PACK EXPO Presentations Geared to Help Improve Manufacturing Operations
Topics to focus on helping customers implement best practices across the enterprises
Milwaukee; Aug. 30, 2018 - Professionals who attend this years PACK EXPO International and Healthcare Packaging EXPO in Chicago, Oct. 14-17, can learn about the latest smart manufacturing techniques aimed at delivering value across the enterprise. This year, Rockwell Automation will conduct a series of presentations and demonstrations for end users, machine and equipment builders in packaging and related industries to share the most recent innovations in independent cart technology, analytics and network security.
Rockwell Automation subject matter specialists will present at the PACK EXPO International and Healthcare Packaging EXPO Innovation Stages, featuring the following topics:
• Smart Flexible Manufacturing: Oct. 14 at 2 p.m. in Booth N-4560 - How companies are leveraging innovative technologies to add more flexibility into manufacturing
• Advanced Technology in Life Sciences: Oct. 15 at 11 a.m. in Booth W-320 - How business models in life science manufacturing are evolving to support changing market demands
• Analytics for Delivering Business Value in Industrial IoT: Oct. 15 at 2 p.m. in Booth N-4560 - Why big data will become less relevant in the future and increasingly be replaced with contextualized data and digital twins that are embedded in devices, machines and the cloud
• Cybersecurity in Manufacturing Operations: Oct. 16 at 10 a.m. in Booth N-4560 - Recommendations on best practices and actionable steps industrial companies can take with reference to network security and standards within the industry
"At PACK EXPO International and Healthcare Packaging EXPO, attendees can learn how they can leverage analytics to help generate increased productivity and flexibility in their operations," said Steve Mulder, OEM packaging and segment leader, Rockwell Automation. "We look forward to sharing the latest in automation technology and offering new solutions for machine designers and end users."
Attendees can also visit Booth E-8043 to see the iTRAK and MagneMover Lite motion control systems from Rockwell Automation. Designed for the precise movement, positioning and tracking of loads, these modular, scalable motion control systems can increase throughput and efficiency in applications such as packaging, pharmaceutical manufacturing, sterile and aseptic filling, lab automation and medical device manufacturing.
In conjunction with its participation in PACK EXPO International, Rockwell Automation is a title sponsor of the PACK gives BACK™ benefit event on Oct. 15 featuring Chicago-based comedian Sebastian Maniscalco. A portion of the proceeds from this event will go to the PACK EXPO Scholarship, which supports students pursuing advanced degrees in packaging or processing at PMMI partner schools. Tickets can be purchased at packexpo.com.
About Rockwell Automation
Rockwell Automation Inc. (NYSE: ROK), the worlds largest company dedicated to industrial automation and information, makes its customers more productive and the world more sustainable. Headquartered in Milwaukee, Wis., Rockwell Automation employs approximately 22,000 people serving customers in more than 80 countries.
Featured Product
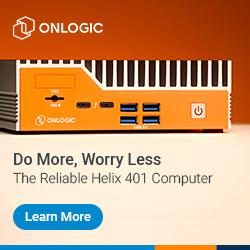