How CNC Turning Is Revolutionizing Precision Manufacturing
In this article, we will explore the fundamentals of CNC turning, its key components, how it works, and how it is reshaping the landscape of precision manufacturing.
Understanding CNC Turning
Key Components of CNC Turning
CNC Lathe Machine: The heart of the CNC turning process is the CNC lathe machine. It consists of a rotating spindle that holds the workpiece and a tool turret that holds various cutting tools. The CNC lathe is capable of performing multiple operations such as turning, boring, drilling, and threading, all of which are essential for precision machining.
Computer Program: The cutting path, spindle speed, tool changes, and other parameters are all controlled by a computer program. The most common programming language used is G-code, which directs the CNC machine to perform specific tasks with extreme accuracy.
Cutting Tools: Various cutting tools are used in CNC turning, such as drills, lathes, and boring bars. These tools are specifically designed for specific tasks, such as removing material or creating precise threads. The right tool selection is crucial to achieving the desired surface finish and accuracy.
Coolant Systems: Cooling and lubrication systems are an essential part of CNC turning. They help reduce heat generation, prevent tool wear, and improve the quality of the surface finish by reducing friction between the cutting tool and the workpiece.
How CNC Turning Works
The process of CNC turning involves several key steps:
Setup: The first step involves securely mounting the workpiece on the CNC lathe's spindle. The machine must be calibrated to ensure that the workpiece is centered and aligned properly.
Programming: Using CAD (Computer-Aided Design) and CAM (Computer-Aided Manufacturing) software, engineers input the design specifications of the part to be produced. The software generates a precise program (often in G-code) that instructs the CNC machine on how to execute the required cuts and shapes.
Machining: The CNC lathe follows the instructions encoded in the program. As the machine operates, the cutting tool removes material from the rotating workpiece to shape it into the desired form. The program ensures that all movements are executed with high precision, allowing for the creation of complex geometries and features.
Finishing: Once the part is machined, it may undergo additional processes such as polishing, coating, or heat treatment to achieve the desired surface finish and mechanical properties.
Impact on Precision Manufacturing
CNC turning is a game-changer in precision manufacturing. Here's how:
Enhanced Accuracy and Precision: CNC turning allows for extremely tight tolerances, often within a few microns. This high level of accuracy ensures that the parts produced meet stringent specifications, reducing the need for rework and ensuring consistency.
Increased Production Efficiency: With CNC turning, operators can run machines continuously with minimal supervision. The high level of automation results in faster cycle times and reduced human error, leading to greater throughput.
Ability to Produce Complex Geometries: Traditional manual turning machines were limited in the complexity of shapes they could produce. CNC turning, however, allows manufacturers to create intricate shapes and features with high precision, which were previously difficult or impossible to achieve manually.
Cost-Effectiveness: While the initial setup costs for CNC turning may be higher compared to manual machining, the long-term benefits far outweigh the costs. Automation leads to higher throughput, reduced scrap rates, and less need for skilled labor, all of which contribute to cost savings over time.
Applications in Various Industries
CNC turning is used in a wide range of industries, each benefiting from the precision, speed, and versatility of this technology.
- Aerospace: CNC turning plays a crucial role in manufacturing high-precision components for the aerospace industry. From turbine blades to engine components, CNC turning ensures that the parts meet stringent safety and performance requirements.
- Automotive: In the automotive sector, CNC turning is used to produce engine blocks, crankshafts, camshafts, and other components that require high precision and durability. The technology allows for the production of high-performance parts that can withstand extreme operating conditions.
- Medical Devices: CNC turning is used to create surgical tools, implants, and other medical devices with exacting tolerances. The ability to produce small, complex parts with precision is essential in the medical field, where quality and reliability are critical.
- Electronics: From connectors to housings, CNC turning is widely used in electronics manufacturing. The technology's ability to create intricate parts with high surface finishes ensures that these components fit together perfectly and function reliably.
Advancements in CNC Turning Technology
CNC turning continues to evolve, with several advancements pushing its capabilities further:
Integration with AI and Machine Learning: Artificial intelligence and machine learning algorithms are being incorporated into CNC turning machines. These technologies optimize machining parameters, predict tool wear, and even adjust processing conditions in real-time, further enhancing efficiency and productivity.
Advanced Materials: CNC turning is now capable of machining a broader range of materials, including high-strength alloys, composites, and ceramics. As material science advances, CNC turning machines are designed to handle these challenging materials, expanding the range of applications.
Automation and Robotics: The integration of robotics with CNC turning machines allows for 24/7 production with minimal human intervention. Robots are used for tasks such as loading and unloading the workpieces, changing tools, and even quality inspection, further improving efficiency.
Challenges and Considerations
Despite its many advantages, CNC turning does present some challenges:
High Initial Investment: CNC machines and the associated software require a significant upfront investment. This can be a barrier for smaller companies or those with limited capital.
Skilled Workforce: CNC turning requires skilled operators who can program the machines and troubleshoot issues. The growing complexity of the technology demands highly trained personnel.
Maintenance: CNC turning machines need regular maintenance to ensure optimal performance. Without proper care, machine downtime and production delays may occur.
Conclusion
CNC turning has revolutionized precision manufacturing, providing a high degree of accuracy, speed, and flexibility. The ability to produce complex and high-tolerance parts with minimal human intervention has transformed industries and opened up new possibilities for innovation. As CNC turning continues to evolve with the integration of AI, robotics, and advanced materials, it will remain a cornerstone of modern manufacturing, driving efficiency and meeting the growing demands of industries worldwide.
By understanding how CNC turning works and embracing its potential, engineers and manufacturers can ensure their competitiveness in an increasingly automated and precise world.
Featured Product
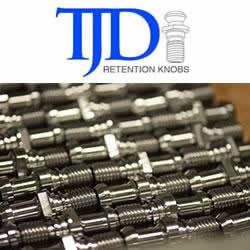
T.J. Davies' Retention Knobs
Our retention knobs are manufactured above international standards or to machine builder specifications. Retention knobs are manufactured utilizing AMS-6274/AISI-8620 alloy steel drawn in the United States. Threads are single-pointed on our lathes while manufacturing all other retention knob features to ensure high concentricity. Our process ensures that our threads are balanced (lead in/lead out at 180 degrees.) Each retention knob is carburized (hardened) to 58-62HRC, and case depth is .020-.030. Core hardness 40HRC. Each retention knob is coated utilizing a hot black oxide coating to military specifications. Our retention knobs are 100% covered in black oxide to prevent rust. All retention knob surfaces (not just mating surfaces) have a precision finish of 32 RMA micro or better: ISO grade 6N. Each retention knob is magnetic particle tested and tested at 2.5 times the pulling force of the drawbar. Certifications are maintained for each step in the manufacturing process for traceability.