Touch International Adds 3D Printing and Increase Laser Etching for Rapid Prototyping
New 3D printing and laser etching capacity helps Touch International rapidly develop complete touch screen display solutions through rapid prototyping, shortening product development lifecycles, increased quality control, and an optimized supply chain.
Austin, Texas October 29, 2015 -- Touch International announced today that it has added 3D printing and increased laser etching capacities to its Austin, Texas, manufacturing and design center to aid in the development of rapid prototyping for custom touch screen display solutions.
The increased capabilities are part of the company's evolution from touch screens, EMI filters and display enhancements, to developing complete touch displays that include a bezel, video controller boards, metal frames and backers, gaskets, and even single board computers . Focusing on professional grade products, TI targets high reliability markets such as medical, military, industrial, aerospace, transportation, and more. Vertically integrated manufacturing capabilities, strategic acquisitions, and extensive experience allow TI to quickly engineer products that meet or exceed stringent industry requirements and certifications.
"Our 3D Printing and laser etching services give our customers more options so that they can perfect the end products look, feel and functionality in a reduced amount of time without having to coordinate multiple vendors," explains Shaun Detmer, director of Marketing, Touch International. "While our competitors continue to outsource manufacturing, we continue to drive our vertical integration capabilities and control every step of the development process while simultaneously optimizing our supply chain and quality control."
The 3D printing and rapid prototyping capabilities, also known as additive manufacturing, will help shorten costly product development lifecycles and improve design testing and verification, saving customers time and money on product development and testing, getting products to market faster, and building a better end-user experience. 3D printing and additive manufacturing also reduce the amount of waste thats produced during the manufacturing process, printing only what is needed, layer by layer, making the process environmentally friendly and cost effective.
3D printing and other forms of additive manufacturing for rapid prototyping is currently used primarily by OEMs (Original Equipment Manufacturers), such as Touch International, to build prototypes in the military, aerospace, medical and automotive spaces. Analysts at Wohlers Associates expect the rapid prototyping market to grow 300% over the next decade jumping from $1.5 billion in 2012 to more than $5 billion by 2020 as applications grow from rapid prototyping into full-scale production for some medical and aerospace devices. (1)
About 3D Printing, Rapid Prototyping and Additive Manufacturing
The term rapid prototyping is typically used in association with additive manufacturing and 3D printing technologies and is commonly applied at the beginning of a product life cycle to create prototypes or parts that can be used to test or verify designs before full blown production begins. 3D printers work off of a 3D CAD design (computer model) and "print" very thin 2D layers on top of each other to form a 3D physical object. (2)
About Touch International
Touch International, headquartered in Austin, Texas, was founded in 2002 by Michael Woolstrum and long-time veteran, Gary Barrett, the companys CTO. TI has become a world leader in professional grade touch screen display manufacturing. The company operates its engineering and design facility and corporate headquarters in Austin, Texas, as well as a high volume production facility located in Shenzhen, China.
(1) http://www.siemens.com/innovation/en/home/pictures-of-the-future/industry-and-automation/Additive-manufacturing-facts-and-forecasts.html
(2) https://www.solidconcepts.com/applications/rapid-prototyping/
Featured Product
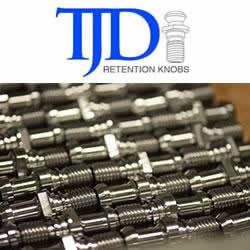
T.J. Davies' Retention Knobs
Our retention knobs are manufactured above international standards or to machine builder specifications. Retention knobs are manufactured utilizing AMS-6274/AISI-8620 alloy steel drawn in the United States. Threads are single-pointed on our lathes while manufacturing all other retention knob features to ensure high concentricity. Our process ensures that our threads are balanced (lead in/lead out at 180 degrees.) Each retention knob is carburized (hardened) to 58-62HRC, and case depth is .020-.030. Core hardness 40HRC. Each retention knob is coated utilizing a hot black oxide coating to military specifications. Our retention knobs are 100% covered in black oxide to prevent rust. All retention knob surfaces (not just mating surfaces) have a precision finish of 32 RMA micro or better: ISO grade 6N. Each retention knob is magnetic particle tested and tested at 2.5 times the pulling force of the drawbar. Certifications are maintained for each step in the manufacturing process for traceability.