PACK EXPO - Novation Industries Exhibiting at Pack Expo Las Vegas September 28-30, 2015
Novation Industries is exhibiting at a major International trade show in Las Vegas. The company is offering complimentary design consultations by their top packaging designer and will also be educating attendees on their unique development process.
McHenry, IL September 24, 2015
Novation Industries specializes in custom manufacturing solutions and integrated product development services including design, injection molding and sourcing, contract manufacturing, and logistics. Specialty packaging solutions include closures, valves, pumps, containers, dispensers, lids, caps, and other packaging components. Novation packaging expertise includes a variety of vertical markets including packaging, automotive, industrial, electronics, medical, consumer and merchandising.
Company president, Scott Baxter, explains, "Our companys high facility standards and ongoing commitment to continuous improvement provide clean, low particulate manufacturing environments and excellent IDP practices, which allows us to service multiple packaging markets." Executive team members will be on site at Pack Expo to discuss the companys extensive packaging capabilities as well as their unique Integrated Development Process (IDP), used in developing new packaging solutions. IDP is used for enlisting multiple disciplines into a cross-functional organization to ensure rapid, yet marketable design, functionally technical development and an efficient production approach in the manufacturing of plastic injection molded parts and assemblies.
At Pack Expo, the companys top packaging partner, Dieter Lay, will be providing project design reviews, including analyzing Total Cost of Ownership. Lay provides turnkey product design and development of injection molded parts, specializing in packaging and medical components. Lay comments, "We enjoy meeting people with generic ideas and taking them to the next level into something that is reliably manufacturable." The company will be giving away complimentary design consultations and a chance to win a new Apple iPad at Pack Expo booth S-6771.
Novation Industries employs a well-qualified staff of approximately 150 who showcase extensive knowledge and talent within the facility. The group of seven lead executives at Novation Industries bring almost 200 years of combined product development experience. Baxter notes, "What sets Novation Industries apart from the competition is our compliance to develop products with impact by carefully employing the best ergonomic, esthetic and materials selection design considerations." The companys ongoing commitment to growth also includes the purchase of four new electric presses, ranging from 150 to 400 ton capacity. Baxter adds, "We are thrilled to share our innovative injection molding processes and product development techniques with potential customers at the show."
Novation Industries, established in 1967, is a full-service custom plastics injection molding company that specializes in integrative packaging development. The McHenry, IL based company is known for its pristine facility that stimulates the use of design, state of the art engineering and high-tech manufacturing. Novation Industries core ideology drives innovation, efficiency and a customer-centric focus.
Featured Product
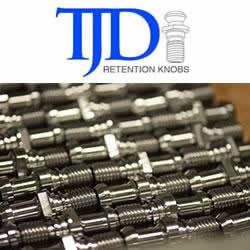
T.J. Davies' Retention Knobs
Our retention knobs are manufactured above international standards or to machine builder specifications. Retention knobs are manufactured utilizing AMS-6274/AISI-8620 alloy steel drawn in the United States. Threads are single-pointed on our lathes while manufacturing all other retention knob features to ensure high concentricity. Our process ensures that our threads are balanced (lead in/lead out at 180 degrees.) Each retention knob is carburized (hardened) to 58-62HRC, and case depth is .020-.030. Core hardness 40HRC. Each retention knob is coated utilizing a hot black oxide coating to military specifications. Our retention knobs are 100% covered in black oxide to prevent rust. All retention knob surfaces (not just mating surfaces) have a precision finish of 32 RMA micro or better: ISO grade 6N. Each retention knob is magnetic particle tested and tested at 2.5 times the pulling force of the drawbar. Certifications are maintained for each step in the manufacturing process for traceability.