FABTECH - Making the Cut with KUKA Robotics Corporation at FABTECH 2015 Chicago
Innovative welding developments and solutions from KUKA Robotics at FABTECH 2015 in booth N-18013 November 9th – November 12th, 2015
SHELBY TOWNSHIP, Mich.--KUKA Robotics will be in booth N-18013 exhibiting among 1,500+ world-class industry suppliers at Fabtech Chicago. Fabtech is North Americas largest metal forming, fabricating, welding and finishing event.
Official KUKA Robotics System Partner PDSI will showcase their plasma cutting cell for structural steel and tubing - The Predator. This robotic development features a KUKA KR 16 L8 arc HW robot with KR C4 to provide the ultimate in cutting reach and precision for this cell. The Predator from PDSI offers an all-in-one steel processing system to cut steel, time and cost. Attendees will have the opportunity to see the cell at work with I-beam tracing utilizing the KR 16 L8 arc HW when visiting the booth.
In addition to The Predator, KUKA will feature Official System Partner ARC Specialties robotic plasma cutting cell also operating a KR 16 L8 arc HW robot. The KR 16 L8 arc HW offers a hollow wrist, high repeatability, and a reach of 2,000mm. The hollow wrist opening of the robot allows for optimal protection of the arc welding dress package by being routed in the protective interior of the robotic arm. This innovative solution from ARC Specialties will be doing live plasma cutting, showcasing the single axis head stock/tail stock design permits rotational cutting of complex parts, with pre-programmed cutting geometry with desired part dimensions requires no programming of the robot.
KUKA Robotics will have the new KR AGILUS HM - the JoeBot, attendees personal barista - on display. The KR AGILUS HM (Hygienic Machine) meets industry requirements for both food and pharmaceuticals. This small robot emphasizes the importance of a hygienic design with a higher protection rating IP 67. The KR AGILUS HM has corrosion-resistant surfaces to prevent build-up of sensitive materials while even being used in temperature ranges between 0oC to 40oC. Offering a payload range of 6kg to 10kg with a reach of 700mm to 1,100mm, the KR AGILUS HM adds new potential to the AGILUS family.
Another demonstration attendees will find in KUKAs booth is from Official System Partner Genesis Systems Group, LLC. This Genesis cell will have on display 4 KR AGILUS and a KR 120 R3900 ULTRA K. The Genesis RoboPogo system offers flexibility, scalability to fit customer applications, and multi-dimensional positioning. The KR AGILUS is KUKA Robotics new family of small robots. Availability is offered in two payloads of 6kg and 10kg with a reach of 700, 900, and 1,100mm. The KR QUANTEC ultra family offers extreme power, stiffness, and precision with 25% shorter cycle times.
The KUKA Robotics System Partner network is designed to mutually benefit each organizations users by extending the way customers can acquire tailored solutions with the major competitive and technological advantage of high precision KUKA robots. The KUKA Robotics System Partner Network includes experienced OEM machine builders, system providers, application specialists and expert robot integrators.
About the KUKA Robot Group
KUKA Robotics Corporation along with KUKA Roboter GmbH, Augsburg Germany (part of the KUKA Aktiengesellschaft group of worldwide companies), ranks among the worlds leading suppliers of industrial robots and material handling vehicles. Core competencies include the development, production, and sale of industrial robots, controllers, software, linear units, and omniMove omni-directional motion platforms. KUKA robots are utilized in a diverse range of industries including the appliance, automotive, aerospace, consumer goods, logistics, food, pharmaceutical, medical, foundry and plastics industries as well as multiple applications including material handling, machine loading, assembly, packaging, palletizing, welding, bending, joining, and surface finishing. KUKA robots range from 5kg to 1300kg payloads, and 635mm to 3900mm reach, all controlled from a common PC based controller platform.
Featured Product
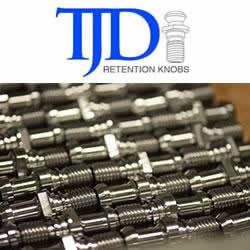
T.J. Davies' Retention Knobs
Our retention knobs are manufactured above international standards or to machine builder specifications. Retention knobs are manufactured utilizing AMS-6274/AISI-8620 alloy steel drawn in the United States. Threads are single-pointed on our lathes while manufacturing all other retention knob features to ensure high concentricity. Our process ensures that our threads are balanced (lead in/lead out at 180 degrees.) Each retention knob is carburized (hardened) to 58-62HRC, and case depth is .020-.030. Core hardness 40HRC. Each retention knob is coated utilizing a hot black oxide coating to military specifications. Our retention knobs are 100% covered in black oxide to prevent rust. All retention knob surfaces (not just mating surfaces) have a precision finish of 32 RMA micro or better: ISO grade 6N. Each retention knob is magnetic particle tested and tested at 2.5 times the pulling force of the drawbar. Certifications are maintained for each step in the manufacturing process for traceability.