP has gained certification as part of Materialise's program to test and validate 3D printing technology as being fully compatible with Materialise Mimics and Mimics inPrint software. This certification allows medical professionals to use the HP Jet Fusion 580/380 3D printers, in combination with Mimics software technology, to print full-color anatomical models for diagnostic use and surgical planning, delivering broad benefits for patient-specific care.
Materialise was the first company in the world to receive FDA clearance for software intended for 3D printing anatomical models for diagnostic and surgical planning uses and introduced a program for manufacturers to have their printers tested and validated. With this certification, HP joins Formlabs, Stratasys and Ultimaker, bringing the total number of certified printer manufacturers to four.
For more information on Materialise's certification program, please visit the certifcation page.
Strategic collaborations with Nikon and Essentium
In today's cost-competitive environment, service-bureaus and industrial manufacturers increasingly rely on software and automation to increase productivity and efficiency in the 3D printing process. This is especially the case for metal 3D printing. Materialise collaborates with Nikon, a leading supplier of advanced opto-electronics and precision technologies, to improve insight into the 3D printing build process. These research activities, supported by Materialise software and the Materialise Control Platform, aim to provide users more control and increase productivity through analysis of the building process.
Materialise and Essentium, an innovator of disruptive 3D printing solutions for industrial additive manufacturing, entered into a strategic partnership in November 2018 to jointly advance and scale industrial 3D printing. In a first step towards that goal, the companies have announced the integration of Materialise's Magics Essentials software with the Essentium High Speed Extrusion (HSE) 3D Printing Platform. This creates an open and complete platform for industrial scale 3D manufacturing without the need to compromise accuracy or speed.
Materialise Streamics 8: better connectivity with the industrial factory floor
"Despite increased awareness about the potential of connected, industrial-scale 3D printing, in-house 3D printing production processes are often still isolated hubs," said Stefaan Motte, Vice President and General Manager of the Materialise software division. "With the introduction of Streamics 8, our software tool to manage and streamline 3D printing operations, Materialise wants to transform those isolated hubs into productive and integrated production facilities, by connecting to existing production management systems and adding specific additive manufacturing execution capabilities."
The fully configurable web-portal allows remote design departments to better interact with the production floor for optimized designs and minimized production costs. The web-based API enables easier integration of the 3D Printing production environment with existing business and manufacturing IT systems. This represents an important step towards making 3D printing an integral part of the overall manufacturing process.
Streamics 8 also offers several advanced features to help increase productivity, including automatic nesting across multiple build platforms, for a more efficient build preparation. This allows users to simply drag and drop multiple parts into the build planner, which automatically nests the parts and creates the appropriate number of build operations. This automated nesting process can significantly reduce annual labor cost.
With the introduction of Streamics 8, Materialise paves the way towards Digital Rights Management (DRM) in 3D printing. DRM provides manufacturers a safe and secure way to print high-value end-parts and to scale operations over a global distributed manufacturing network. By enabling the protection of designs, Streamics 8 offers peace of mind to manufacturers who demand a more secure production environment. Materialise is working with partners to establish a true end-to-end, secure 3D printing manufacturing process, allowing users to restrict the printing of a file to a pre-defined printer and guarantee the exact build quality or to limit the number of reprints.
Scaling 3D printing production also requires full traceability of each individual component. Streamics 8 automatically stores all relevant build data, such as serial numbers, process parameters and part revisions, and makes this data available at all times. With Streamics 8, Materialise supports both text labels and Data Matrix Labels. Data Matrix Labels convert the alphanumerical data from standard 3D-printed labels into a data matrix code that can be automatically applied to individual parts. These smart tags are smaller and machine-readable, reducing human error and further automating the post-production process.
With Streamics 8, Materialise announces support for MTConnect, allowing better monitoring for MTConnect-enabled machines, such as select Stratasys 3D printers. In addition, Streamics 8 offers better machine monitoring for Arcam and HP printers through dedicated build processors. Live monitoring of vital machine parameters on the Streamics dashboard, including machine state and elapsed production time, provides operators with more control of the production process and improves overall productivity. Materialise believes open factory standards are important to enable better connectivity and more efficient operations and plans to support other machine communication standards, such as OPC-UA, in the future.
Streamics 8 will be available in June 2019. More information.
Advanced simulation features
In addition, Materialise introduces the second version of its simulation software, which offers significant speed improvements and advanced simulation features. Materialise Simulation 2.0 makes simulation easy to manage and accessible to a wider audience. It allows operators to predict and analyze the behavior of a part during physical production by creating a virtual prototype. This helps to optimize the build preparation and reduces the number of costly reprints and fails.
The new version offers speed improvements of up to nine times for file management and is capable of handling larger files. New simulation features include ‘part compensation', which allows users to predict and compensate heat-related part deformation. The new version also makes it possible to simulate heat diffusion, which prevents overheating during the print process. Materialise Simulation 2.0 is available as an optional module with Materialise Magics 23.
Attendees at the RAPID + TCT Conference can learn more by visiting Materialise at booth 1417at Cobo Center in Detroit May 20-23, 2019.
About Materialise
Materialise incorporates nearly three decades of 3D printing experience into a range of software solutions and 3D printing services, which together form the backbone of the 3D printing industry. Materialise's open and flexible solutions enable players in a wide variety of industries, including healthcare, automotive, aerospace, art and design, and consumer goods, to build innovative 3D printing applications that aim to make the world a better and healthier place. Headquartered in Belgium, with branches worldwide, Materialise combines the largest group of software developers in the industry with one of the largest 3D printing facilities in the world.
For additional information, please visit: www.materialise.com.
Featured Product
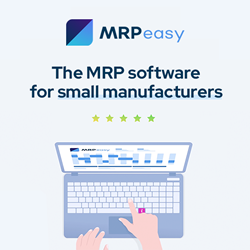